Experimental and Numerical Investigation of Injection Molding Main Parameters’ Effects on Shrinkage and Warpage of a Thin Sheet Made of HDPE
International Journal of Advanced Design and Manufacturing Technology(2022)
Abstract
Injection molding is one of the common processes for producing plastic parts. In this process, the mold is filled immediately and then the part and mold will be cooled down during the packing time. In the end, the part will be ejected from the mold. In this study, the effects of the most important processing parameters such as packing time, melt and mold temperature have been investigated on shrinkage and warpage of the products experimentally and numerically. According to previous reports, a thin sheet is defined by a length to thickness ratio of at least 100. MOLDFLOW software has been utilized to obtain the numerical results. For the empirical study, 64 specimens have been produced in different production conditions. These samples have been scanned by a 3D scanner and results have been analyzed by CATIA software. The findings show that increasing melt and mold temperature decreases the warpage amount and rises the shrinkage in the specimens. Also increasing the packing time up to 2 seconds increases the warpage and decreases the shrinkage noticeably but in longer packing times the variations will be less remarkable. Moreover, findings show that the general trend in simulated and experimental results are similar in all reported values of shrinkage and warpage, in which the maximum calculated errors for both of them are approximately 10%.
MoreTranslated text
Key words
hdpe,injection molding,melts and mold temperature,packing time,shrinkage,warpage
AI Read Science
Must-Reading Tree
Example
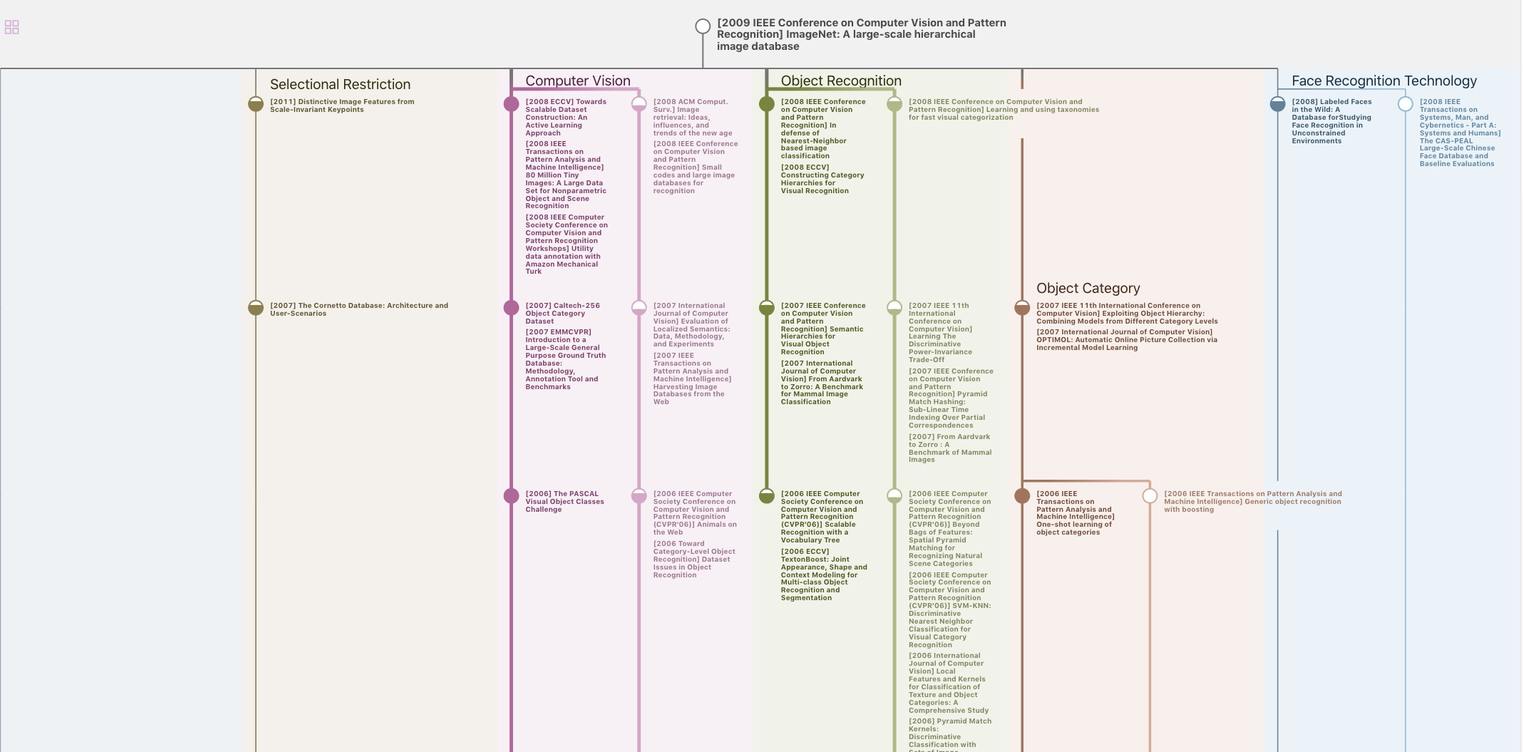
Generate MRT to find the research sequence of this paper
Chat Paper
Summary is being generated by the instructions you defined