Application of Digital Twin for Real-Time Early Identification and Warning of Pipe Stuck Using Hybrid Approach of Physics Model and Machine Learning
Day 4 Thu, October 05, 2023(2023)
Abstract
Abstract Pipe Stuck is one of the predominant causes for drilling-related non-productive time (NPT). According to statistics, losses up to hundreds of millions of dollars are caused by pipe stuck globally each year. Early identification and warning of pipe stuck are essential for predicting and avoiding stuck issue once preventive measures are taken promptly. Typical detecting methods based on data fluctuation amplitude or curve trends subject to expert user experience and human error. Moreover, pipe stuck usually have already happened in most cases when noticed by these methods. This paper presents an innovative system combing physics model with machine learning method, which enables automatically pipe stuck risk monitoring and warning while drilling. The new system combines these approaches: 1)real-time calculation of hook load, torque and standpipe pressure(SPP) for 9 different drilling states (rotary drilling, slide drilling, reaming, back-reaming, tripping in, tripping out and etc.) based on drill string mechanics and wellbore hydraulics model; 2)The calculated parameters are checked and calibrated automatically within set computing cycle to narrow down calculation error; 3) The deviation of actual parameters from theoretical modeled value and rate of change(ROC) of actual parameters are calculated and compared on time-series, based on which a pipe stuck risk index (PSRI) is proposed ranging from 0% to 100%; 4) With different risk index ranges, pipe stuck risk level is monitored and evaluated as low (green), medium(yellow) and high(red) on real-time basis. For historical wells with and without pipe stuck issues under different drilling states, thresholds for deviation and ROC of parameters corresponding to different risk levels are obtained by random forest algorithm (RFA). The system is designed to provide users, driller or monitoring specialist a warning signal with prompt window jumping out and constant beep sound whenever a high-risk is identified. Once detected, preventive or intervention measures are generally mandatory for on-site personnels. Application cases showed that alerting warning of high-risk of pipe stuck could be realized typically between 30 minutes and 2 hours ahead during back-reaming and tripping operations, which demonstrated the system capability for early identification and warning of pipe stuck under different drilling states. The new system showed that digital twin driven technique could provide effective solution for detecting the onset of pipe stuck, which could help to minimize NPT, better capture and utilize digital data for optimizing drilling.
MoreTranslated text
AI Read Science
Must-Reading Tree
Example
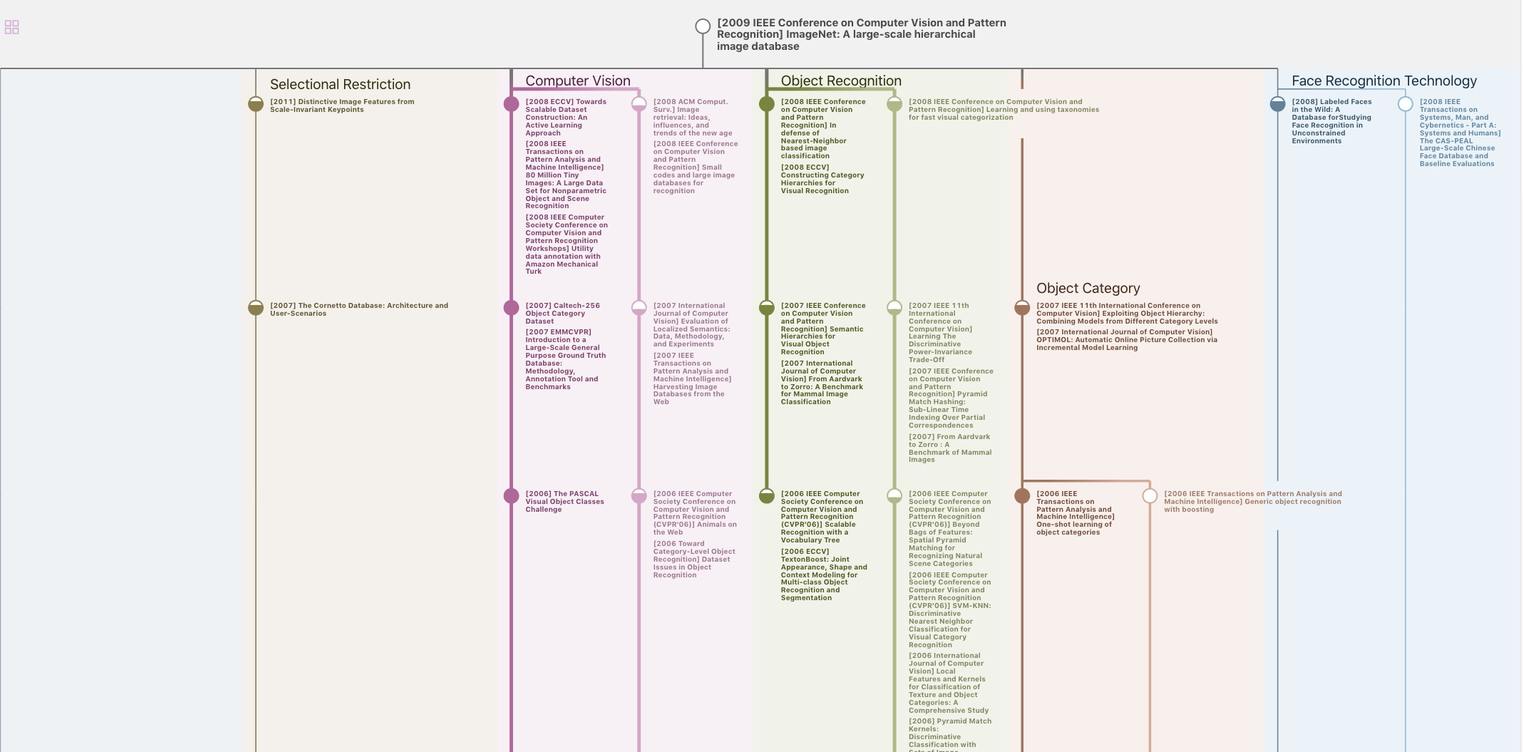
Generate MRT to find the research sequence of this paper
Chat Paper
Summary is being generated by the instructions you defined