Hot-filament Chemical Vapour Deposition of Microcrystalline Diamond Layers for Grinding Applications
crossref(2015)
摘要
Rough, microcrystalline CVD diamond layers are under research for many years for grinding applications. This contribution will present an overview about the results, both for film development and for application tests. The crystallite protrusions of microcrystalline CVD diamond layers act as micro cutting edges. Thus, the CVD diamond film forms a grinding layer on tools for abrasive machining, like grinding wheels or abrasive pencils (burrs, points). Such grinding layers have significant advantages compared to conventional diamond grinding layers, which are formed by bonding of diamond grains onto the tool base body. The development comprises CVD diamond layers that have been deposited on silicon nitride and silicon carbide tool base bodies with diameters up to 290 mm to form grinding wheels. For the preparation of the diamond layers our unique large-scale hot-filament CVD reactor with a coating area of 1000 mm 500 mm was used which is already industrialized for the production of diamond electrodes, face seals, and bearings, respectively. The process was adjusted to achieve film thicknesses of 20 m with tolerances below 1 m over the full grinding wheel area. The height of the crystallite protrusions was up to 4 m; this protrusion corresponds to a grit size of D 12 for conventional bonded diamond grinding layers. The grinding wheels achieved a much better workpiece roughness in the machining of glass, alumina, and cermets. It is assumed that this is due to the number of protrusions, which is by factor of 2 to 7 higher compared to bonded grinding layers, depending on the grit size. Additionally the CVD diamond grinding wheels showed a strongly reduced wear rate. It was 10 to 80 times lower compared to conventional bonded diamond grinding layers. This improvement is due to the much higher number of diamond micro cutting edges and the larger diamond volume that can withstand the wear for a longer time. Furthermore a process technique was developed to regenerate worn CVD diamond layers. During machining the diamond crystallite tips are flattened. It was shown that a short epitaxial-like CVD process is able to recreate the crystallite tips without a significant increase of crystallite size. In such a way the CVD grinding tool can be re-sharpened and re-used. Grinding tests have shown that the machining performance is the same as for newly coated CVD grinding layers. The contribution will also present the development of micro abrasive pencils with CVD diamond coating. Microcrystalline CVD diamond layers have been deposited on cemented carbide tool base bodies with cylindrical tip shape. Due to the ability of the CVD process to coat complex substrate geometries the tools have been coated very uniformly. The abrasive pencils were tested and showed low work piece roughness and very long tool life times. The smallest abrasive pencil that was developed and tested successfully had a diameter of 0.05 mm. The presentation will be complemented by results of the development of honing tools.
更多查看译文
AI 理解论文
溯源树
样例
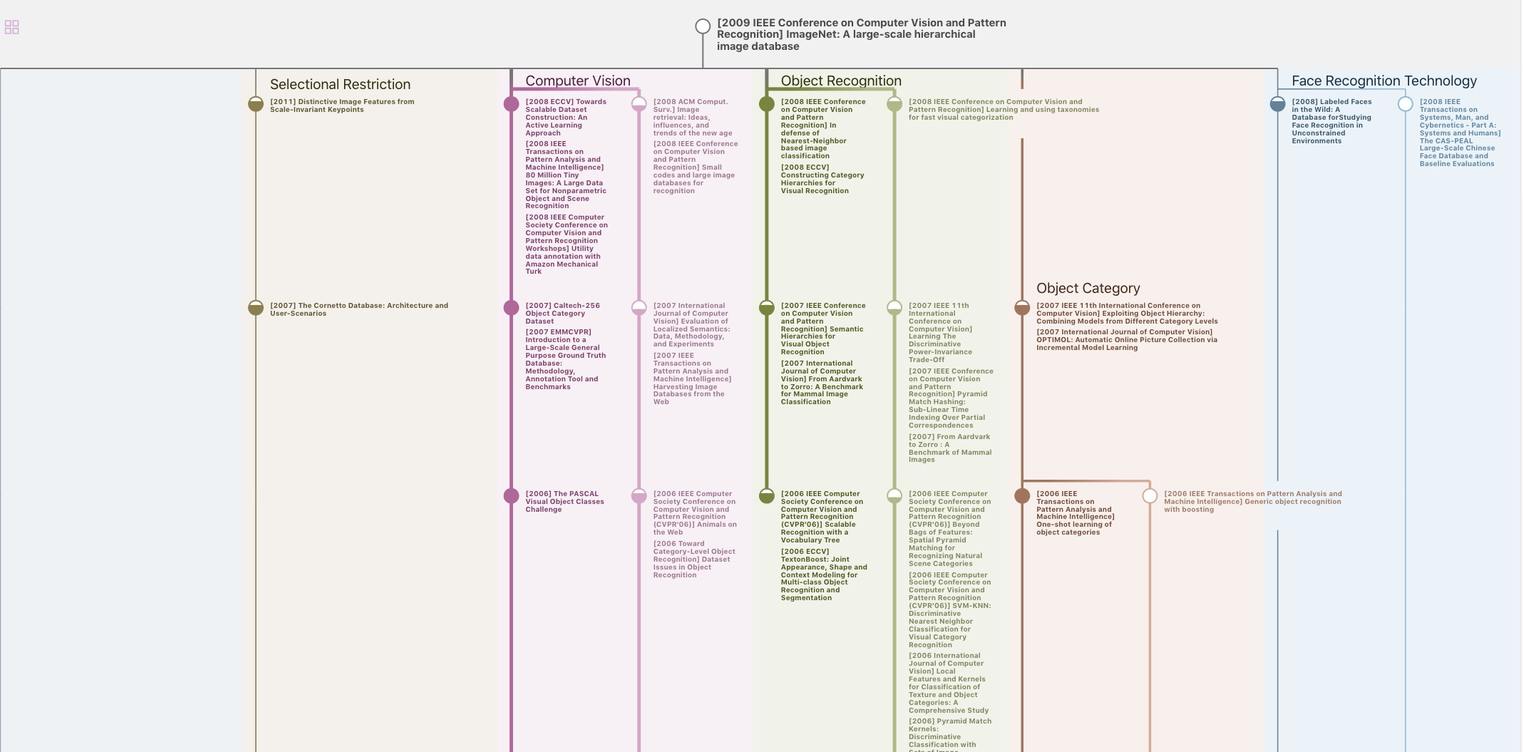
生成溯源树,研究论文发展脉络
Chat Paper
正在生成论文摘要