A new effective decoupling method to identify the tracking errors of the motion axes of the five-axis machine tools
JOURNAL OF INTELLIGENT MANUFACTURING(2023)
摘要
Currently, there are demands for machine tools with higher dynamic performance as a result of their high machining accuracy and efficiency in designing complex parts in the manufacturing industry. The motion delays in each of the motion axes cause dynamic tracking errors or tool tracking errors which greatly affect the surface quality of machined parts; hence, tuning the dynamic parameters like the position gains of the motion axis causing the defect is as good as eliminating the error source rather than tuning the parameters of all the motion axes. This work proposes a decoupling method to identify the particular motion axis that greatly affects or causes the tool tracking error by using the ISO BK3 kinematic test, and this involves orientation contour error estimation and motion axis error computation based on inverse kinematics of the machine tool transformation. An experiment was carried out on an industrial machine tool with a tilting rotary table to verify the simulation results; the feed servo system model of the motion axes was constructed using MATLAB Simulink tools. The results obtained show that the tool tracking errors are greatly influenced by some dynamic parameters like the feedrate and the position gains emanating from a particular motion axis with dynamic deficiency, and the proposed decoupling method robustly identifies the individual motion axes greatly affecting the dynamic tracking error which makes it very relevant to tune only the dynamic parameters of those particular motion axes instead tuning all. Moreover, this method is simple and robust, and its implementation can help improve the dynamic performance of machine tools in the manufacturing industry.
更多查看译文
关键词
Machine tool, Tracking error, Motion axis, Decoupling
AI 理解论文
溯源树
样例
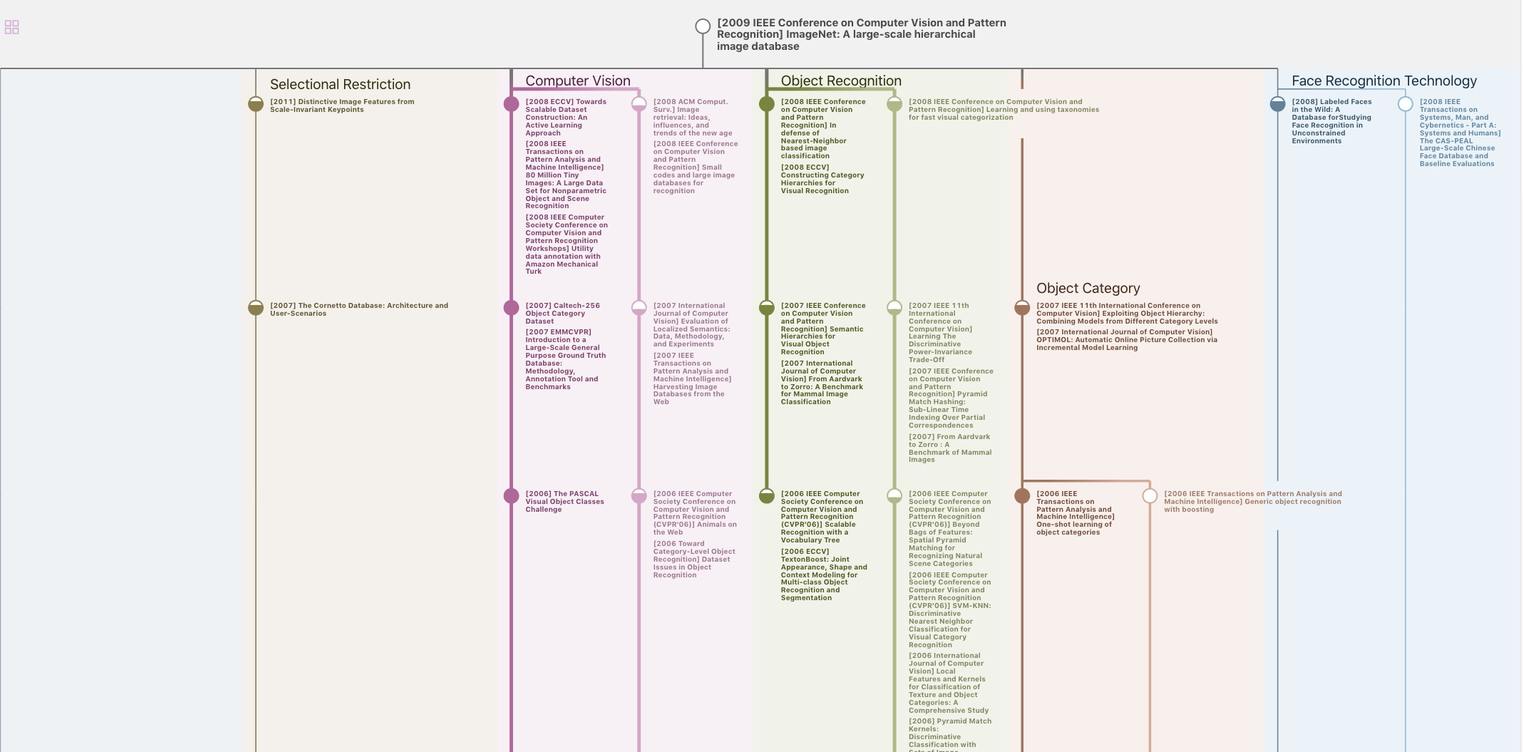
生成溯源树,研究论文发展脉络
Chat Paper
正在生成论文摘要