Prediction of high cycle fatigue strength for additive manufactured metals by defects incorporated crystal plasticity modeling
Materials Science and Engineering: A(2023)
摘要
The durability assessment of additive manufacturing (AM) components is an open issue due to the large scatter in their high cycle fatigue performance. The intrinsic defects inherited from AM processes, especially the irregular defects, pose great challenge to numerical modeling of AM metals and prediction of their fatigue behavior. In this paper, a computational method is proposed to predict the high cycle fatigue (HCF) properties of AlSi10Mg alloy fabricated by laser powder bed fusion (LPBF). A virtual laboratory framework including model generation, crystal plasticity calculation and fatigue performance evaluation is established. In the framework, a representative volume element (RVE) model integrating the polycrystal matrix and defects is developed; the defects are reconstructed based on X-ray Computed Tomography (XCT) measurement and then incorporated into the synthetic polycrystal matrix as the second phase; a crystal plasticity (CP) model using a FFT solver is employed to calculate the mechanical response under cyclic loading; finally, the fatigue strength is determined by using the staircase method. The proposed method well predicts the varied fatigue strengths of specimens containing different defects.
更多查看译文
关键词
Laser powder bed fusion,Crystal plasticity modeling,Defects,High cycle fatigue,Virtual laboratory
AI 理解论文
溯源树
样例
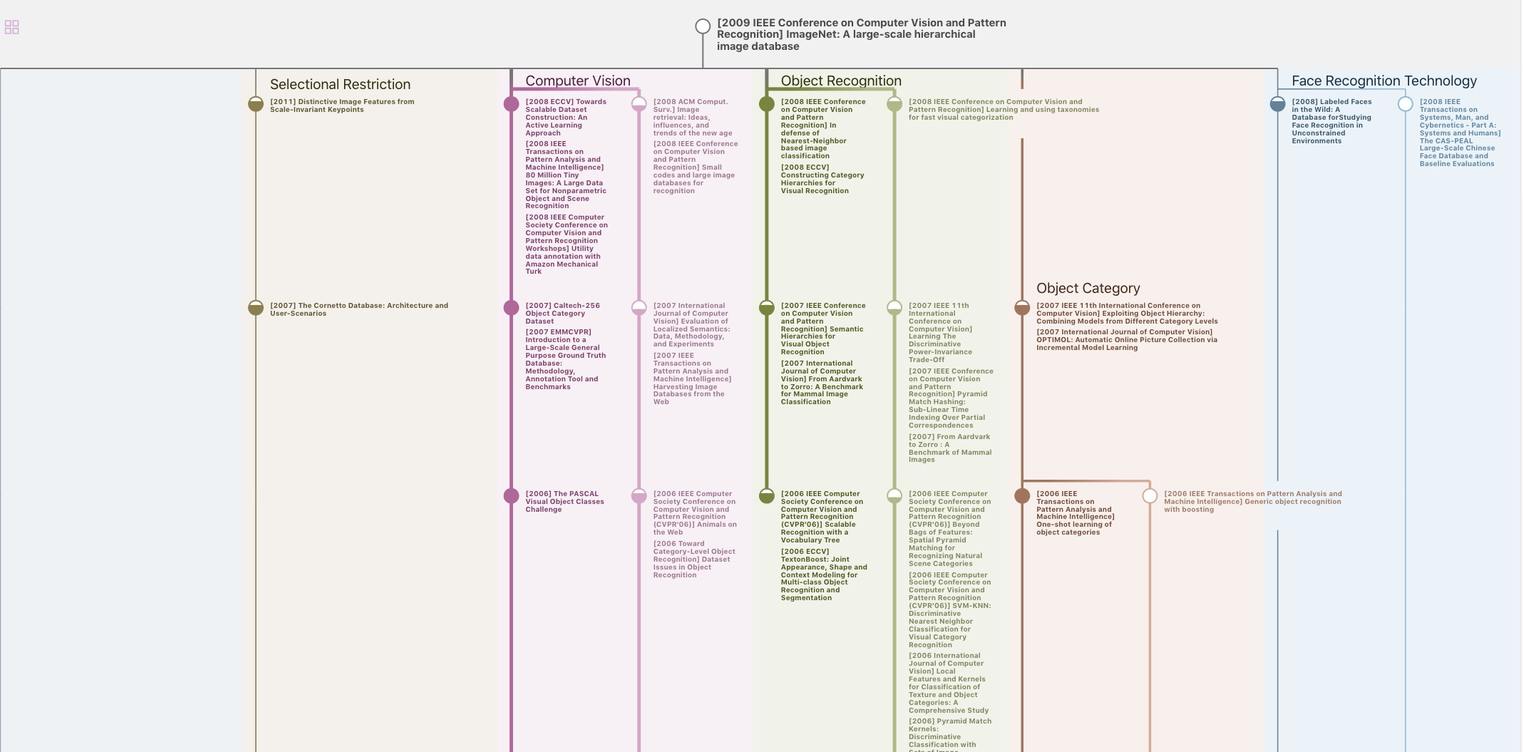
生成溯源树,研究论文发展脉络
Chat Paper
正在生成论文摘要