Towards a New Real-Time Metrology Guidance Method for Robotized Machining of Aerostructures Robust Against Cutting Fluids and Debris
INTERNATIONAL JOURNAL OF ADVANCED MANUFACTURING TECHNOLOGY(2023)
关键词
Robotic milling,Error compensation,Real-time feedback,Kinematic modeling,CMM-arm
AI 理解论文
溯源树
样例
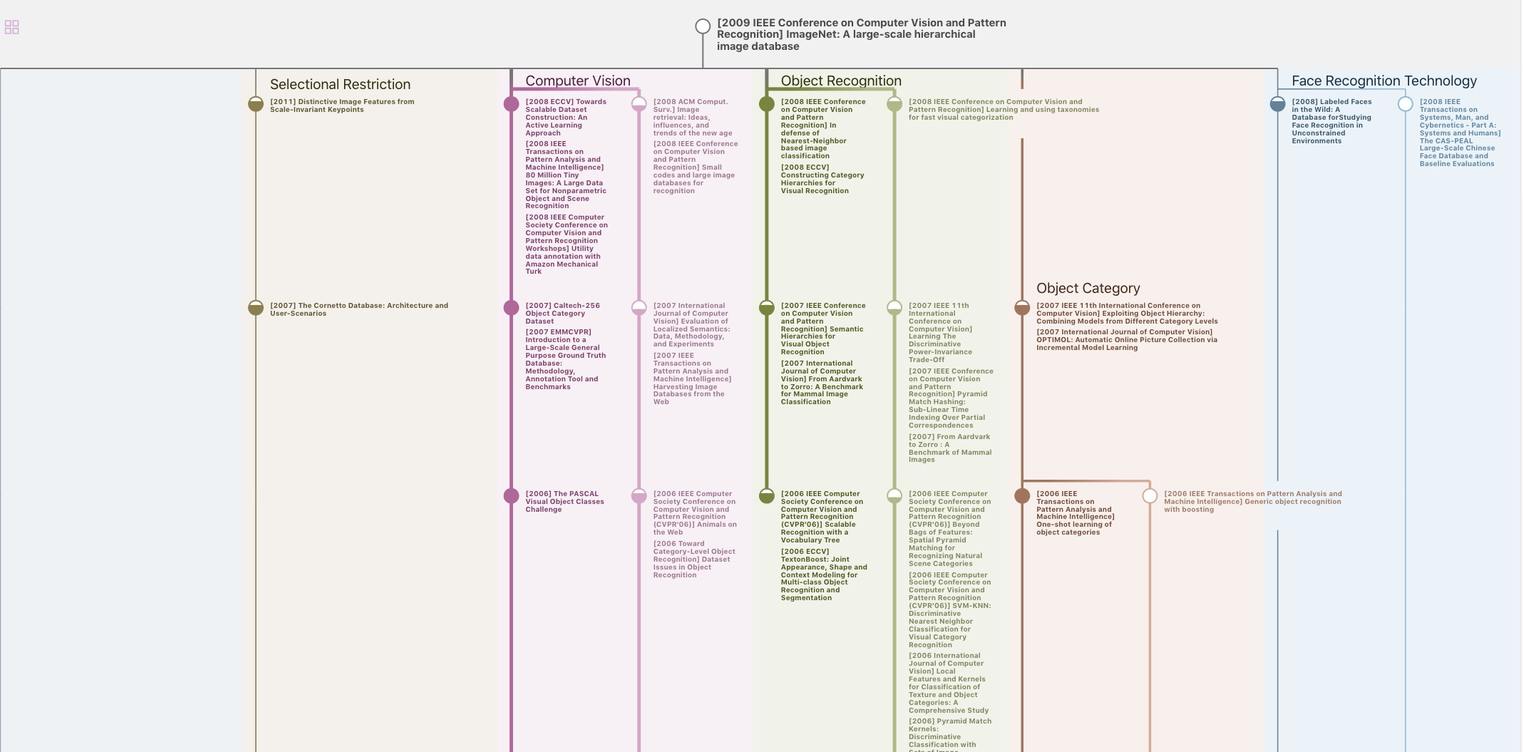
生成溯源树,研究论文发展脉络
Chat Paper
正在生成论文摘要