Process Characterizations of Ultrasonic Extruded Weld-Riveting of AZ31B Magnesium Alloy to Carbon Fiber-Reinforced PA66.
Polymers(2024)
Abstract
Traditional metal-plastic dissimilar welding methods directly heat the metal workpiece, which may cause potential thermal damage to the metal workpiece. Ultrasonic extruded weld-riveting (UEWR) is a relatively new method for dissimilar joining of carbon fiber-reinforced thermoplastic (CFRTP) and metal. In this method, the CFRTP workpiece is melted using the ultrasonic effect and is squeezed into prefabricated holes in the metal workpiece to form a rivet structure. In this method, the metal workpiece is not directly heated, and potential high-temperature losses can be avoided. This paper investigates the process characterizations of UERW of AZ31B magnesium alloy to carbon fiber-reinforced PA66. The process parameters are optimized by the Taguchi method. The joint formation process is analyzed based on the fiber distribution in the cross-sections of joints. The effects of welding parameters on the joint microstructure and fracture surface morphology are discussed. The results show that a stepped amplitude strategy (40 μm amplitude in the first stage and 56 μm amplitude in the second stage) could balance the joint strength and joint appearance. Insufficient (welding energy < 2600 J or amplitude-A < 50%) or excessive (welding energy > 2800 J or amplitude-A > 50%) welding parameters lead to the formation of porous defects. Three fracture modes are identified according to the fracture surface analysis. The maximum tensile shear strength of joints at the optimal parameters is about 56.5 ± 6.2 MPa.
MoreTranslated text
Key words
ultrasonic extruded weld-riveting,dissimilar joining,carbon fiber-reinforced thermoplastic,magnesium
AI Read Science
Must-Reading Tree
Example
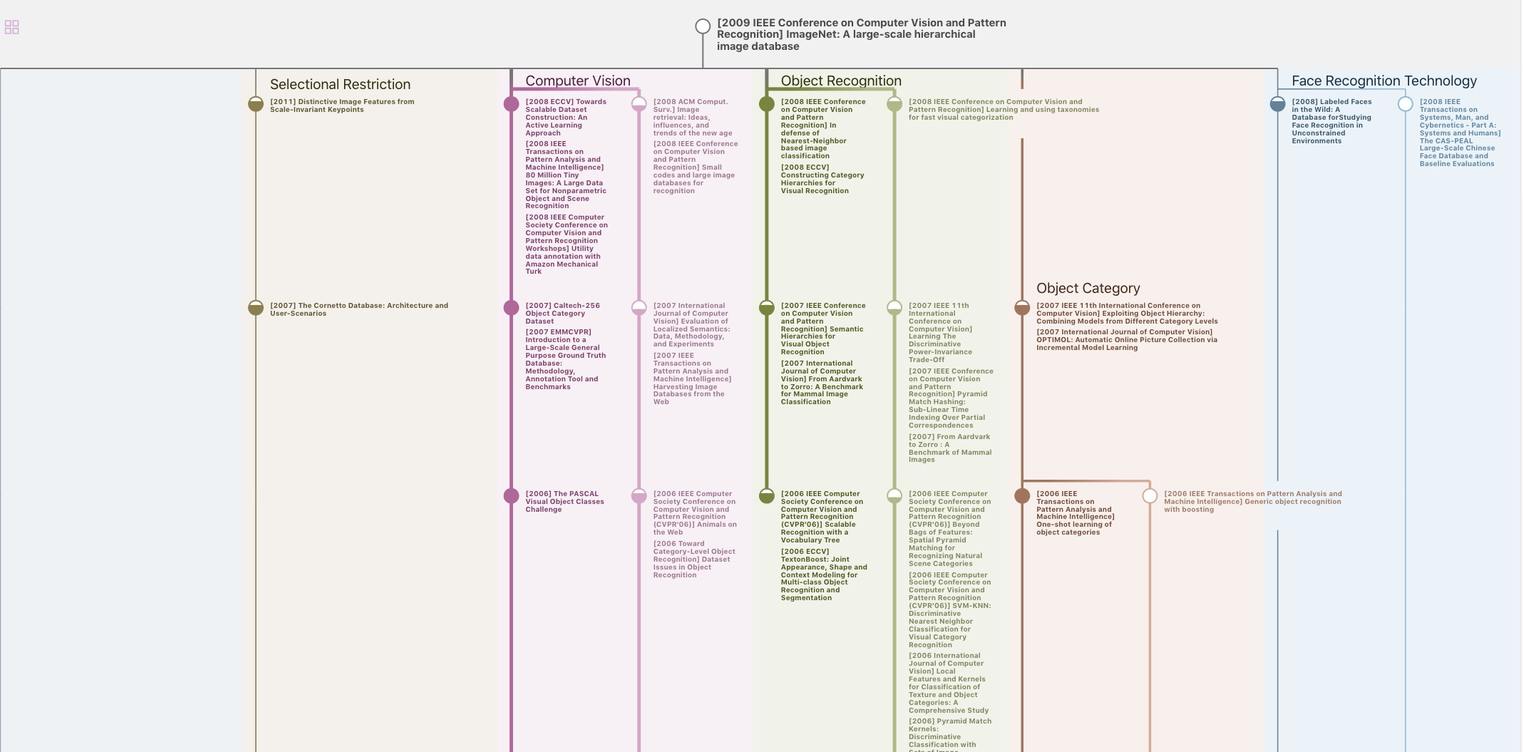
Generate MRT to find the research sequence of this paper
Chat Paper
Summary is being generated by the instructions you defined