Efficient Computer-Based Method for Adjusting the Stiffness of Subject-Specific 3D-Printed Insoles during Walking
APPLIED SCIENCES-BASEL(2023)
摘要
Featured Application Quasi-static finite element model to adjust the stiffness of 3D-printed insoles during walking for patients with diabetic foot by using ankle moments and joint reaction forces as efficient boundary conditions. Diabetes-adapted insoles are essential in prevention and rehabilitation of foot ulcers in diabetic foot syndrome. However, their manufacture is labour-intensive and costly. Therefore, the study aims to present an alternative method that allows the individual adjustment of the stiffness of the insoles using the finite element (FE) method and subsequent 3D printing. In the study, 3D gait analysis followed by musculoskeletal modelling was used to determine the boundary conditions of a healthy subject for the FE model. While muscle forces are elaborately implemented in most studies, this FE model presented a more efficient way by using ankle moments and joint reaction forces. The deviation between the simulated plantar peak pressure and the experimentally determined using the Pedar system amounted to 234 kPa in the heel area and 30 kPa in the toe area. The stiffness of the individual insole was adjusted by applying soft insole plugs in areas where high plantar pressures occurred during walking. Three different Young's moduli were analysed in these areas (0.5 MPa, 1.0 MPa, 1.5 MPa). The computer-based approach to adjust the stiffness of an individual insole revealed a plantar peak pressure reduction by 37% in the heel area and by 119% in the toe area with a Young's modulus of 0.5 MPa. The presented method could be a valuable tool in the cost-efficient development and engineering of subject-specific 3D-printed insoles for patients with diabetic foot syndrome.
更多查看译文
关键词
diabetic foot,insole,3D printing,finite element analysis,musculoskeletal modelling
AI 理解论文
溯源树
样例
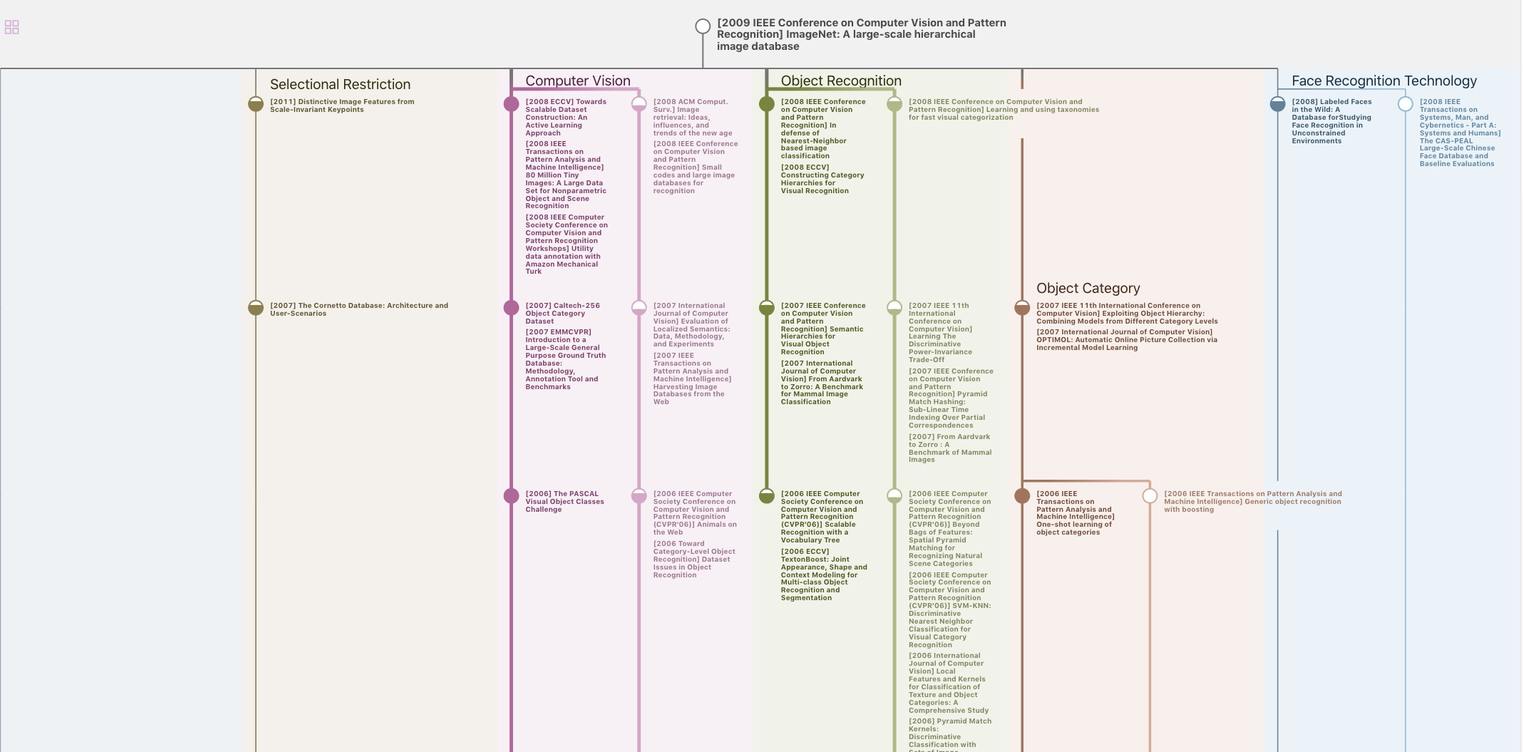
生成溯源树,研究论文发展脉络
Chat Paper
正在生成论文摘要