Low-Force Elastocaloric Refrigeration Via Bending
APPLIED PHYSICS LETTERS(2021)
摘要
Elastocaloric cooling has been identified as a promising alternative to high global warming potential vapor compression cooling. Two key bottlenecks to adoption are the need for bulky/expensive actuators to provide sufficient uniaxial stress and inadequate elastocaloric material fatigue life. This paper defines the physics that govern the performance of axisymmetric flexural bending for use as an emerging low-force and low-fatigue elastocaloric heating and cooling mechanisms and further demonstrates a continuous rotary-driven cooling prototype using polycrystalline Ni50.75Ti48.74. Elastocaloric material performance is determined using infrared thermography during uniaxial-tension and four-point bending thermomechanical testing. A systematic study reveals the effects of strain rate (from 0.001 to 0.025 s(-1)), maximum strain (from 2 to 8%), and strain mode on the temperature evolution, mechanical response, and coefficient of performance. Four-point bending experiments demonstrate a temperature reduction of up to 11.3 degrees C, material coefficients of performance between 2.31 and 21.71, and a 6.09- to 7.75-fold reduction in the required actuation force compared to uniaxial tension. The absence of localized macroscopic martensite domains and reduced mechanical dissipation during flexure represent reduced microstructure degradation and improved fatigue life. The rotary-based elastocaloric cooling prototype is shown to provide similar thermomechanical performance with the added benefit of discrete hot and cold zones, continuous cooling, inexpensive rotary actuation, and scalability, which represents a significant advancement for compact, long lifetime, and inexpensive elastocaloric cooling.
更多查看译文
关键词
elastocaloric refrigeration,low-force
AI 理解论文
溯源树
样例
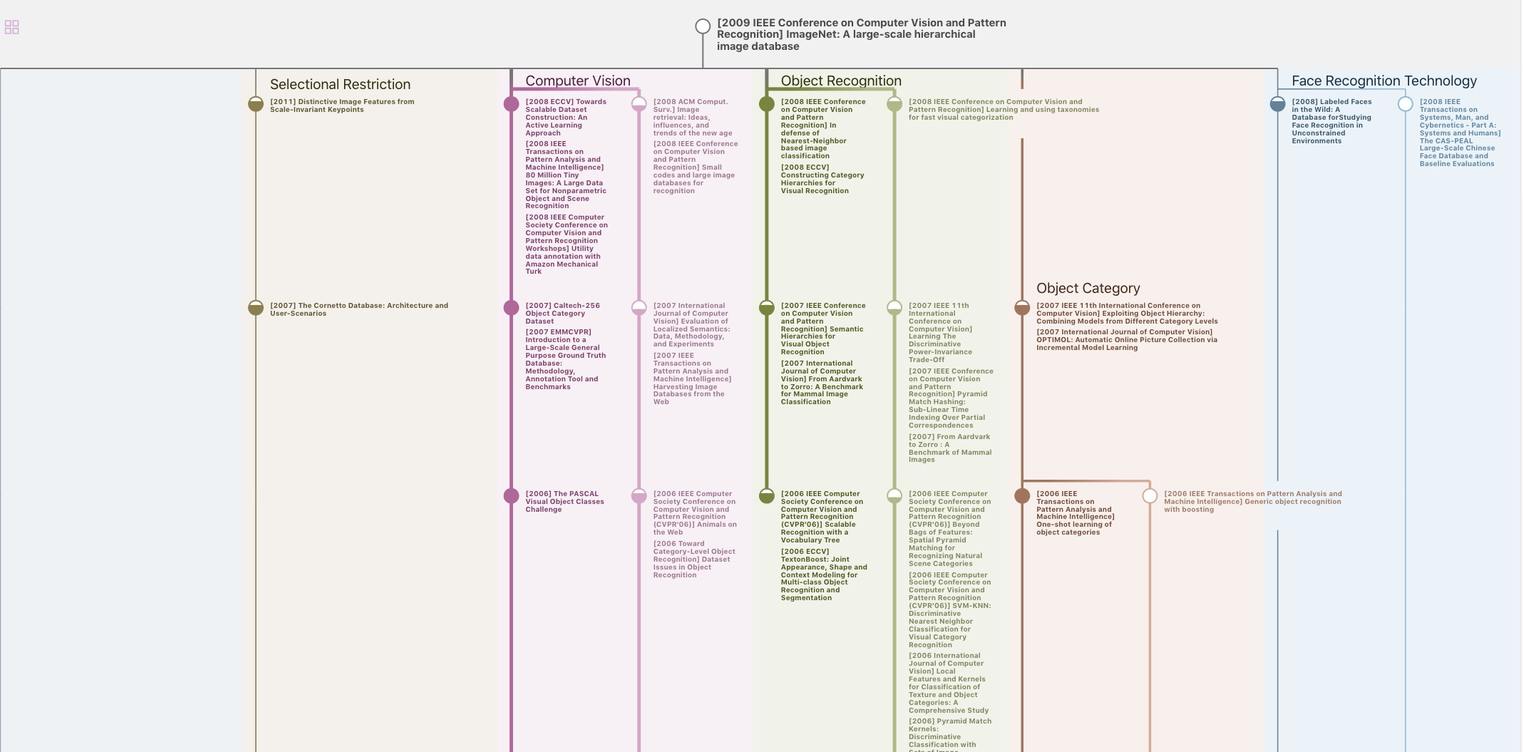
生成溯源树,研究论文发展脉络
Chat Paper
正在生成论文摘要