Modification and Optimization of the Trajectory of an Industrial Robot to Scan a 3D-Surface for Quality Inspection
ADVANCES IN SERVICE AND INDUSTRIAL ROBOTICS, RAAD 2023(2023)
关键词
Industrial robots,Automatic quality inspection,Machine vision
AI 理解论文
溯源树
样例
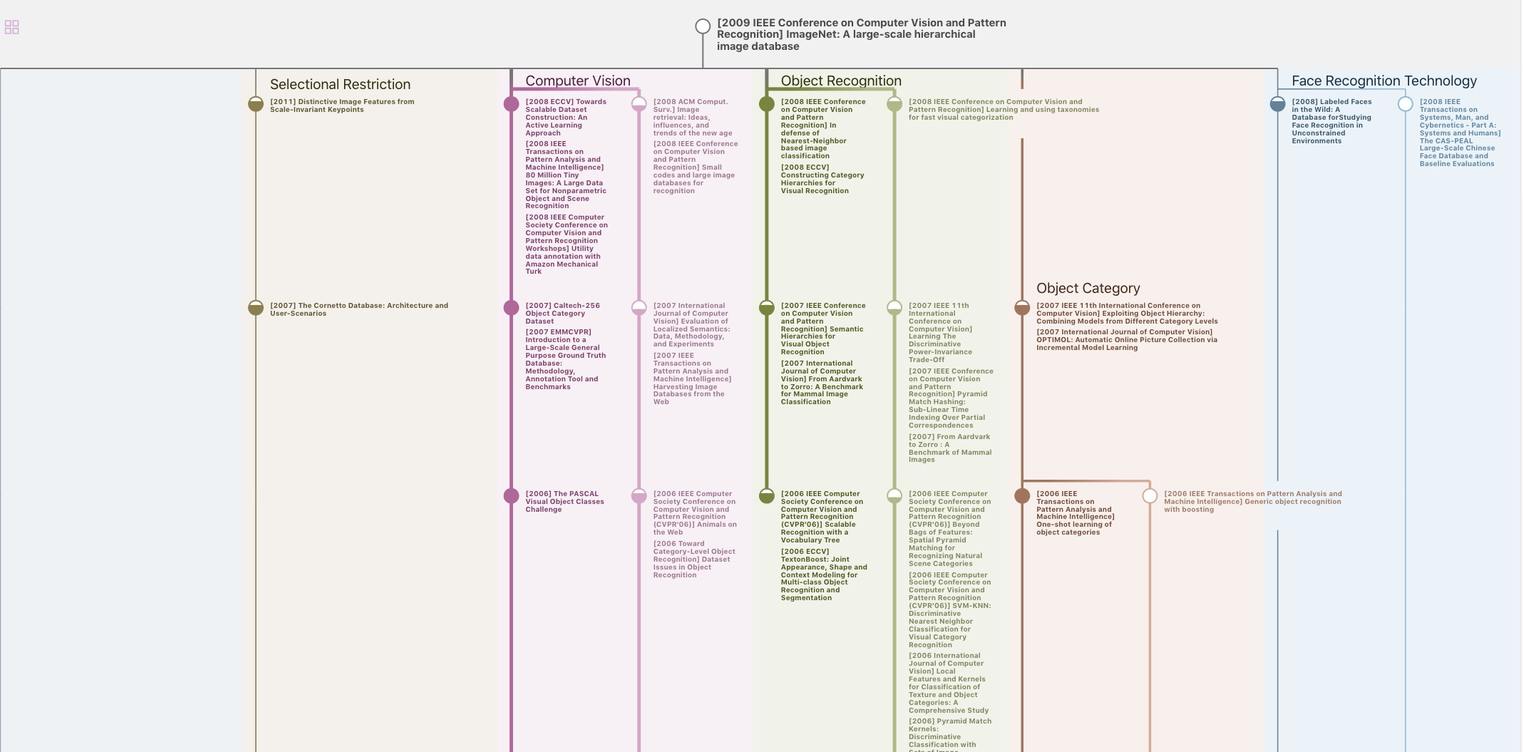
生成溯源树,研究论文发展脉络
Chat Paper
正在生成论文摘要