Accurate TCP Position and Orientation Trajectory Generation in 6DOF Robotic Manipulators and CNC Machine Tools using FIR Filtering and Haversine Synchronisation
Procedia CIRP(2023)
摘要
The use of robotics in manufacturing is rapidly growing. One promising application in particular is the use of robots as machining platforms. Robotic machining offers many advantages such as large operating envelopes, flexibility in operations and low installation and running costs. Robotic machining platforms much like computer numerically controlled (CNC) machine tools are commanded by numerical controllers (NCs) using the well established G-code part programming language (ISO-6983). Toolpaths are defined in the work piece coordinate system (WCS) as a series of discrete tool centre point (TCP) positions and tool orientations. The role of the NC is to generate smooth feed drive or robot joint commands such that the tool or end effector travels along the commanded toolpath whilst satisfying TCP position and orientation tolerances and robot/machine tool kinematic constraints. Interpolating tool orientations directly in the WCS requires complex real-time spherical interpolation computations. Overcoming this challenge, this paper introduces a C4 continuous tool path trajectory generation method for 6DOF motion. The tool centre point position is smoothed in the WCS, however, the tool orientation is smoothed directly in the rotary coordinate system without the requirement for spherical interpolation. The interpolated tool orientation trajectory follows the path of the great circle arc using the modified Haversine method eliminating non-linear interpolation errors present in linear interpolation of rotary axis positions (machine coordinate system interpolation). The proposed method is validated by simulation of a 6DOF robotic manipulator.
更多查看译文
关键词
Robotic Machining interpolation,Trajectory Generation,Pose Control,Motion Control
AI 理解论文
溯源树
样例
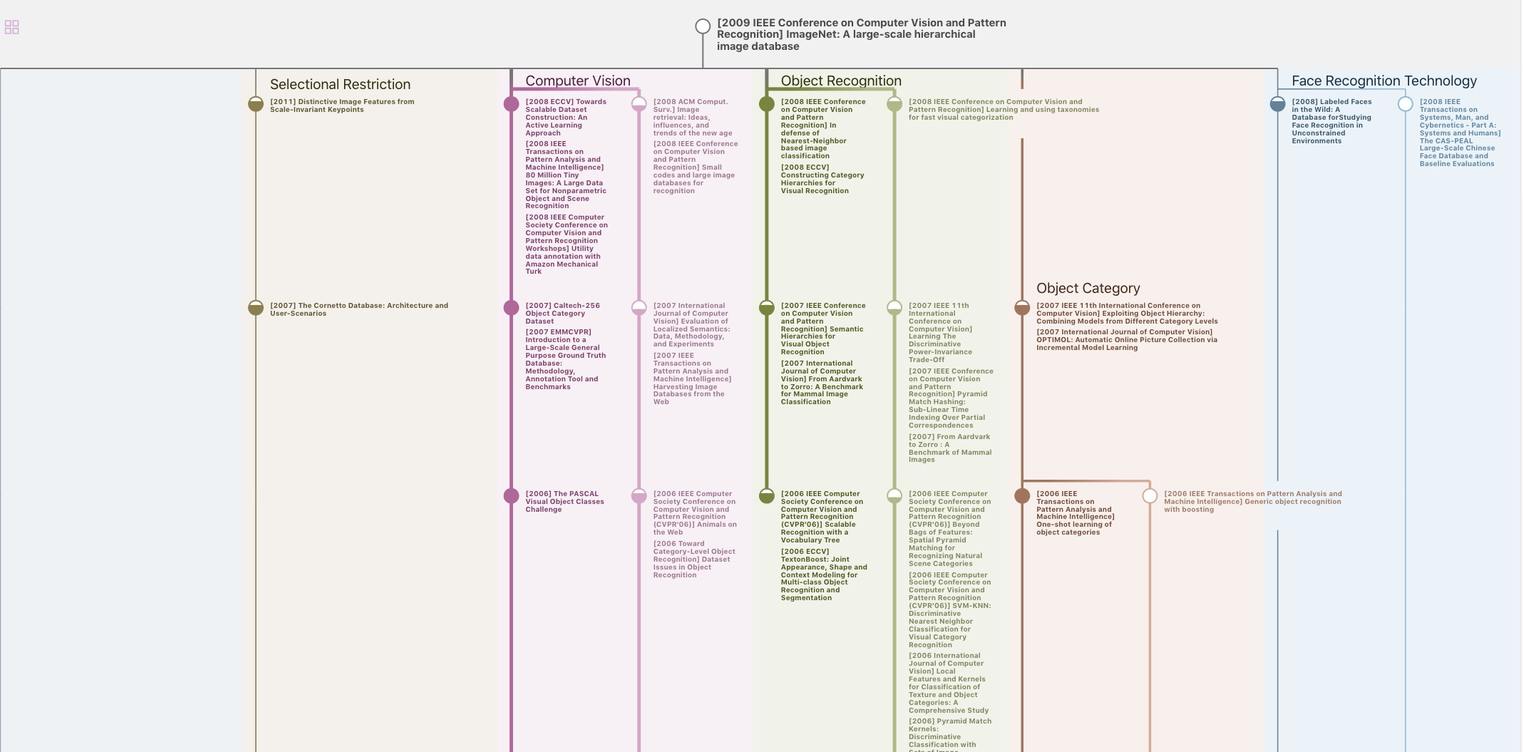
生成溯源树,研究论文发展脉络
Chat Paper
正在生成论文摘要