Influence of surface treatment on metal dusting resistance of welds
MATERIALS AND CORROSION-WERKSTOFFE UND KORROSION(2024)
Abstract
Welds of the commercial Ni-based alloys 602 CA, 699 XA, 601 and 690 were exposed under harsh metal dusting conditions. The pit formation was compared for as-welded, brushed, ground, glass bead blasted, steel shot peened and dry cathodic pickled surfaces. Surface treatments were applied by industrial partners. When (stainless) steels were involved in the surface treatment, Fe contaminations acted as catalyst sites for pit initiation. A fast metal dusting attack was also observed on dry cathodic pickled samples. A beneficial effect was attributed to deformation of the sub-surface zone, as it provides diffusion paths for oxide formers (by grinding and glass bead blasting). In the same region, formation of & alpha;-Cr (BCC) precipitates was observed. The best performance was found for samples where the weld bead was fully flattened by grinding to P40 grit. In addition, it was demonstrated that on-site slurry aluminization further enhances the resistance against metal dusting attack. Fe contaminations enhanced metal dusting pit formation on brushed welds of Ni-based alloys. The best performance of the welds was achieved by grinding, this is attributed to the deformation of the sub-surface zone. Additional protection by on-site slurry aluminization was successfully demonstrated.image
MoreTranslated text
Key words
aluminum diffusion coating,deformed zone,metal dusting,Ni-based alloys,protective oxide,surface treatment
AI Read Science
Must-Reading Tree
Example
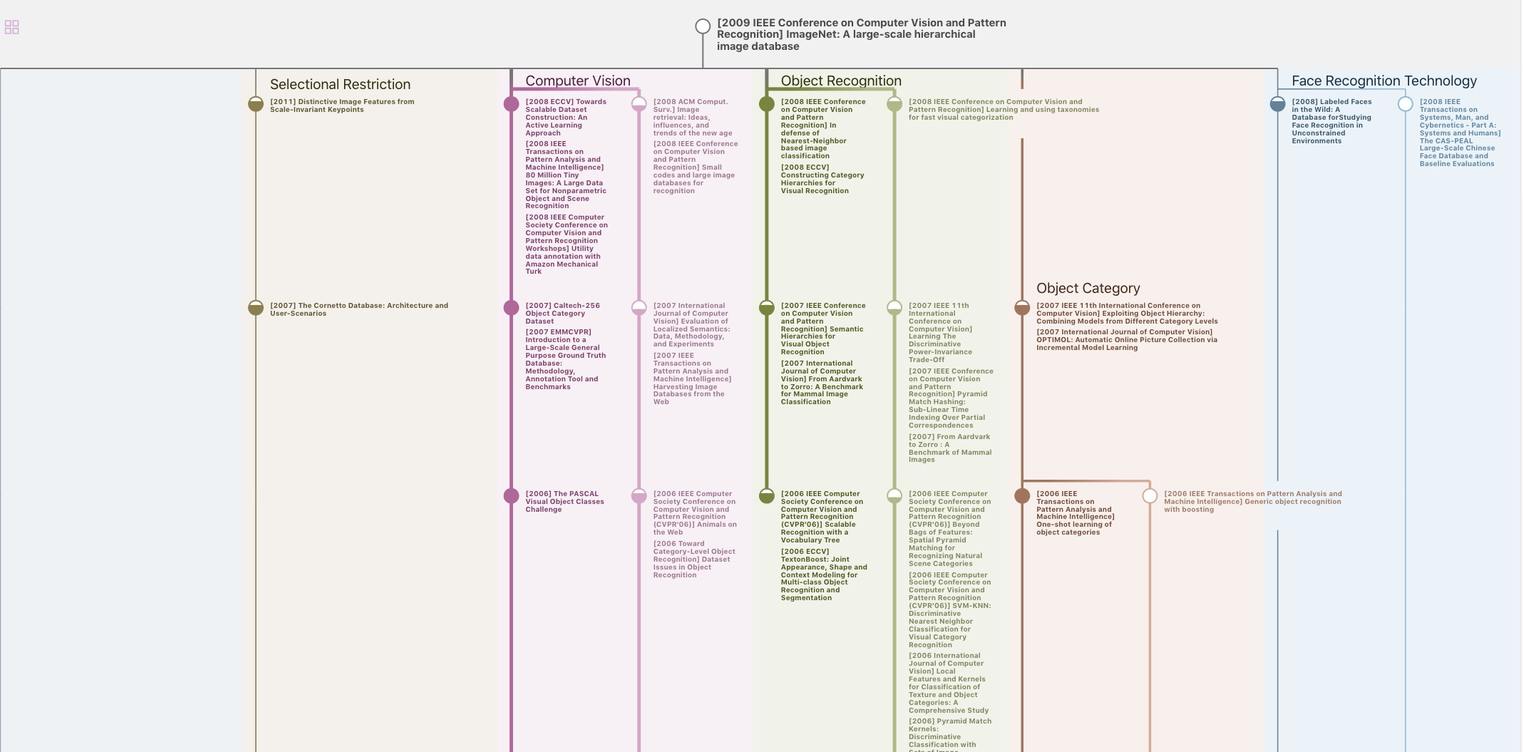
Generate MRT to find the research sequence of this paper
Chat Paper
Summary is being generated by the instructions you defined