Digital twin model-driven capacity evaluation and scheduling optimization for ship welding production line
JOURNAL OF INTELLIGENT MANUFACTURING(2023)
Abstract
Approximately 45% of ship delivery delays are due to welding quality. To solve the problematic control of production tempo and process sequence optimization in the welding process, it is urgent to combine the characteristics of the digital twin for dynamic simulation and optimization. Therefore, the capacity evaluation and scheduling optimization for the ship welding production line (WPL) based on the digital twin is proposed. Firstly, to describe the construction method of the digital twin model and digital twin data, a strategy is proposed for the construction of a digital twin ship component WPL model. Based on the fusion mapping of model and data, the construction of the digital twin model for WPL (DTM-WPL) is achieved. Secondly, by using equipment failure rate, processing time and buffer capacity as evaluation indicators, an WPL optimization model based on digital twins is constructed to solve the WPL production sequencing problem. Thirdly, to illustrate the welding quality traceability and prediction process, a DTM-WPL synchronous mapping for quality prediction and adjustment method is proposed. Finally, taking small and medium-sized WPL as the research object, the capacity evaluation and scheduling optimization system of ship components is developed to evaluate the production capacity of ship components. The validation results indicate that the optimized process scheme has increased production efficiency by 7.27%.
MoreTranslated text
Key words
Welding production line,Digital twin,Capacity evaluation,Scheduling optimization
AI Read Science
Must-Reading Tree
Example
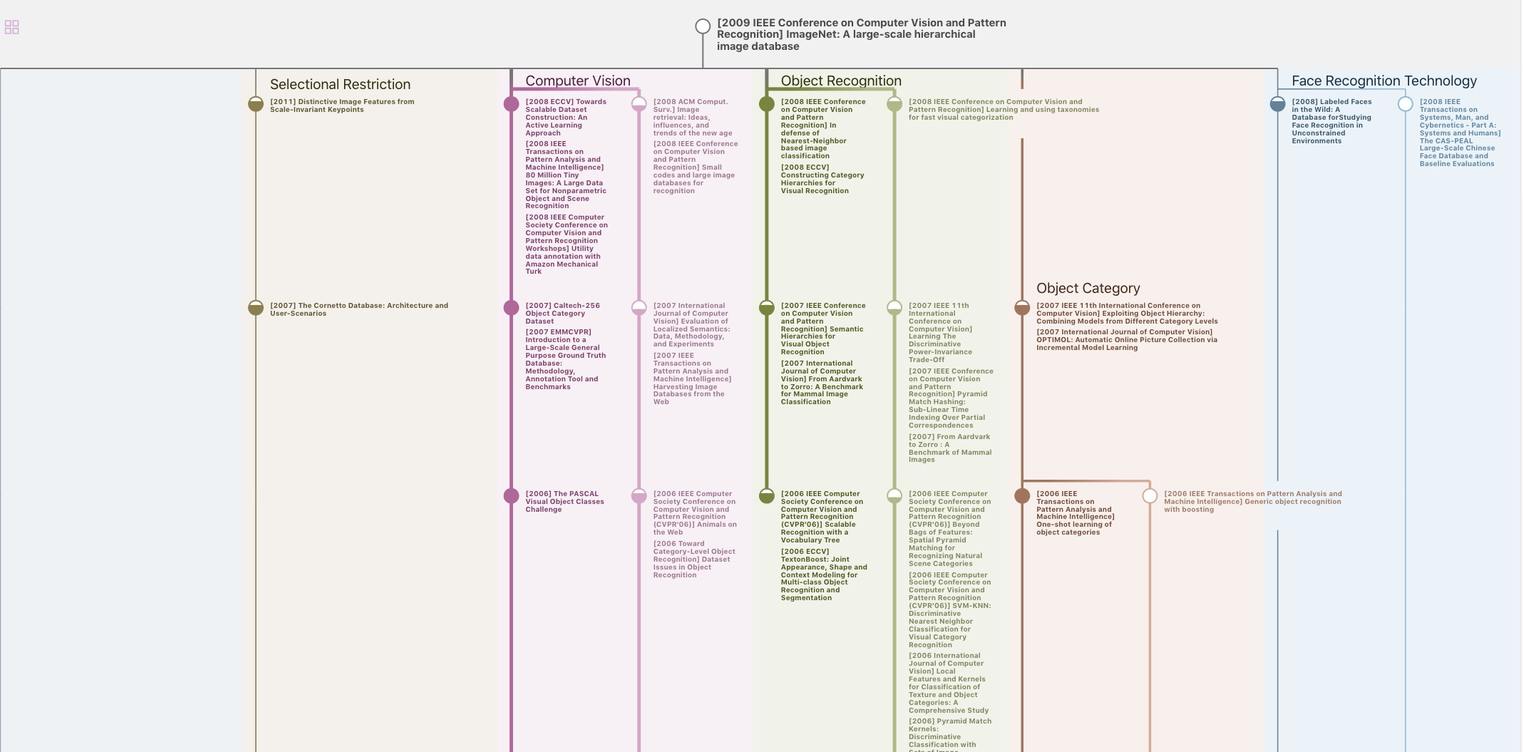
Generate MRT to find the research sequence of this paper
Chat Paper
Summary is being generated by the instructions you defined