Optimizing calcination of coal by-products for maximizing REE leaching recovery and minimizing Al, Ca, and Fe contamination
Journal of Rare Earths(2023)
Abstract
High-temperature calcination is effective in improving the leaching characteristics of rare earth elements (REEs) from conventional REE-bearing minerals by transforming them into more leachable forms. However, the recovery of contaminants such as Al, Fe, and Ca also increases significantly. The objective of the study was to maximize the REE extraction while minimizing the concentration of contaminant ions (Al, Ca, and Fe) in the leach solution. Representative density fractions of the coarse refuse from the Baker and Fire Clay seam coal refuse were pulverized to a top size of 180 μm and used as a feedstock for the study. All the samples generated from thermal treatment were leached at 1% (w/v) using 1.2 mol/L sulfuric acid at 75 °C for 2 h. Test results from a parametric program based on a Box-Behnken design were used for modeling and optimization of three operating parameters associated with the lab-scale calcination process. The parameters include temperature (400–800 °C), ramp rate (2–10 °C/min) and holding time (0–120 min). It is determined that the calcination temperature is the most significant parameter influencing REE recovery. The majority of the heavy rare earth elements (HREEs) is found to be present in an insoluble form in the calcination products and is marginally affected by thermal treatment. A strong correlation between light rare earth elements recovery (LREEs) and Al suggests a possible association with clays. The optimum operating conditions for high REE recovery with comparatively lower contaminant concentration for 1.6 specific gravity float and 2.2 sink fractions of Baker and Fire Clay seam material were determined to be at 776, 800 °C and 407, 800 °C, calcining temperatures, respectively. A higher optimum temperature of 1.6 float fraction of Baker seam relative to Fire Clay seam material is due to elevated pyrite concentration in Baker seam material. Thermal treatment at 400 °C converts pyrite into a soluble intermedium iron oxide, resulting in a high Fe content in the leachate. Calcining at 776 °C converts most of the soluble iron oxide into insoluble α-hematite, considerably reducing the Fe concentration in the solution.
MoreTranslated text
Key words
Calcination,Optimization,Rare earth elements,Coal refuse
AI Read Science
Must-Reading Tree
Example
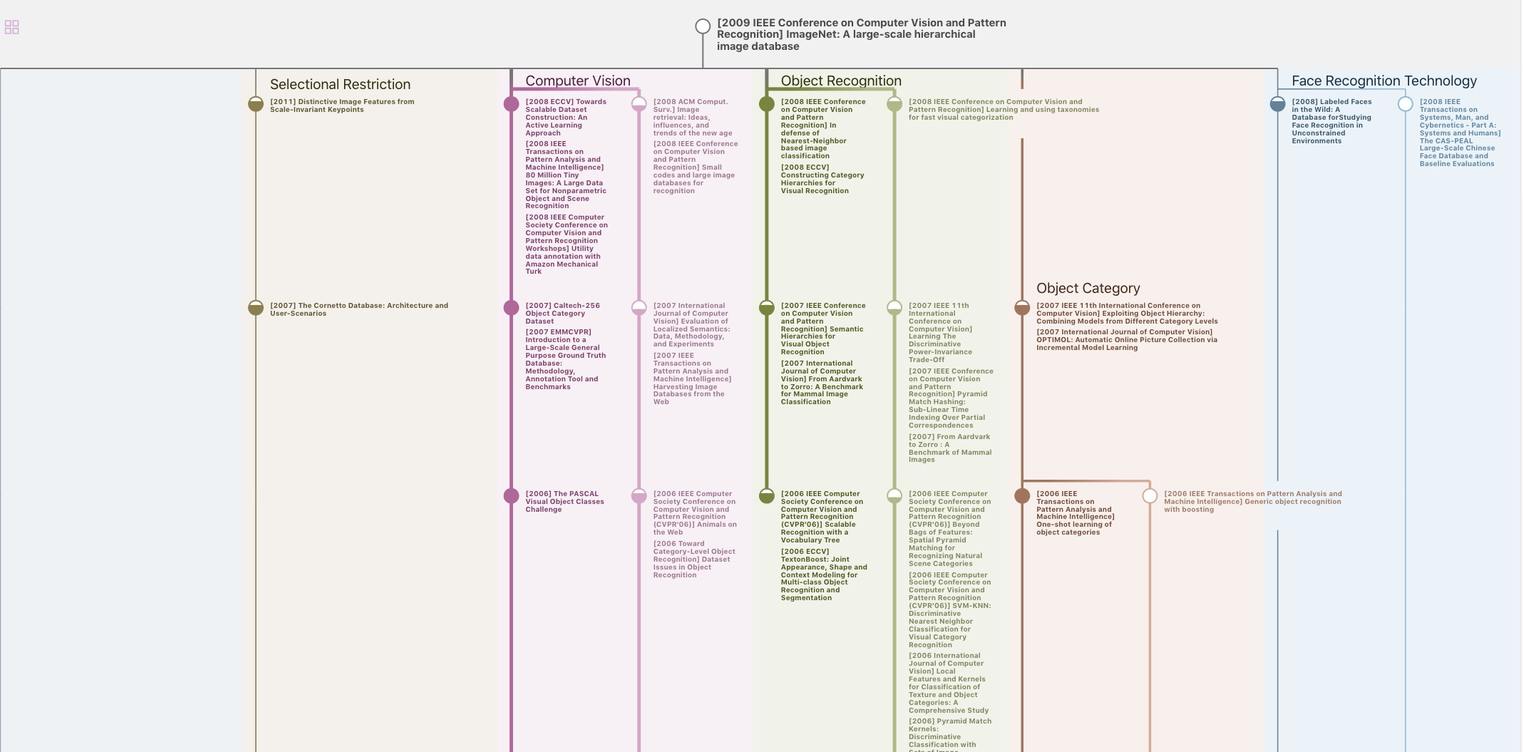
Generate MRT to find the research sequence of this paper
Chat Paper
Summary is being generated by the instructions you defined