Stiffness-Performance-Based Redundant Motion Planning of a Hybrid Machining Robot
MACHINES(2022)
摘要
Large-scale components usually have complex structures with high local stiffness, and the holes on them are required to be machined with high precision, which makes it important and challenging to study how to efficiently and precisely drill in the large-scale components. This article presents mobile hybrid machining equipment that consists of a five-axis parallel module, a 2-degree-of-freedom (DoF) robotic, arm and an automated guide vehicle (AGV) connected in series. With the ability of wide-range positioning and precise local processing, it has potential advantages in the drilling processing of large-scale components. Stiffness is one of the most important performances for machining equipment, and it's highly related to the its configuration. For the discussed equipment, the stiffness is determined by the two-stage-positioning hybrid machining robot, which comprises a five-axis parallel module and a two-DoF robotic arm. The redundant motion of the hybrid machining robot makes it possible to optimize its configuration by reasonably planning redundant motion. Therefore, a redundant motion-planning method based on stiffness performance is proposed. A kinematic analysis of the five-axis parallel module, the robotic arm, and the hybrid machining robot is carried out. A hybrid robot usually consists of several subsystems, and to take the compliance of each subsystem into consideration, the stiffness-modeling method for the hybrid robot with n subsystems connected in series is proposed. The stiffness model of the hybrid machining robot is established by using this method, and the variation of the stiffness magnitude has the same trend as that obtained by using FEA software. Stiffness magnitude and isotropy indices are proposed to evaluate the robot's stiffness performance along the axis of the spindle and in the plane perpendicular to the axis of the spindle. The redundant motion of the hybrid machining robot is planned by maximizing the stiffness magnitude along the spindle axis, with priority to the stiffness isotropy index. Finally, the drilling experiment is carried out, and the results show that the relative error of the hole diameter obtained under the optimal configuration of the hybrid machining robot is 1.63%, which is smaller than those obtained under the other two configurations for comparison with relative errors of 3.75% and 3.50%, respectively. It proves the validity of the redundant motion-planning method. The proposed stiffness-modeling method and the stiffness-performance indices are also applicable to other hybrid machining robots.
更多查看译文
关键词
hybrid robot,stiffness modeling,redundant motion planning,stiffness performance index
AI 理解论文
溯源树
样例
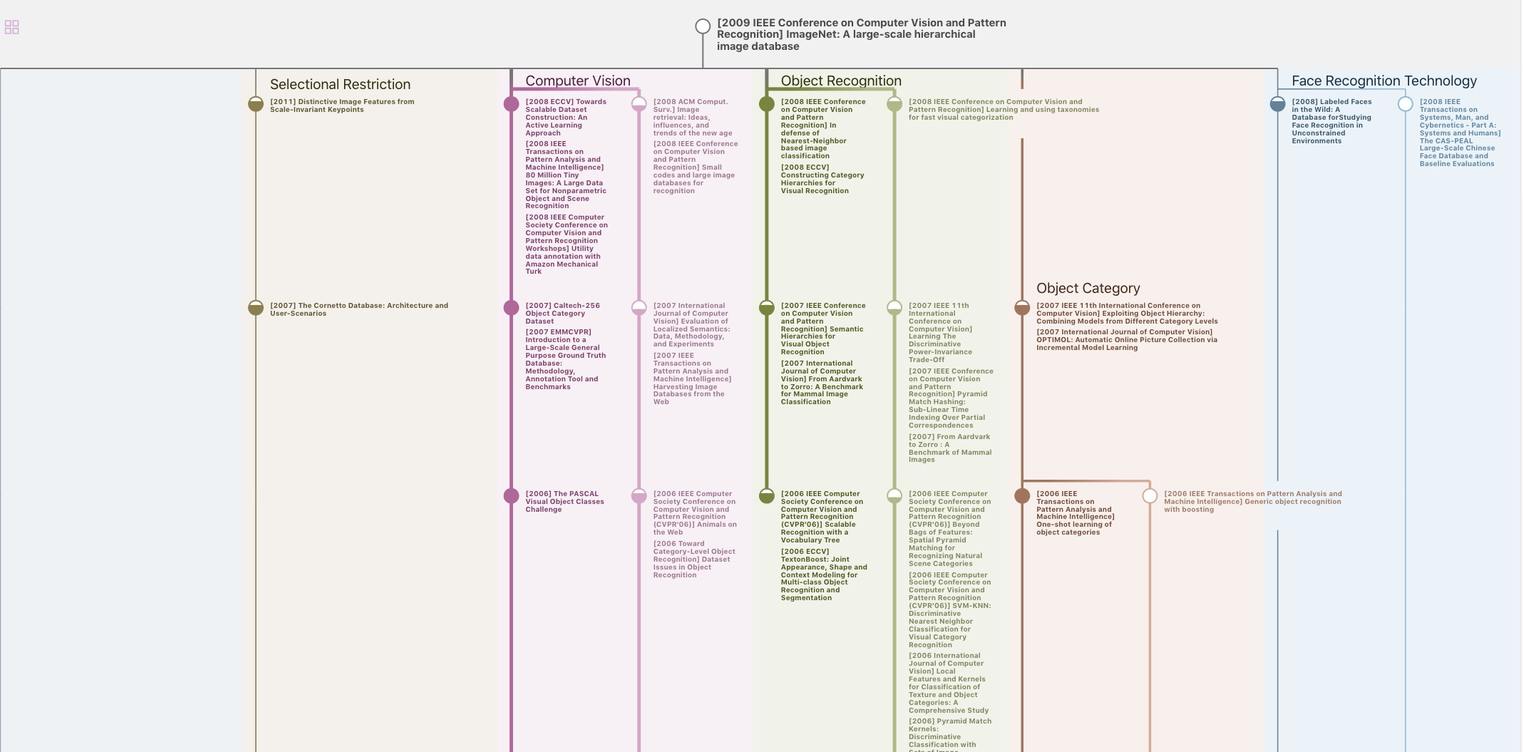
生成溯源树,研究论文发展脉络
Chat Paper
正在生成论文摘要