Enhancing the Cooling Efficiency of Aluminum-Filled Epoxy Resin Rapid Tool by Changing Inner Surface Roughness of Cooling Channels
POLYMERS(2024)
摘要
In low-pressure wax injection molding, cooling time refers to the period during which the molten plastic inside the mold solidifies and cools down to a temperature where it can be safely ejected without deformation. However, cooling efficiency for the mass production of injection-molded wax patterns is crucial. This work aims to investigate the impact of varying surface roughness on the inner walls of the cooling channel on the cooling efficiency of an aluminum-filled epoxy resin rapid tool. It was found that the cooling time for the injection-molded products can be determined by the surface roughness according to the proposed prediction equation. Employing fiber laser processing on high-speed steel rods allows for the creation of microstructures with different surface roughness levels. Results demonstrate a clear link between the surface roughness of cooling channel walls and cooling time for molded wax patterns. Employing an aluminum-filled epoxy resin rapid tool with a surface roughness of 4.9 mu m for low-pressure wax injection molding can save time, with a cooling efficiency improvement of approximately 34%. Utilizing an aluminum-filled epoxy resin rapid tool with a surface roughness of 4.9 mu m on the inner walls of the cooling channel can save the cooling time by up to approximately 60%. These findings underscore the significant role of cooling channel surface roughness in optimizing injection molding processes for enhanced efficiency.
更多查看译文
关键词
surface roughness,cooling efficiency,aluminum-filled epoxy resin,rapid tool,cooling time,low-pressure wax injection molding
AI 理解论文
溯源树
样例
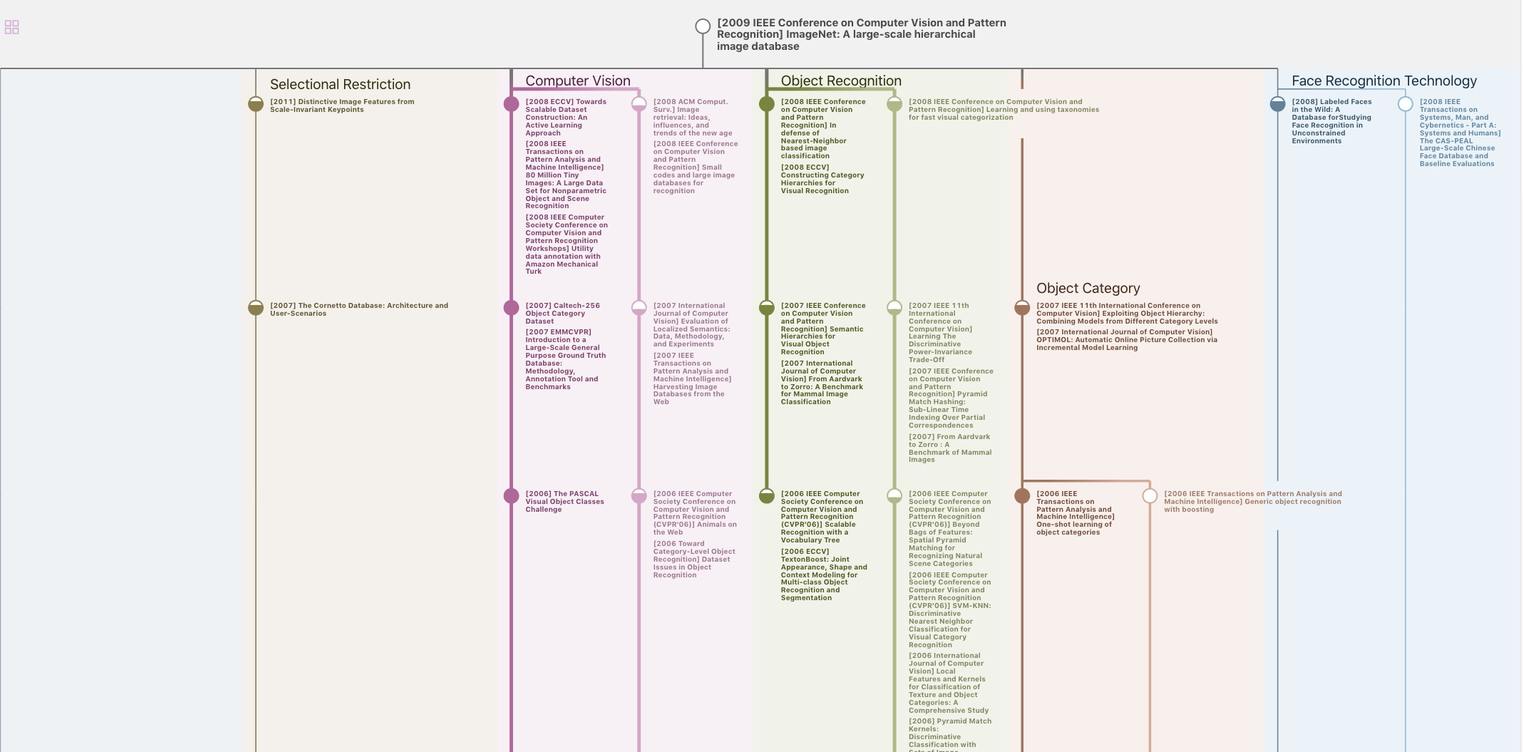
生成溯源树,研究论文发展脉络
Chat Paper
正在生成论文摘要