Numerical Simulation of Coated Proppant Transport and Placement in Hydraulic Fractures Based on CFD-DEM
Petroleum science and technology(2023)
Abstract
Channel fracturing technology is designed to form fractures supported by non-uniform pillar proppants. Non-cured adhesive resin-coated proppant gradually becomes viscous after immersion and agglomerates during transportation. The pillars are stable after the fracture is closed. They not only maintain a certain compressive strength but also maintain long-term conductivity. Currently, there are few evaluations of coated proppant migration. Based on CFD-DEM method, a two-phase flow coupling model considering the adhesive contact force of coated proppant particles is established to study the cementation characteristics of coated proppant during transportation. The transportation mechanism of coated proppant are revealed by numerical calculation analysis. The results show that different from the conventional proppant, the migration process of the coated proppant is divided into four stages (1) the softening of the proppant contact; (2) the paving of the proppant agglomeration; (3) proppant pillars growth along fracture height; and (4) proppant pillars growth along fracture length. We have completed a preliminary geometric characteristics evaluation of sand bank formed by coated proppant by evaluating the pore volume ratio (the ratio of void volume between pillars to the sand bank volume) under various parameters. This evaluation offers some theoretical guidance for the optimization of channel fracturing proppant injection parameters.
MoreTranslated text
Key words
CFD-DEM,channel fracturing,coated proppant,numerical simulation,proppant transportation
AI Read Science
Must-Reading Tree
Example
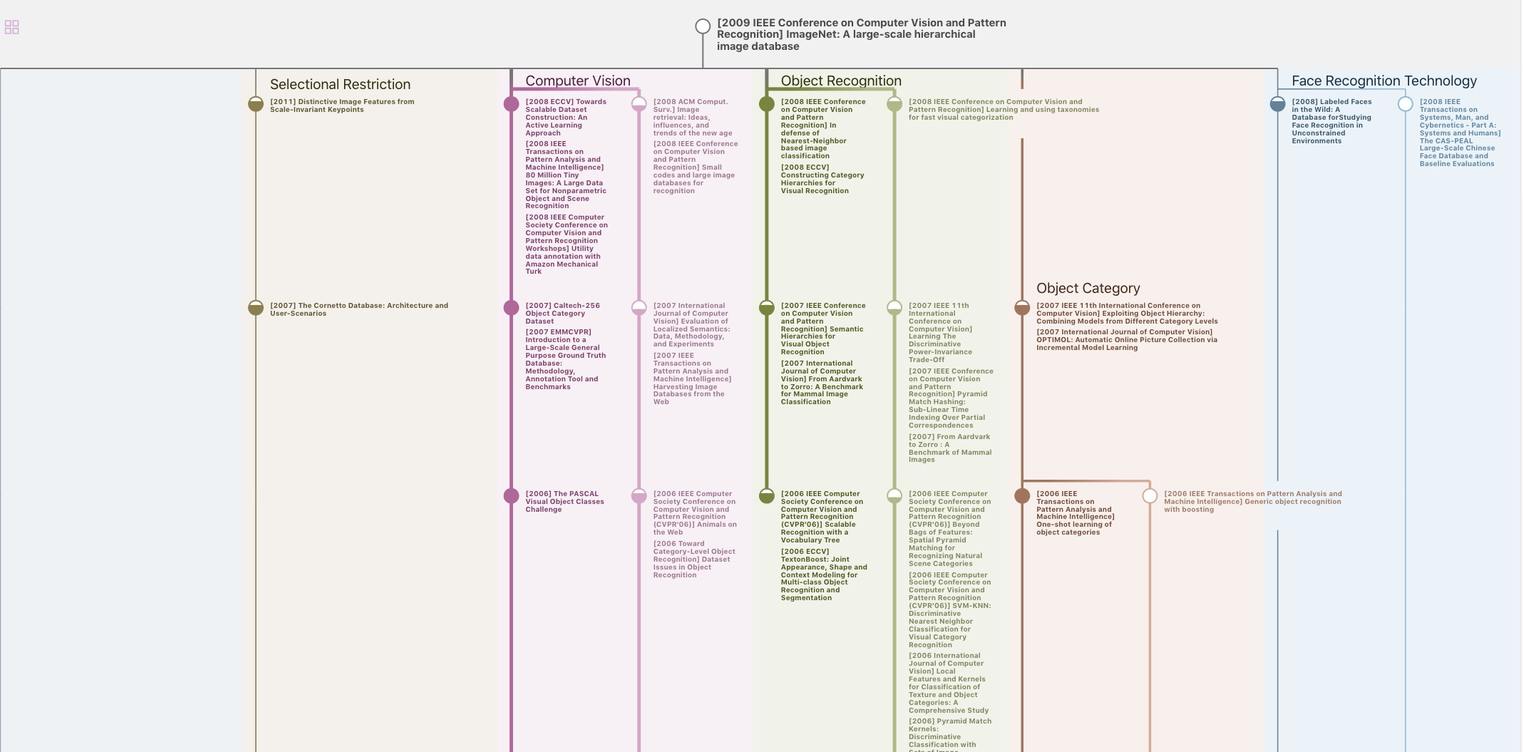
Generate MRT to find the research sequence of this paper
Chat Paper
Summary is being generated by the instructions you defined