Nanostructuring of Additively Manufactured 316L Stainless Steel Using High-Pressure Torsion Technique: An X-ray Line Profile Analysis Study
MATERIALS(2024)
Abstract
Experiments were conducted to reveal the nanostructure evolution in additively manufactured (AMed) 316L stainless steel due to severe plastic deformation (SPD). SPD-processing was carried out using the high-pressure torsion (HPT) technique. HPT was performed on four different states of 316L: the as-built material and specimens heat-treated at 400, 800 and 1100 degrees C after AM-processing. The motivation for the extension of this research to the annealed states is that heat treatment is a usual step after 3D printing in order to reduce the internal stresses formed during AM-processing. The nanostructure was studied by X-ray line profile analysis (XLPA), which was completed by crystallographic texture measurements. It was found that the as-built 316L sample contained a considerable density of dislocations (10(15) m(-2)), which decreased to about half the original density due to the heat treatments at 800 and 1100 degrees C. The hardness varied accordingly during annealing. Despite this difference caused by annealing, HPT processing led to a similar evolution of the microstructure by increasing the strain for the samples with and without annealing. The saturation values of the crystallite size, dislocation density and twin fault probability were about 20 nm, 3 x 10(16) m(-2) and 3%, respectively, while the maximum achievable hardness was similar to 6000 MPa. The initial <100> and <110> textures for the as-built and the annealed samples were changed to <111> due to HPT processing.
MoreTranslated text
Key words
316L steel,additive manufacturing,high-pressure torsion,X-ray line profile analysis,dislocation density,crystallite size,twin fault probability
AI Read Science
Must-Reading Tree
Example
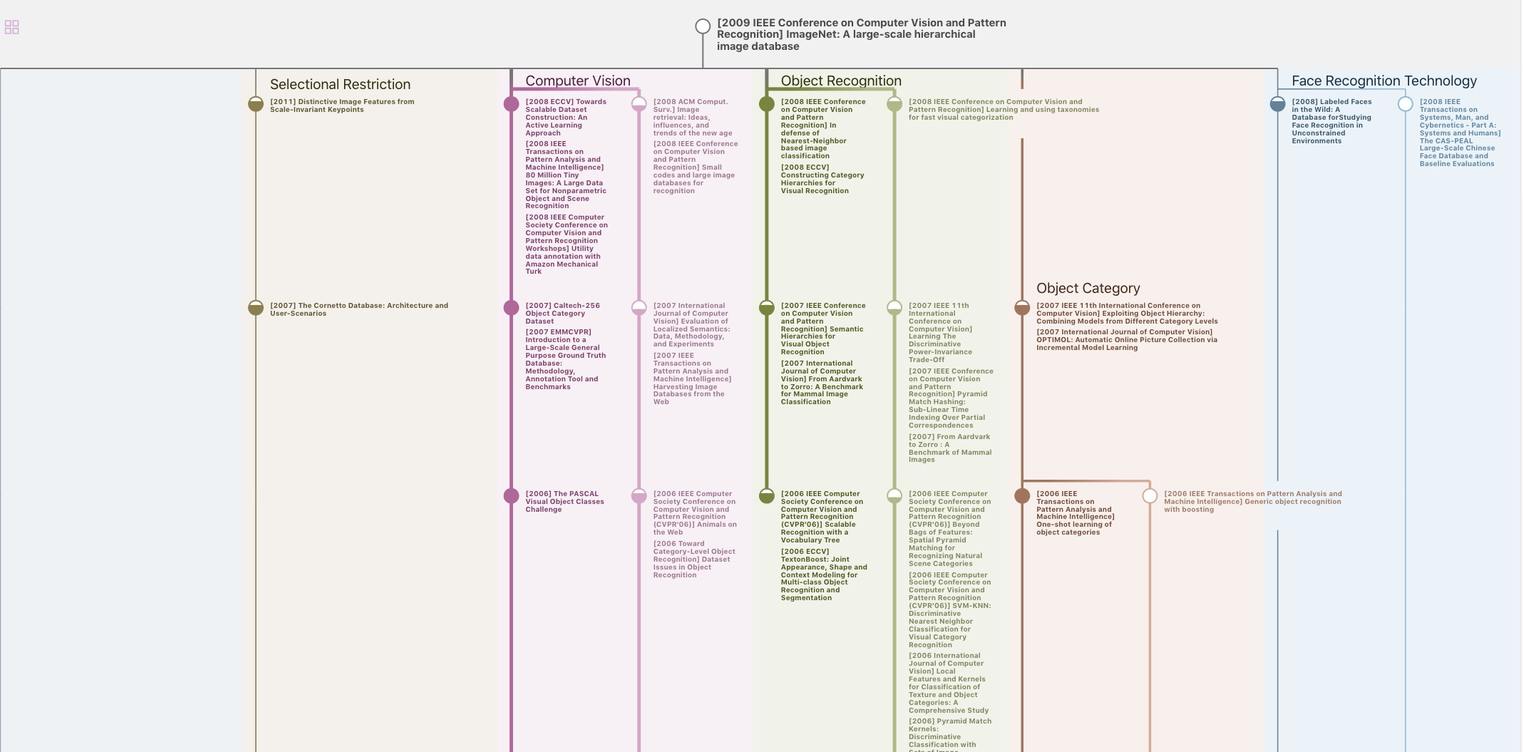
Generate MRT to find the research sequence of this paper
Chat Paper
Summary is being generated by the instructions you defined