A Variable Stiffness End-of-Arm Mechanism for Safe Operation in Industrial Environments
Volume 7: 46th Mechanisms and Robotics Conference (MR)(2022)
摘要
Abstract In robotic manipulation, uncertainties in the operating environment can result in the exchange of unintended forces that can harm the operator, robot, tool, or the operating environment. In this study, we present a variable stiffness end-of-arm mechanism (VSEAM) to improve the collision safety of industrial robots. In VSEAM, the endpoint stiffness of the robotic manipulator is controlled using the displacement of permanent magnets. Additionally, a calibrated force model is developed for these magnets to detect external collisions. In the event of an unintended collision, the nonlinear compliance of the VSEAM provides passive displacement of the tool and provides enough time for the robot to react to the collision. Such passive displacement helps in absorbing the partial impact energy and thus protects the tool and the environment from damage. The proposed mechanism is validated during unintended collisions with two different operational speeds (end-effector speeds of 0.3 m/s, and 0.5 m/s) and two different loads at the end-effector (0.4 Kg and 1 Kg). The transmitted forces in low and medium stiffness settings of the VSEAM is compared to the high stiffness setting of the robot (in the absence of the VSEAM) demonstrating the capability of the proposed system to reduce the transmitted forced by approximately 50%.
更多查看译文
AI 理解论文
溯源树
样例
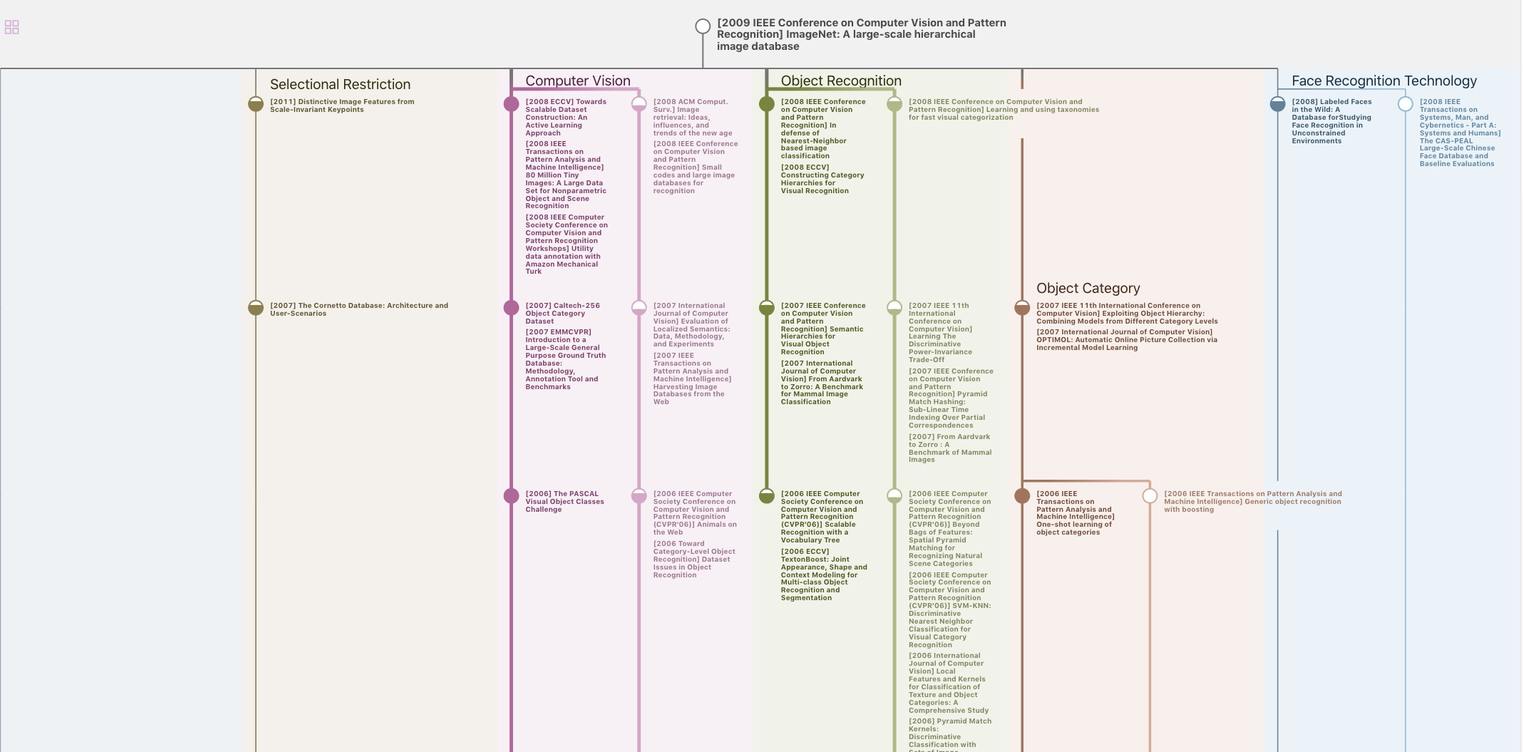
生成溯源树,研究论文发展脉络
Chat Paper
正在生成论文摘要