Measurement of Creep Deformation of Resin Structural Parts for a Lightweight Industrial Robot.
2024 IEEE/SICE International Symposium on System Integration (SII)(2024)
摘要
Lightweight industrial robots are increasingly required to reduce power consumption. In this research, we focus on lightweight resin materials such as 3D printed parts, and our ultimate goal is to develop practical industrial robots using these materials as structural parts. Unlike conventional light metal materials such as high-strength aluminum, resin materials have creep deformation properties even at room temperature, which deteriorates the end-point position accuracy in practical use over a long period. In this paper, we fabricated an experiment apparatus that can measure creep deformation by applying 40 kgf of load at the end of a beam specimen. A laser displacement meter accurately measured the creep deformation for approximately two months (1600 hours). For comparison, we measured the creep deformation of six specimens of five different lightweight resin materials and conventional aluminum alloys (A5052). The results showed that 3D printed materials had large creep deformation, whereas A5052 and FELCARBO showed almost no creep deformation.
更多查看译文
关键词
Part Of Structure,Creep Deformation,Industrial Technology Development Organization,Experimental Setup,3D Printing,Conventional Materials,Aluminium Alloy,Resin Matrix,3D Printing Materials,End Of The Specimen,Laser Displacement,3D-printed Parts,Time Series,Weight Reduction,Time Series Data,Loading Conditions,Bulk Material,Carbon Fiber,Measurement Procedure,Chamber Temperature,Displacement Measurements,Fused Deposition Modeling,Continuous Fibers,Outside Temperature,Part Of The Robot,Heating, Ventilation, And Air Conditioning,Vibration Analysis,Standard Specimens,Transducer Surface,Main Experiment
AI 理解论文
溯源树
样例
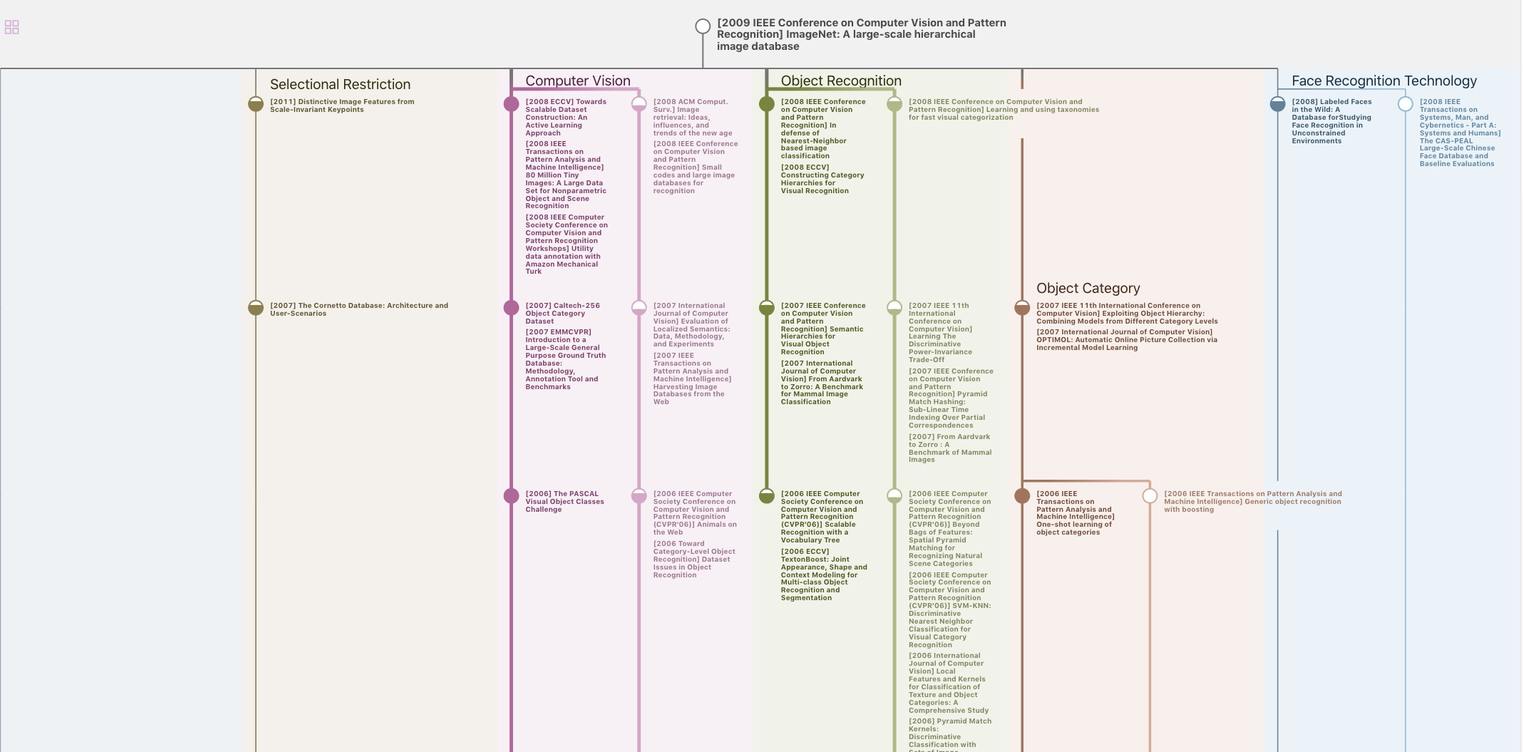
生成溯源树,研究论文发展脉络
Chat Paper
正在生成论文摘要