Investigation of Effect of Processing Parameters for Direct Energy Deposition Additive Manufacturing Technologies
JOURNAL OF MANUFACTURING AND MATERIALS PROCESSING(2023)
摘要
In order to capitalize on the cost-effectiveness of additive manufacturing (AM), it is critical to understand how to build components with consistency and high quality. Directed energy deposition (DED) is an AM method for creating parts layer by layer through the use of a moving heat source and powder material inserted into the melt pool generated on the substrate. DED, like most AM processes, is highly complex due to the rapid thermal gradients experienced during processing. These thermal gradients are determined by a variety of processing parameters, which include laser power, powder feed rate, travel speed, layer height hatch spacing, etc. A lot of effort has been carried out in the additive manufacturing community to understand what these critical parameters are and how they influence the thermal gradients. Despite all these efforts, AM industries rely on a trial-and-error-based approach to find the right set of parameters to produce a quality part. This is time-consuming and not a cost-effective use of AM technology. The aim of our research is to reduce the amount of experimental data in combination with numerical analysis to optimize this relationship. Physics-based two-dimensional melt-pool modeling and experimental results from an OPTOMEC 850M LENS will be utilized to investigate the effects of processing parameters on melt-pool geometry, and the results from this study will provide key processing guidelines to achieve desirable clad geometry and powder efficiency for the DED method.
更多查看译文
关键词
additive manufacturing, clad geometry, direct energy deposition, melt pool modeling, powder efficiency, process map
AI 理解论文
溯源树
样例
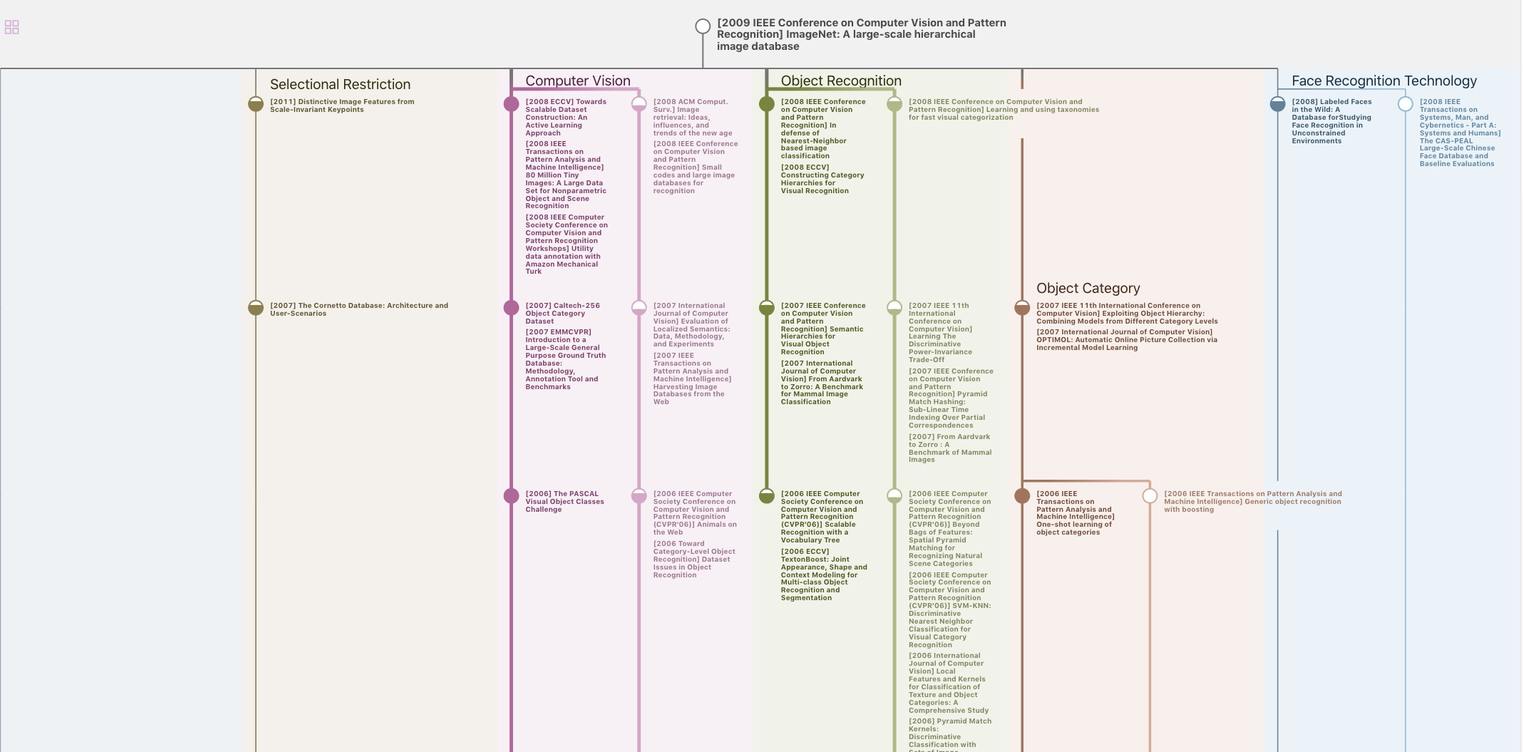
生成溯源树,研究论文发展脉络
Chat Paper
正在生成论文摘要