Base placement optimization of a mobile hybrid machining robot by stiffness analysis considering reachability and nonsingularity constraints
CHINESE JOURNAL OF AERONAUTICS(2023)
摘要
The mobile hybrid machining robot has a very bright application prospect in the field of high-efficiency and high-precision machining of large aerospace structures. However, an inappropriate base placement may make the robot encounter a singular configuration, or even fail to complete the entire machining task due to unreachability. In addition to considering the two constraints of reachability and non-singularity, this paper also optimizes the robot base placement with stiffness as the goal to improve the machining quality. First of all, starting from the structure of the robot, the reachability and nonsingularity constraints are transformed into a simple geometric constraint imposed on the base placement: feasible base placement area. Then, genetic algorithm is used to search for the base placement with near optimal stiffness (near optimal base placement for short) in the feasible base placement area. Finally, multiple controlled experiments were carried out by taking the milling of a protuberance on the spacecraft cabin as an example. It is found that the calculated optimal base placement meets all the constraints and that the machining quality was indeed improved. In addition, compared with simple genetic algorithm, it is proved that the feasible base placement area method can shorten the running time of the whole program. (c) 2022 Production and hosting by Elsevier Ltd. on behalf of Chinese Society of Aeronautics and Astronautics. This is an open access article under the CC BY-NC-ND license (http://creativecommons.org/ licenses/by-nc-nd/4.0/).
更多查看译文
关键词
Aerospace industry,Base placement optimiza-tion,Hybrid machining robot,Mobile robot,Robot application,Singularity avoidance,Stiffness optimization
AI 理解论文
溯源树
样例
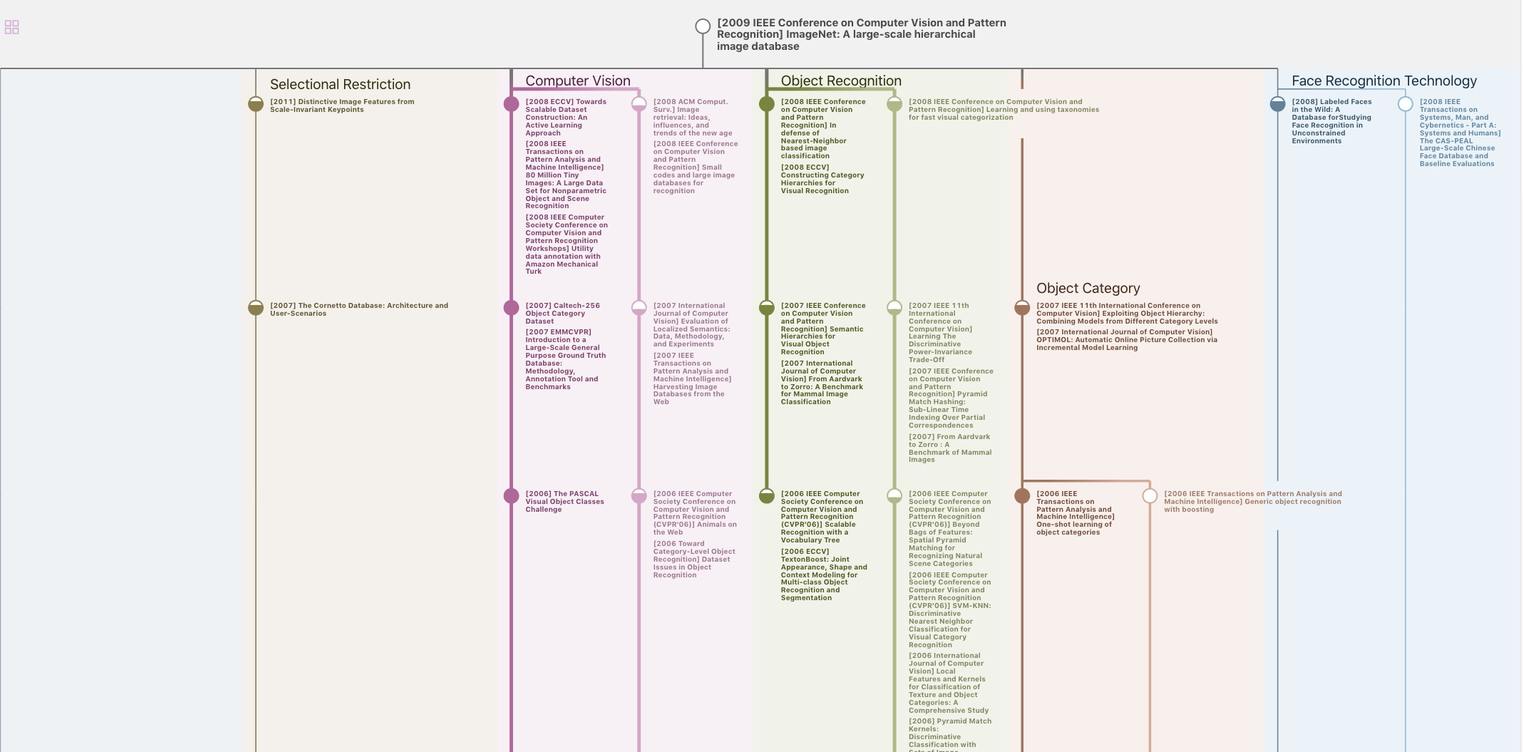
生成溯源树,研究论文发展脉络
Chat Paper
正在生成论文摘要