Reducing Cf/SiC composite damages through collaborative control of laser ablating depth and grinding modes
Composite Structures(2024)
摘要
Cf/SiC composites are regarded as difficult-to-machine aerospace materials. A low-damage surface machining of Cf/SiC composite by laser-ablating assisted grinding (LAAG) was conducted, and investigated the effects of laser-ablating depth and grinding modes on surface/subsurface damages. The results showed that ablated material depth reached 420 μm after 1200 times scanning, while the effective ablating rate was inhibited by the depth. Compared with down grinding, the grinding forces and temperatures were substantially higher in up grinding, with a maximum increase of 123.5% and 140% in normal and tangential grinding forces, respectively; however, micro brittle fracture and ductile removal were remarkably enhanced in normal and transverse fibers, and surface macroscopic damage has been suppressed; subsurface damage remained insignificant, mainly exhibited in internal micro cracks and minor interfacial debonding. It was attributed to cutting characteristics of up grinding. Furthermore, as grinding depth increased, the material removal behavior underwent a brittle-ductile transition and the surface roughness grew accordingly. Moreover, a laser scanning angle of 0° and up grinding facilitated the occurrence of longitudinal fiber debonding, producing larger sized fiber bundle chips. Combining up grinding with 90° scanning angle at low grinding depth was an effective method to improve the surface quality of Cf/SiC composite.
更多查看译文
关键词
Cf/SiC composite,Grinding,Laser ablation,Subsurface damage
AI 理解论文
溯源树
样例
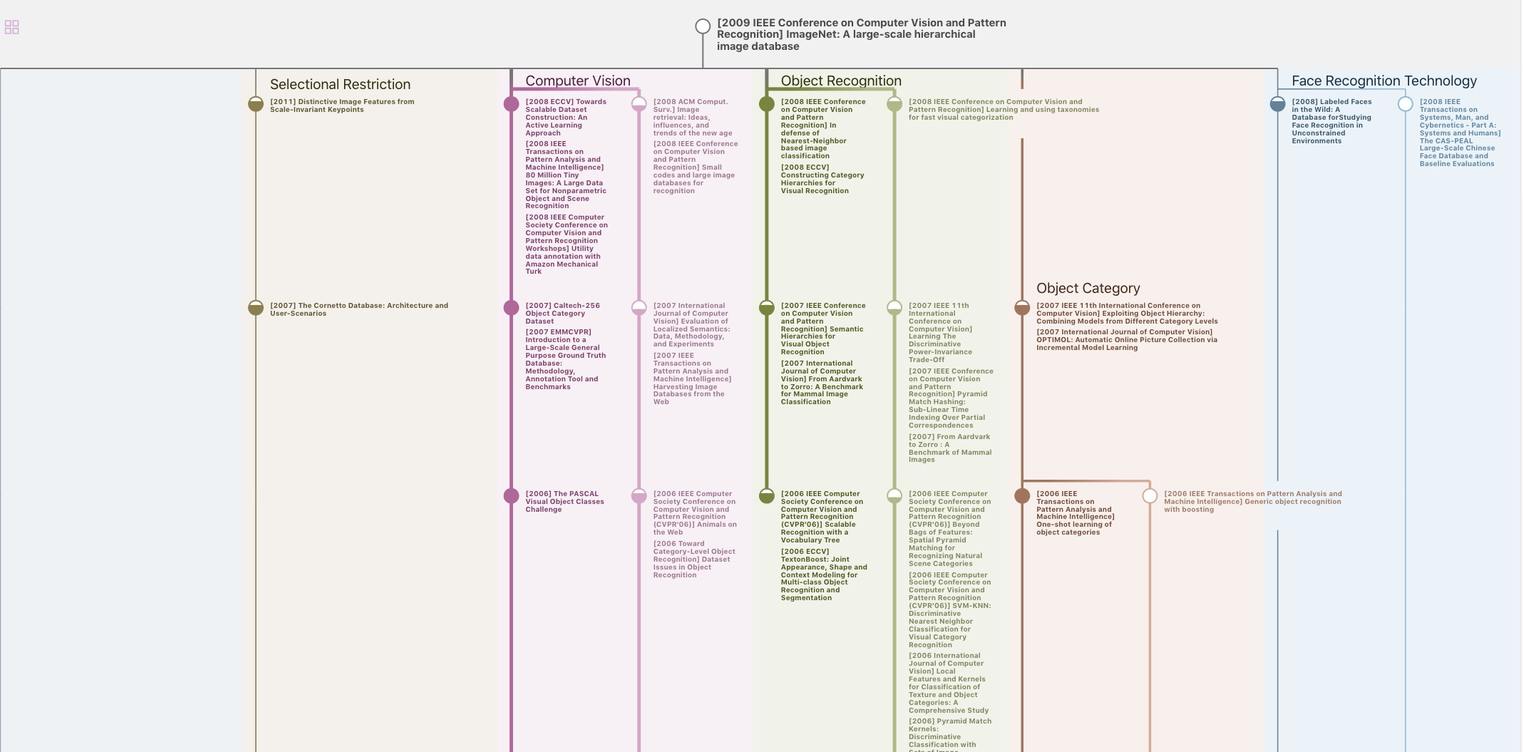
生成溯源树,研究论文发展脉络
Chat Paper
正在生成论文摘要