Thermal Analysis and Design of Self-Heating Molds Using Large-Scale Additive Manufacturing for Out-of-Autoclave Applications
OSTI OAI (US Department of Energy Office of Scientific and Technical Information)(2022)
关键词
Large Scale Additive Manufacturing,Carbon-fiber reinforced composites,3D Printing,Heat Transfer,Thermal Analysis,Wire embedding,Out-of-autoclave Manufacturing,Composite Mold
AI 理解论文
溯源树
样例
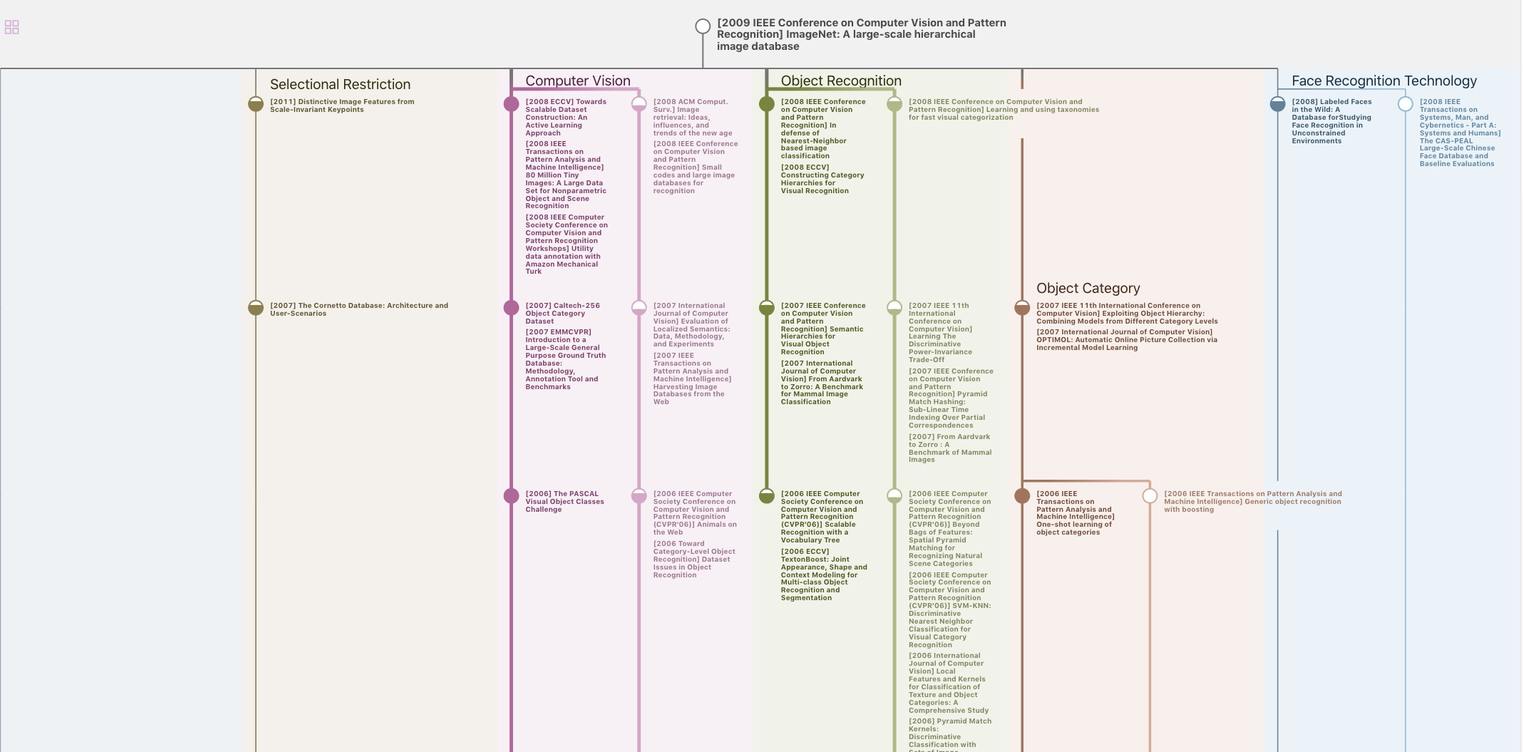
生成溯源树,研究论文发展脉络
Chat Paper
正在生成论文摘要