Mechanical model of strut-based metamaterials based on direct stiffness method
INTERNATIONAL JOURNAL OF MECHANICAL SCIENCES(2024)
摘要
The mechanical properties of micro-struts manufactured through laser powder bed fusion (LPBF) are influenced by a multitude of factors including forming angle, thickness, process parameters, and equipment. This results in the failure of mechanical models for strut-based metamaterials that are based on bulk material properties. By incorporating mechanical property data from micro-struts produced using LPBF into a direct stiffness method, we developed a mechanical model capable of predicting the elastic tensor and strength surface of strut-based metamaterials. The robustness of this methodology was evaluated through quasi-static compression experi-ments on 3D double-arrowhead (DAH) auxetic metamaterials produced using LPBF and finite element analysis (FEA). Results indicate that the deviations of Young's modulus, Poisson's ratio, and strength between the theoretical model's predictions and experimental results are within 30 %, 50 %, and 25 %, decreasing to within 15 %, 30 %, and 15 % as relative density increases, respectively. Deviations from FEA results under the assumption of uniform strut performance remain within 15 %, 25 %, and 20 %, correspondingly. Furthermore, the theoretical model can predict the elasticity and strength of metamaterials under any loading direction and identify the most vulnerable strut in the metamaterial unit. The theoretical model effectively represented the general anisotropy of metamaterials resulting from LPBF manufacturing factors. This study presents a transplantable method for developing mechanical models of strut-based metamaterials, improving the accuracy of performance prediction and promoting their application in LPBF-manufactured parts.
更多查看译文
关键词
Strut-based metamaterials,Direct stiffness method,Laser powder bed fusion,Anisotropic,Strength surface
AI 理解论文
溯源树
样例
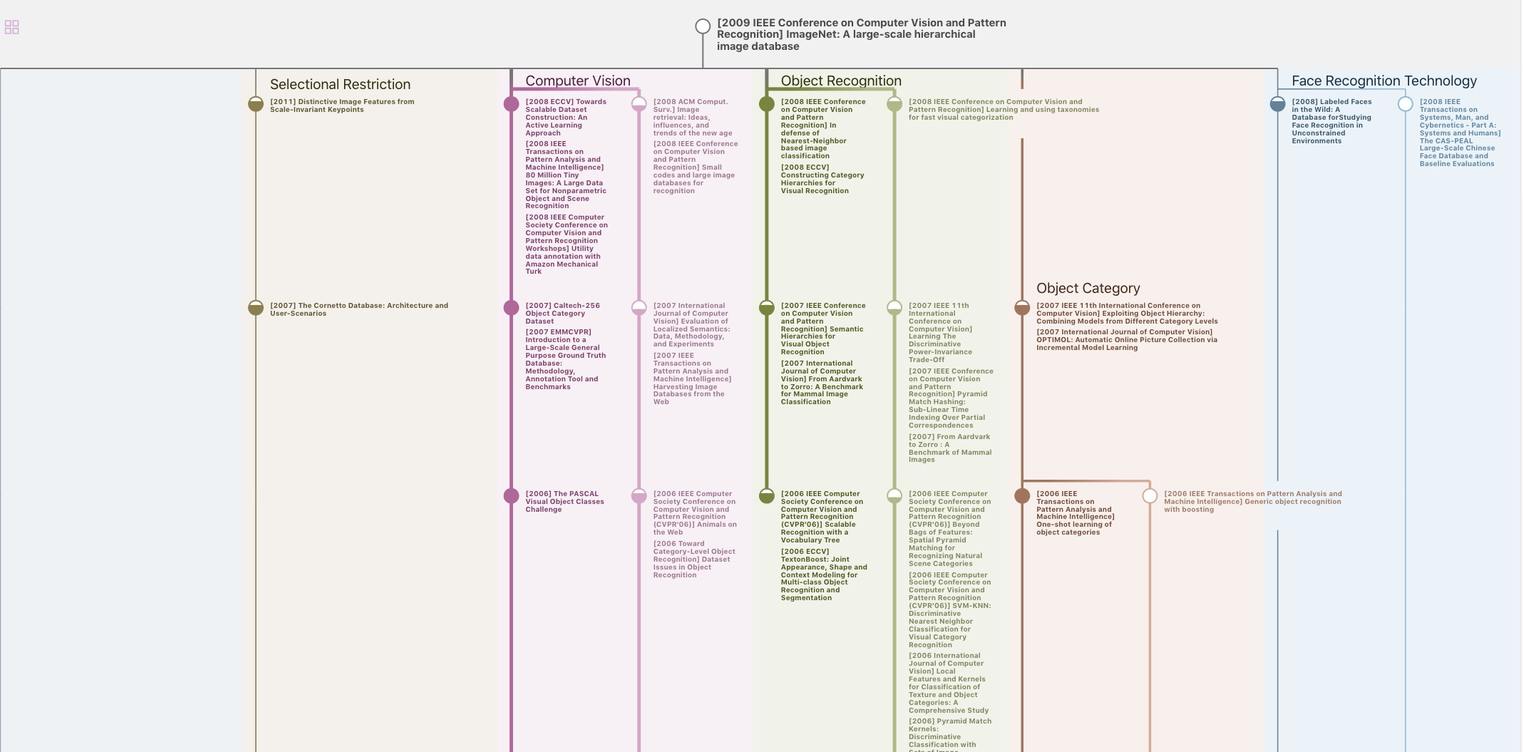
生成溯源树,研究论文发展脉络
Chat Paper
正在生成论文摘要