Comparative study on energy efficiency and densification of ZnO ceramics using various sintering processes
JOURNAL OF MATERIALS SCIENCE-MATERIALS IN ELECTRONICS(2023)
摘要
Regarding the recent energy costs and Net-Zero carbon emissions concerns, energy efficient and sustainable manufacturing technologies are becoming an important topic in the ceramic industry. In this work, we make a comparison for the energy consumption and densification processes of Zinc oxide (ZnO) ceramics fabricated using conventional solid-state sintering (CSS), spark plasma sintering (SPS), cold sintering process (CSP), and hybrid cold sintering process/spark plasma sintering (CSP-SPS). In order to achieve high dense ZnO ceramics (≥ 99%), the energy consumption using various sintering routes is obtained, i.e. 59080 kJ/g, 3715.7 kJ/g, 622.5 kJ/g and 679.2 kJ/g for CSS, SPS, CSP and CSP-SPS, respectively. Moreover, microstructural results show that the grain size of ZnO ceramics grows from 0.20 μm of the starting powder to 0.403 and 0.841 μm using CSP and CSP-SPS, while the values increase significantly to 6.63 and 10.09 μm for samples sintered by SPS and CSS, respectively. The apparent activation energies of grain growth for CSP and CSP-SPS samples are 18 (± 2.1) and 35.3 (± 4.3) kJ/mol, much lower than 238.6 (± 20.8) and 269 (± 13.9) kJ/mol of CSS and SPS samples. Additionally, it is found that SPS sample presents the lowest grain boundary resistance of 6.57 × 10 3 Ω, while CSP sample displays the highest grain boundary resistance of 5.27 × 10 6 Ω. This research demonstrates that ZnO ceramics can be effectively densified with a moderate grain growth by utilizing novel CSP and CSP-SPS, which reduces the energy consumption by more than an order of magnitude comparing with CSS.
更多查看译文
关键词
zno ceramics
AI 理解论文
溯源树
样例
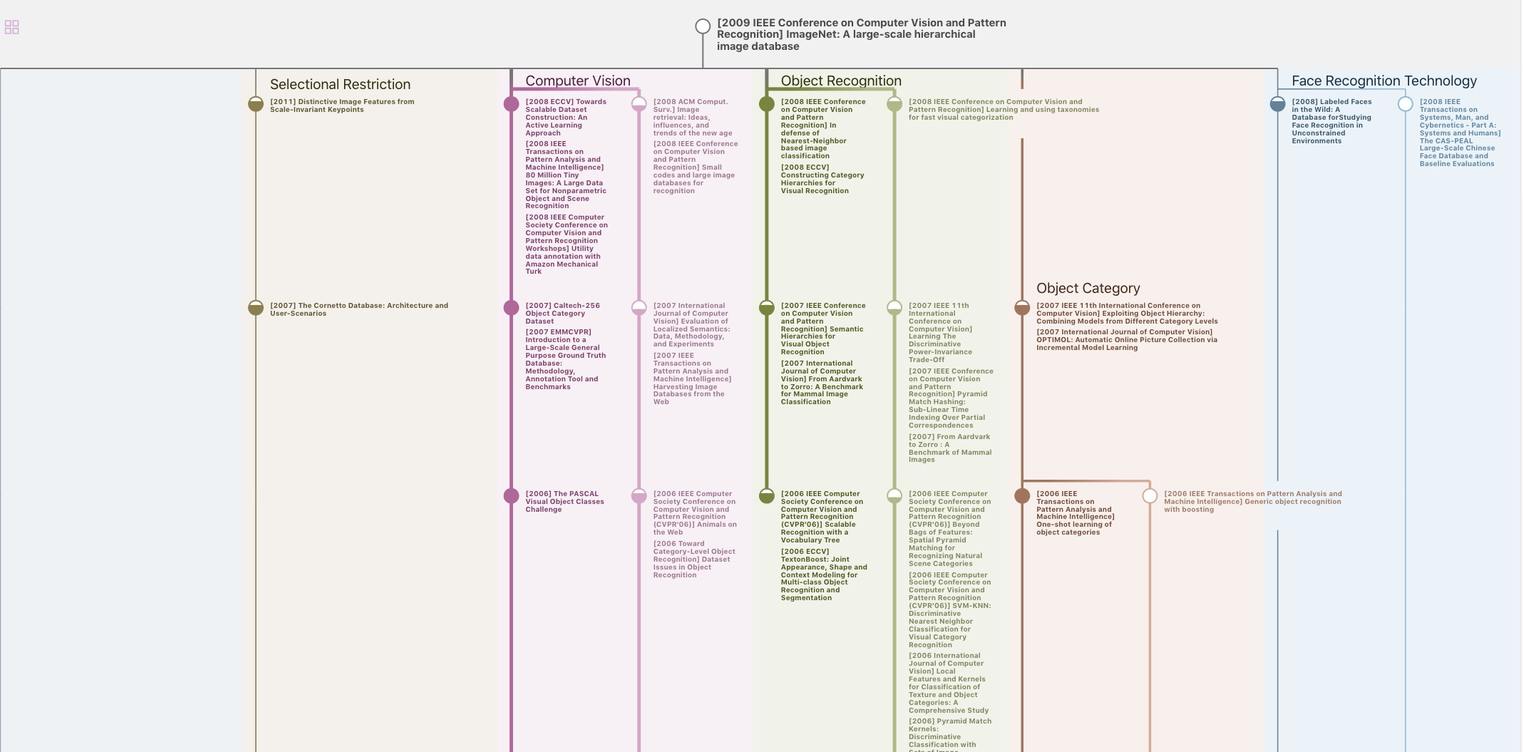
生成溯源树,研究论文发展脉络
Chat Paper
正在生成论文摘要