A case study of hybrid manufacturing of a Ti-6Al-4V titanium alloy hip prosthesis
The International Journal of Advanced Manufacturing Technology(2023)
摘要
Abstract Hybrid manufacturing (HM) is a process that combines additive manufacturing (AM) and subtractive manufacturing (SM). It is becoming increasingly recognized as a solution capable of producing components of high geometric complexity, while at the same time ensuring the quality of the surface finish, rigour and geometric tolerance on functional surfaces. This work aims to study the surface finish quality of an orthopaedic hip resurfacing prosthesis obtained by HM. For this purpose, test samples of titanium alloy Ti-6Al-4V using two Power Bed Fusion (PBF) processes were manufactured, which were finished by turning and 5-axis milling. It was verified that, upon the machining tests, no differences in Ra and Rt were found between the various types of AM. Regarding the type of SM used, 5-axis milling provided lower roughness results with a consistent value of Ra = 0.6 µm. The use of segmented circle mills in 5-axis milling proved to be an asset in achieving a good surface finish. This work successfully validated the concept of HM to produce a medical device, namely, an orthopaedic hip prosthesis. As far as surface quality is concerned, it could be concluded that the optimal solution for this case study is 5-axis milling.
更多查看译文
关键词
Ti-6Al-4V,Titanium alloy,Hybrid manufacturing,EBM,SLS
AI 理解论文
溯源树
样例
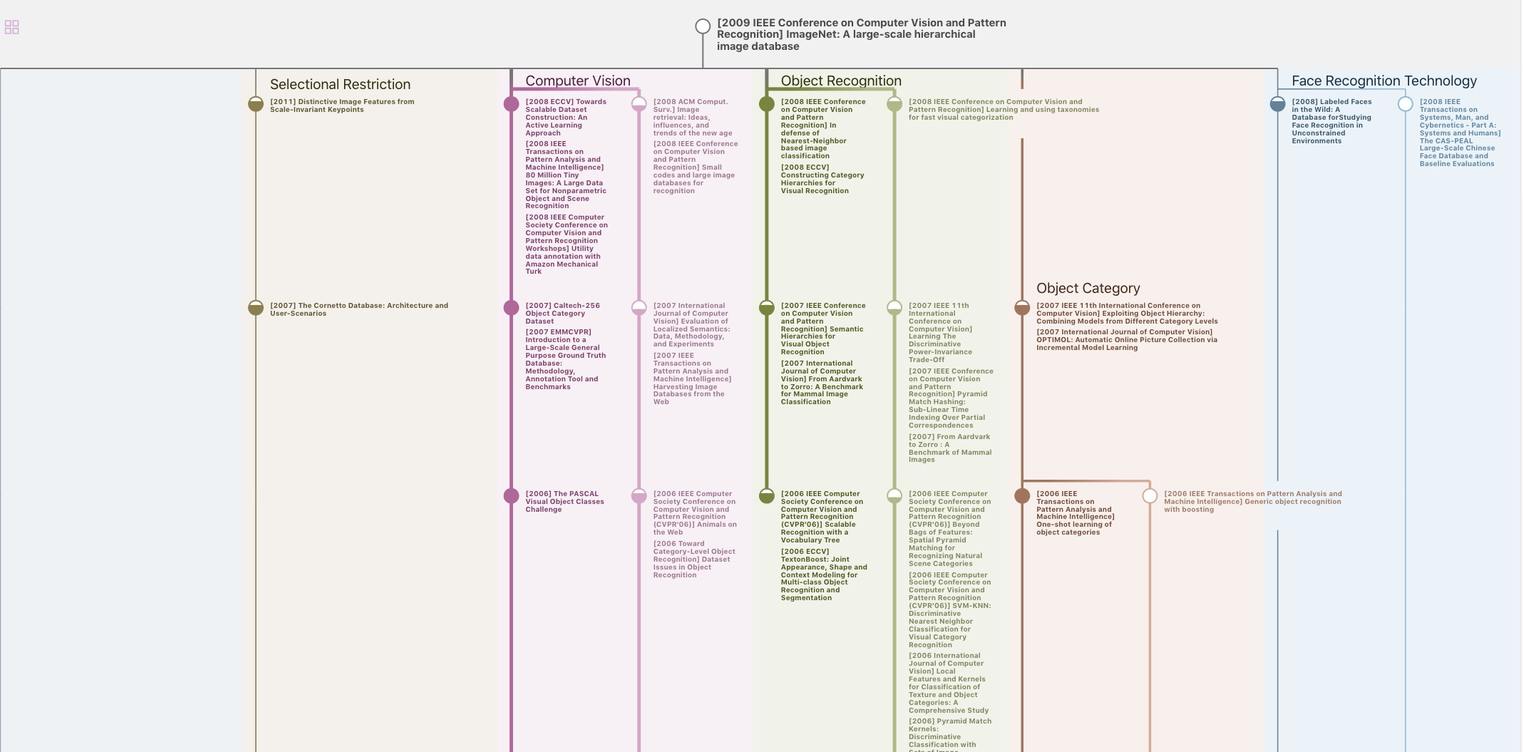
生成溯源树,研究论文发展脉络
Chat Paper
正在生成论文摘要