Predicting axial force in friction stir welding thick 2219 aluminum alloy plate
The International Journal of Advanced Manufacturing Technology(2023)
Abstract
T he advanced heavy-duty launch vehicle fuel tank is made of 2219 aluminum alloy with a thickness of 18 mm now and is welded by friction stir welding (FSW) process. The large thickness results in the axial force in FSW process exceeding 50 kN. The axial force affects the generation of frictional heat and the plastic flow of welding material, which ultimately affects the welding quality. Predicting axial force is the premise of control of the process based on axial force. Most of the existing studies simplify the geometric morphology of the tool during modeling because the complex shape of the tool deforms the mesh excessively and causes the simulation to stop. To achieve the prediction of axial force and investigate the influence of process parameters on axial force, a simulation model of FSW thick 2219 aluminum alloy plate considering the geometric morphology of the tool is established using ABAQUS/CEL based on fluid–structure coupling finite element method. The variation curve of axial force with time during the welding process is obtained, and the validity of the model is verified by FSW experiments. The maximum relative error between the predicted peak axial force and the experimental results is 12.9%, and the average relative error between the predicted axial force and the experimental data in welding stage is 15.1%. Variation law of axial force with rotational speed and welding speed is explored. The research lays a foundation for the control of axial force in FSW thick 2219 aluminum alloy plate.
MoreTranslated text
Key words
FSW,2219 aluminum alloy,Thick plate,ABAQUS/CEL,Axial force
AI Read Science
Must-Reading Tree
Example
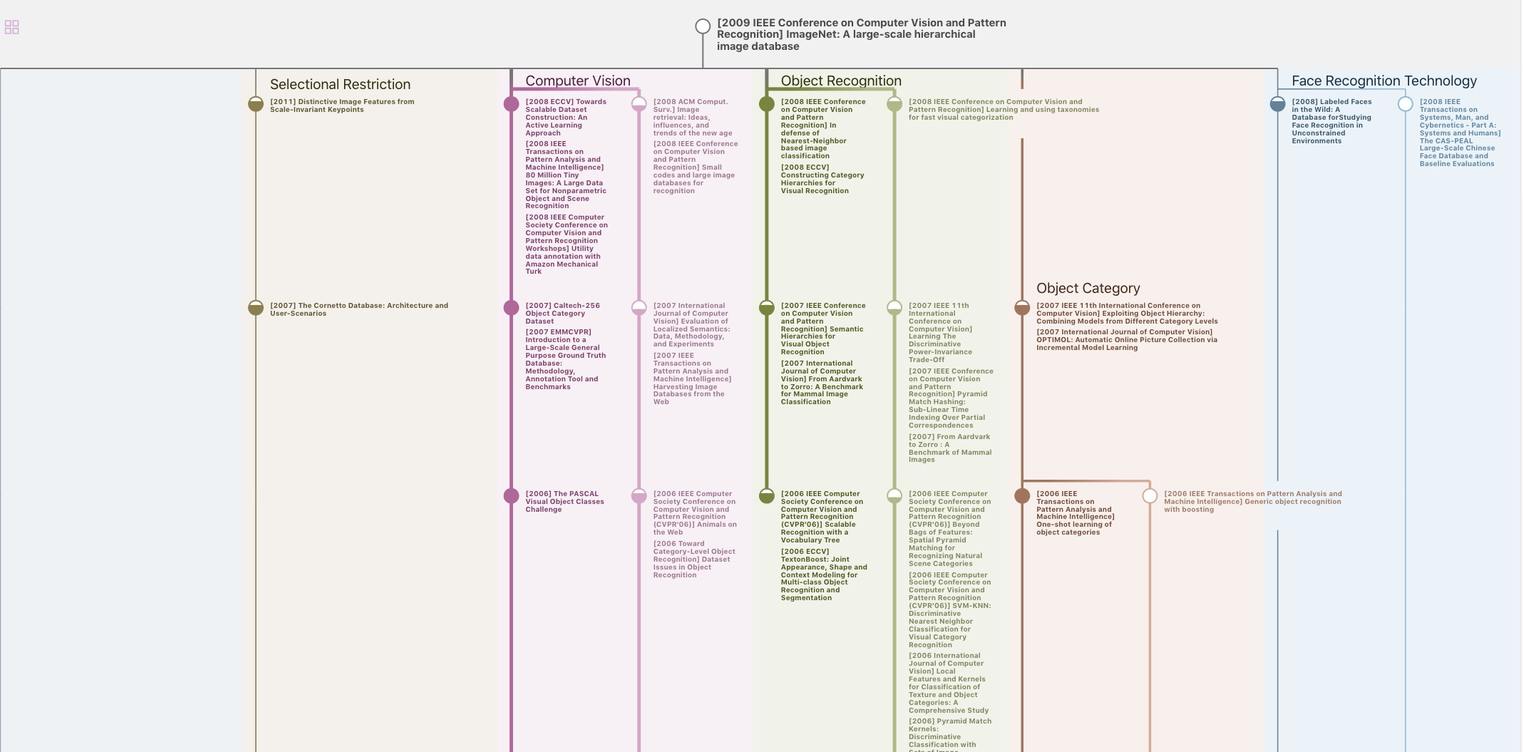
Generate MRT to find the research sequence of this paper
Chat Paper
Summary is being generated by the instructions you defined