Numerical investigation of the non-equilibrium condensation inside a fuel cell turbine with variable geometry
INTERNATIONAL JOURNAL OF HEAT AND MASS TRANSFER(2023)
Abstract
A turbine with variable geometry can fully recover energy from the fuel cell exhaust gas and effectively reduce parasitic power consumption of the compressor. In this study, an electric turbocharger is developed for a 100 kW fuel cell system. To investigate condensation occurring inside the turbine, a wet air condensation model based on a classical nucleation theory and the Hertz-Knudsen droplet model is proposed. Validation of the model is made by testing aerodynamic performances of the turbine. In order to do this, an air humidification bench is built and exhaust gas from the fuel cell cathode outlet is replaced by humidified high-pressure air. Numerical simulation and experiment results are in good agreement. Influences of nozzle vane angle and wall temperature of the turbine on its aerodynamic performances are examined. Results show that when the nozzle opening turns small, flow capacity of the turbine decreases, pressure at the nozzle outlet declines, and condensation is more likely to occur in the rotor area. As the wall temperature drops, area in which water vapor condenses rapidly moves forward from the rotor to the nozzle. Liquid water mass fraction at different locations increases approximately 5 % as the wall temperature decreases from 310 K to 290 K.
MoreTranslated text
Key words
Fuel cell,Variable geometry turbine,Non-equilibrium condensation,Nozzle vane angle,Wall temperature
AI Read Science
Must-Reading Tree
Example
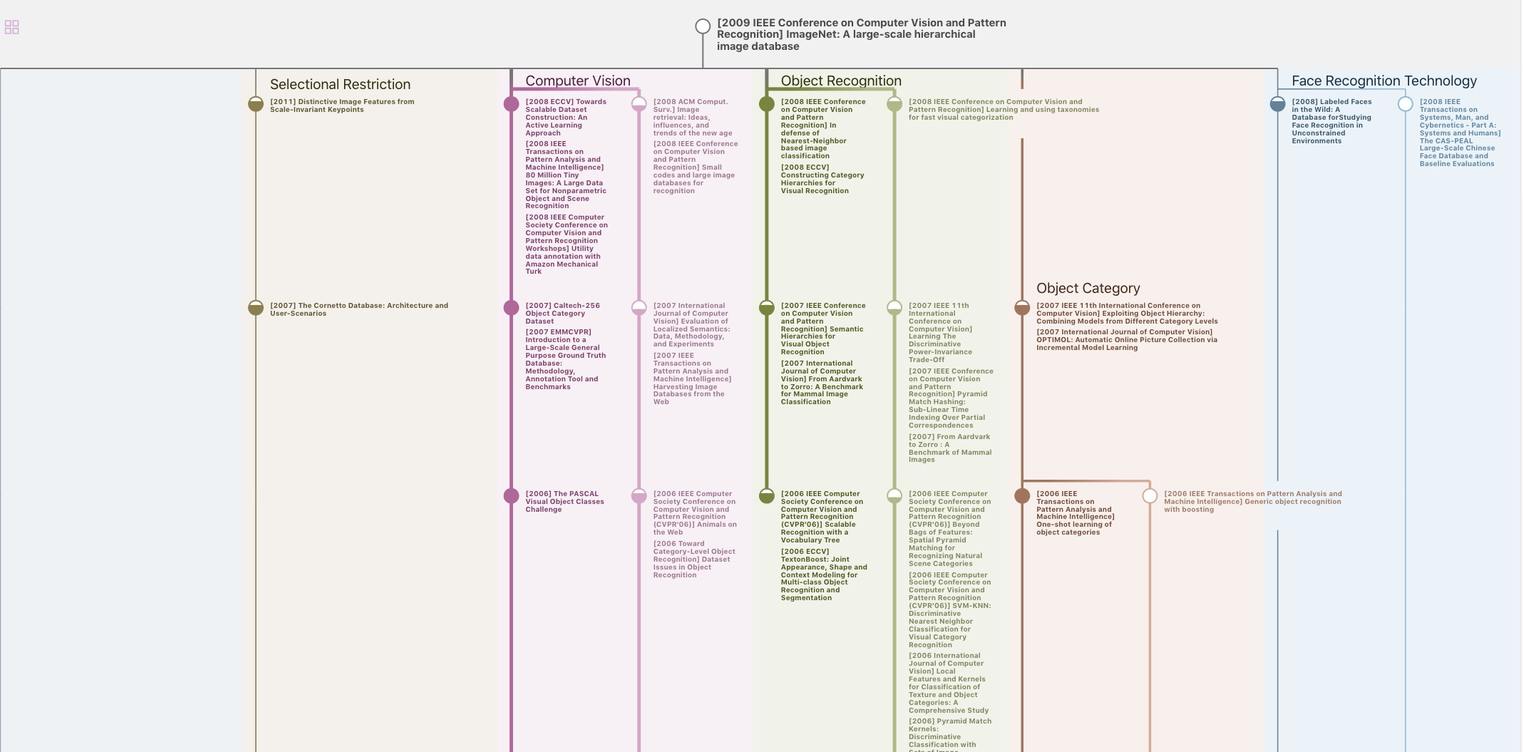
Generate MRT to find the research sequence of this paper
Chat Paper
Summary is being generated by the instructions you defined