Modeling of Combustor Non-Uniformities Evolution Through a High-Pressure Turbine Stage
JOURNAL OF TURBOMACHINERY-TRANSACTIONS OF THE ASME(2024)
Abstract
In modern gas turbines, the reduction of pollutant emissions can be achieved by employing lean-burn combustors. At the combustion chamber outlet, the flow is non-uniform and characterized by a residual swirl superimposed to steady (hot streak) and unsteady (entropy waves) temperature disturbances. During the transport from the combustor outlet to the turbine inlet, these disturbances are weakly dissipated and persist at the turbine inlet. Therefore, the interaction between the combustor non-uniformities and the turbine has to be deeply studied. To study combustor-turbine interaction experimentally, a common practice is to install combustor simulators on non-reactive turbine test facilities. For this purpose, a combustor simulator was designed and installed at the Politecnico di Milano turbine test facility. This device can generate a combined steady/unsteady temperature disturbance and swirl profile at the turbine inlet. Using this layout, several experimental campaigns have been carried out changing the type of injected disturbance, the injection position, and the turbine operating condition. In this paper, the data collected from these experiments have been used to develop simplified models to predict the transport and dissipation of combustor perturbations through a turbine's first stage. In the open literature, few attempts are discussed regarding the modeling of combustor-turbine interaction that-in authors' opinion-represents an important tool for preliminary turbine design.
MoreTranslated text
Key words
turbine aerodynamic,combustor-turbine interaction,hot-streak,entropy wave,swirl profile,low-order modeling
AI Read Science
Must-Reading Tree
Example
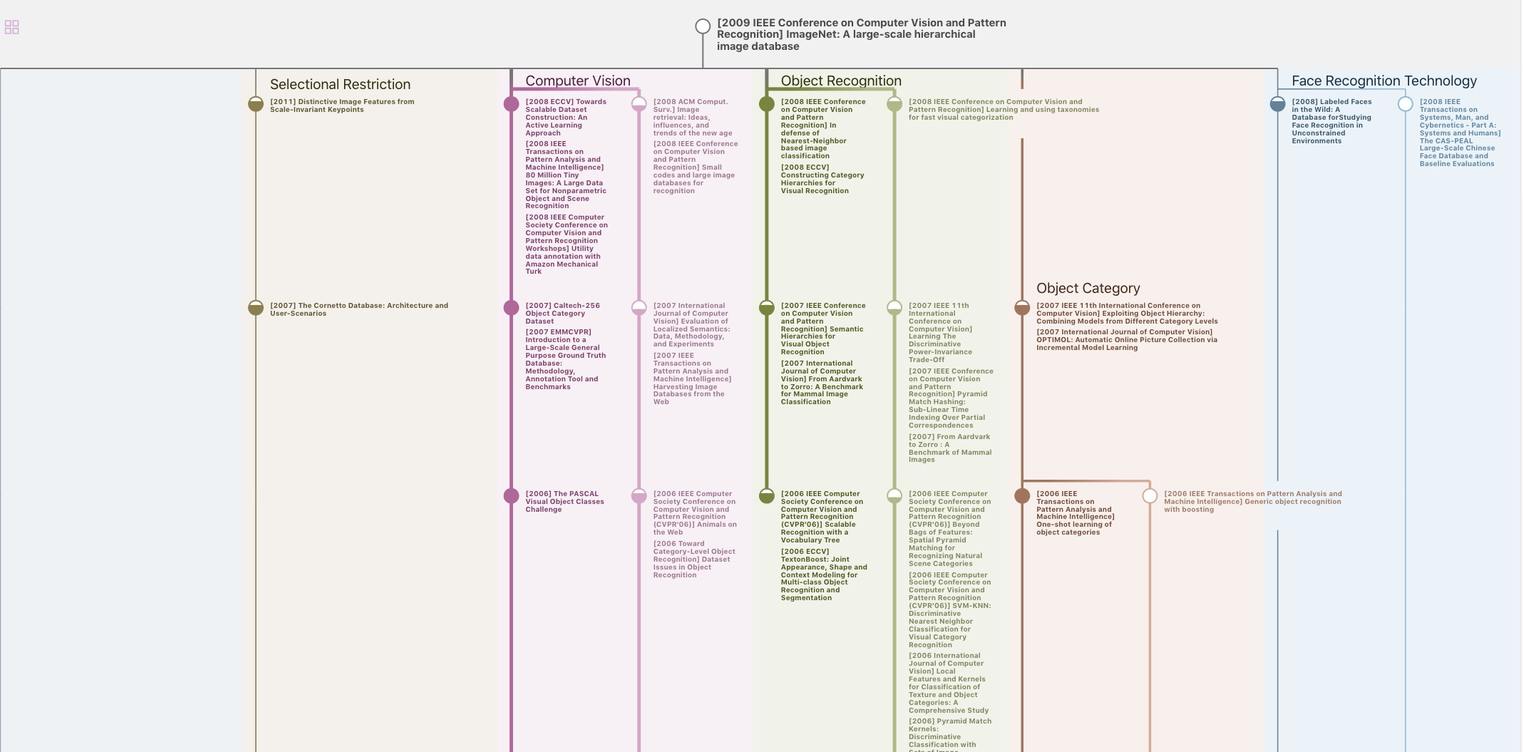
Generate MRT to find the research sequence of this paper
Chat Paper
Summary is being generated by the instructions you defined