Effect of Shot Peening and CuNiIn Coating Composite Treatment on Fretting Fatigue Properties of Superalloy Tenon Specimens
CHINA SURFACE ENGINEERING(2023)
摘要
The 10705BX iron-based superalloy has the advantages of high yield strength, corrosion resistance, and oxidation resistance. It is widely used for manufacturing high-temperature components, such as turbine discs, blades, and fasteners. However, under actual working conditions, the tenon structure of a turbine is subjected to alternating cyclic loads, resulting in fretting fatigue cracks until failure, which eventually leads to accidents. Surface modification technology forms a work-hardening layer and introduces residual stress; thus, the fretting fatigue properties of materials can be improved using this method. To date, the fretting fatigue properties of 10705BX iron-based superalloys and related surface-strengthening techniques have not been reported. Fretting fatigue tests were performed on 10705BX iron-based superalloy tenon structures treated using different surface modification techniques under different loads to extend the service life of the turbine. The fretting fatigue tests were conducted using a high-frequency fatigue-testing machine. The specific test parameters were as follows: a peak load of 22 kN, stress ratio of 0.1, and frequency values of 128-138 Hz. The fretting fatigue properties of the 10705BX iron-based superalloy dovetail structure were compared after as-received (AS), shot peening (SP), and shot peening + coating composite treatments (SC), respectively. Subsequently, the surface and cross-sectional morphologies, fracture characteristics, and mechanical properties were analyzed. The results showed that the surface roughness Sa values of the AS, SP, and SC samples were 0.08, 3.38, and 13.65 gm, respectively. The surface hardness increased by 16.28% after SP. The hardened layer depth was approximately 80 gm. Based on the KAM chart of EBSD analysis, the stress in the 0-80 gm region from the surface depth of the sample after SP treatment was relatively high owing to the high residual compressive stress introduced by shot peening. The fretting fatigue lifetime after SP was 7.8 times longer than that of AS. The fretting fatigue lifetime after SC was 4.2 times longer than that after AS. The average coating thickness was approximately 50 gm. Compared to the SP treatment, the fretting fatigue life of the SC treatment was low. This was because, after the SC treatment, the hardness of the hardened layer below the coating decreased slightly, reducing the anti-fretting fatigue performance. During plasma-spraying CuNiIn coating, the thermal effect of thermal spraying can somewhat reduce the residual stress introduced by shot peening, reducing the anti-fretting fatigue property of the sample. However, because the CuNiIn coating was soft, it exhibited good fretting wear resistance. When subjected to cyclic loading, ductile deformation occurs easily, and it has a lubricating effect, reducing stress concentration, and improving fatigue life. The cracks in the AS, SP, and SC samples were initiated by multiple fatigue sources. However, the number of crack sources after SP and SC decreased significantly. The fretting fatigue fracture mechanism of 10705BX did not change after SP and SC treatments but expanded in the cleavage mode. However, the crack propagation rate increased. The fatigue band spacings in the rapid expansion zone of the AS, SP, and SC treatments were 0.39, 0.83, and 0.84 gm, respectively. An increase in the fatigue-band spacing indicates an increase in the crack growth rate. The crack initiation lifetime increased because of the formation of a hardened layer and the compressive residual stress after SP. SP and SC treatments are expected to be important alternative methods for extending the service life of turbine blades.
更多查看译文
关键词
10705BX superalloy,shot peening,CuNiIn coating,composite processing,fretting fatigue
AI 理解论文
溯源树
样例
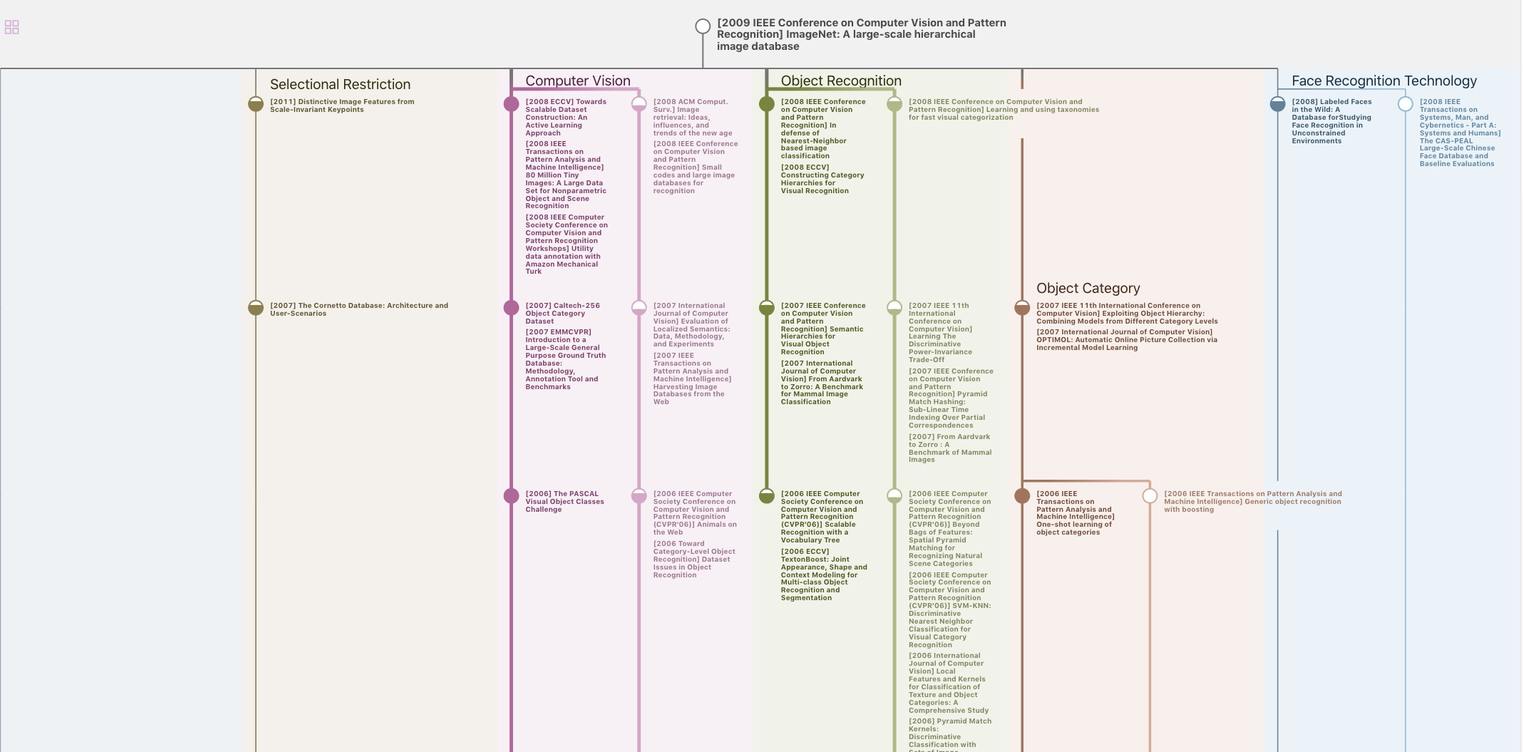
生成溯源树,研究论文发展脉络
Chat Paper
正在生成论文摘要