Tool wear reduction in ultrasonic vibration-assisted turning of SiC-reinforced metal-matrix composite
Wear(2023)
Abstract
In recent years, metal matrix composites (MMCs) have attracted the interest of various industrial sectors thanks to the benefits they offer in terms of lightness and mechanical properties compared to equivalent non-reinforced metallic alloys. Nevertheless, when machining MMCs, their heterogeneous structure, specifically characterized by the presence of hard particles within a much more ductile matrix, induces different thermal and mechanical loads when the cutting edge passes through the various composite constituents. This, in turn, may drastically reduce the cutting tool life as well as deteriorate the part surface integrity leading to poor in-service performances of the part. Nonconventional machining methods are usually employed to manufacture parts made of MMCs, nevertheless at the cost of scarce workpiece surface integrity and increased manufacturing burdens. To overcome the above-mentioned issues, ultrasonic vibration-assisted turning (UVAT) is proposed in this study as an efficient approach to machine MMCs. Turning trials with and without the application of ultrasonic vibration were carried out at varying cutting speeds, feed and volume of removed material. The tool wear mechanisms were identified and quantified. The surface finish and chip morphology were also analyzed as further machinability parameters for comparing the different machining approaches and assessing the advantages of UVAT. The obtained experimental results showed that the adoption of ultrasonic vibrations together with high feed can significantly increase the tool life, representing a suitable approach for efficiently machining MMCs.
MoreTranslated text
Key words
vibration-assisted,sic-reinforced,metal-matrix
AI Read Science
Must-Reading Tree
Example
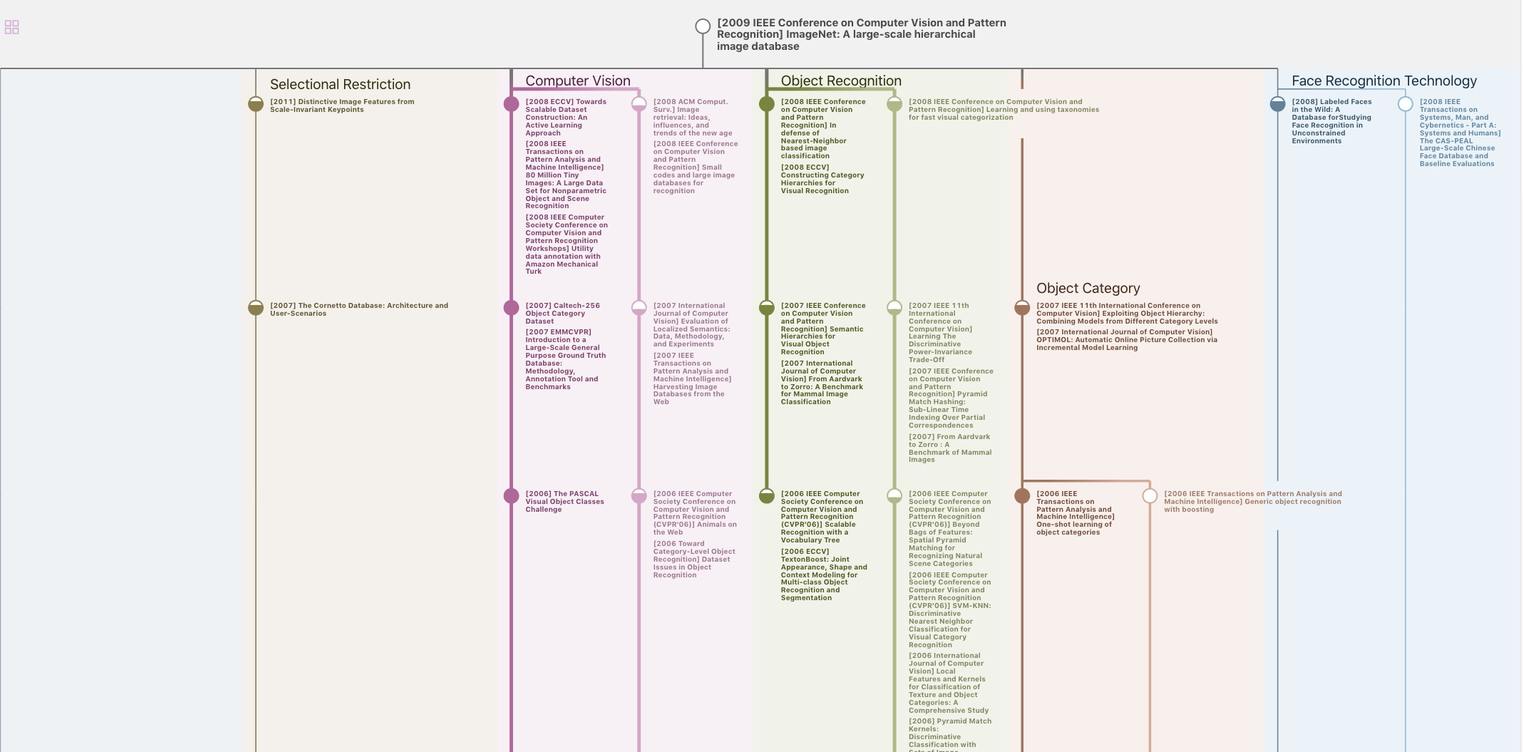
Generate MRT to find the research sequence of this paper
Chat Paper
Summary is being generated by the instructions you defined