A Thermal Damage-Coupled Constitutive Model for Predicting Fracture and Microstructure Evolution and Its Application in the Hot Spinnability Process
Journal of Materials Research and Technology(2024)
Key words
Hot deformation,Microstructure evolution,Damage model,Stress state
AI Read Science
Must-Reading Tree
Example
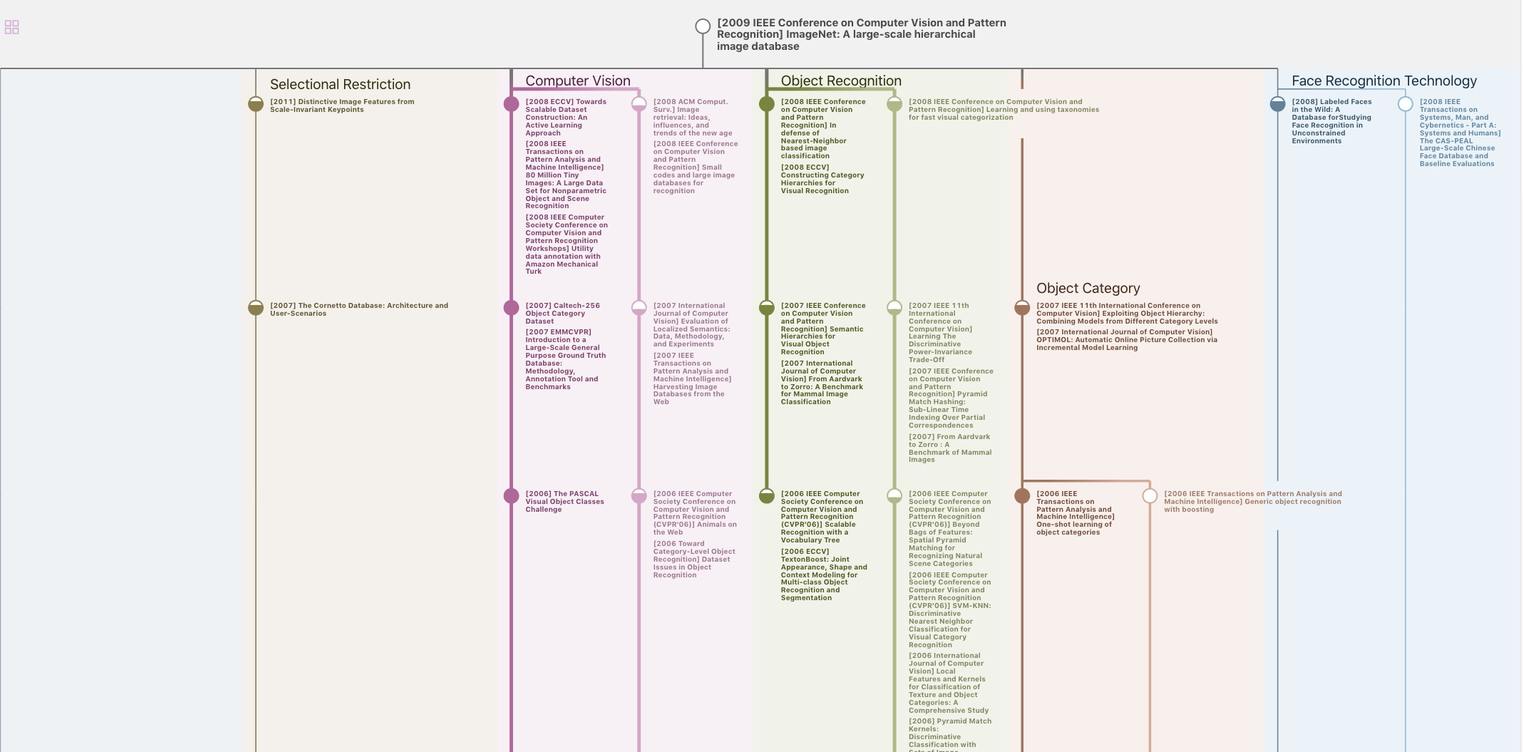
Generate MRT to find the research sequence of this paper
Chat Paper
Summary is being generated by the instructions you defined