Reduction of Cogging Torque in Segmented Permanent Magnet BLDC Motor IPM V-Shape by Skewing Stator
THE INTERNATIONAL CONFERENCE ON BATTERY FOR RENEWABLE ENERGY AND ELECTRIC VEHICLES (ICB-REV) 2022 AIP Conference Proceedings(2023)
Abstract
. The cogging torque on a brushless DC (BLDC) motor, in this case on the Internal Permanent Magnet V-Shape motor, causes torque ripple and speed fluctuations. This can interfere with motor operating performance because the motor will not rotate smoothly due to noise and vibration, especially at low rpm. Therefore, the cogging torque must be reduced or eliminated so that the operating performance of the BLDC motor IPM V-Shape that has been designed and built can be better. Several studies have shown various ways to reduce or eliminate cogging torque. This paper will analyze and apply one of the methods to eliminate cogging torque, which is the Skew Method in the stator of the BLDC motor IPM V-Shape through Finite Element Analysis (FEA) simulation using ANSYS Maxwell. The motor's torque, speed, and efficiency will be analyzed to determine the effectiveness of the Skew Method on the stator of BLDC Motor IPM V-Shape. The result shows that the Skew Method in the BLDC Motor IPM V-Shape can reduce by almost 100% of cogging torque and produce a motor design that has good performance
MoreTranslated text
Key words
Cogging Torque Reduction,Motor Design Optimization,Permanent Magnet Machines,Bearingless Motors,Magnetic Gearing
AI Read Science
Must-Reading Tree
Example
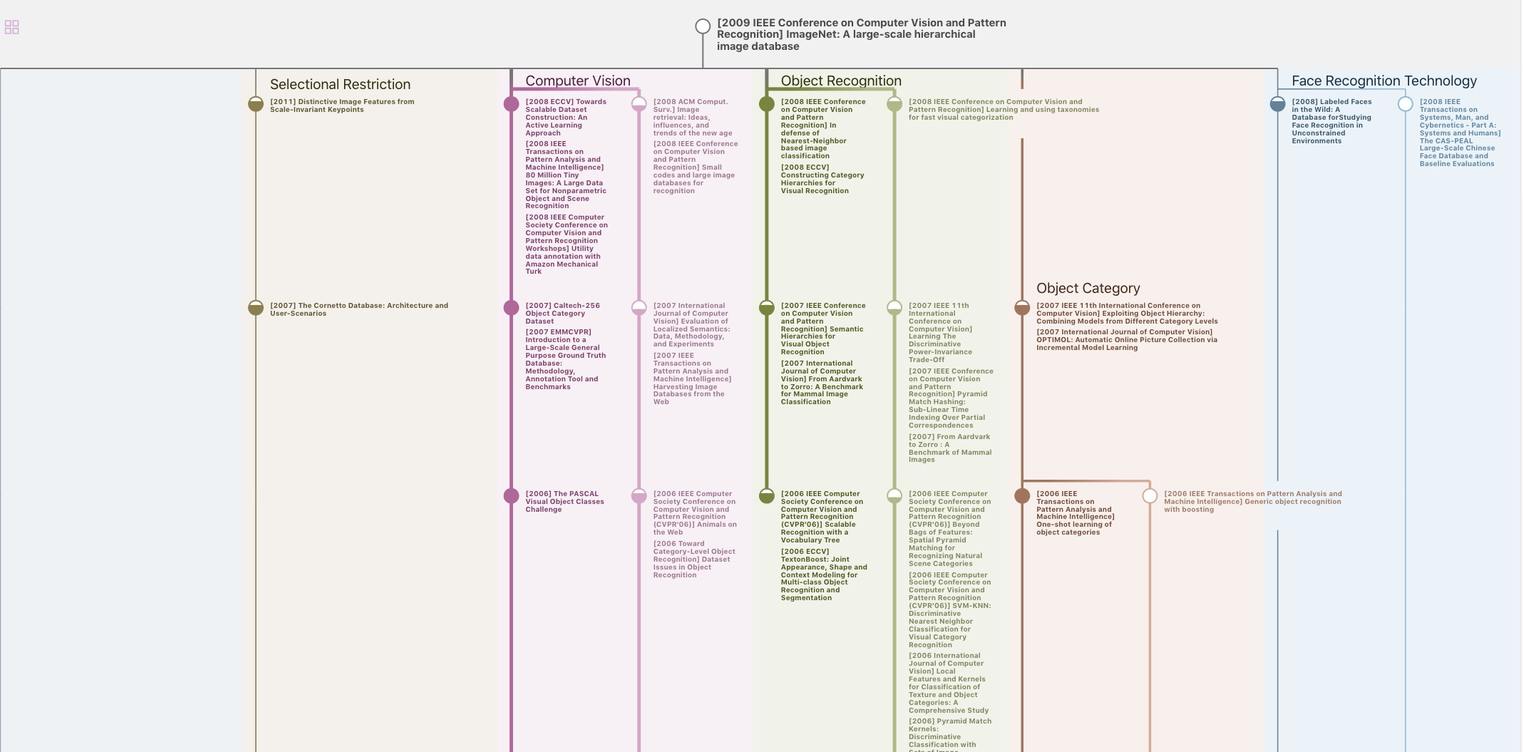
Generate MRT to find the research sequence of this paper
Chat Paper
Summary is being generated by the instructions you defined