Study on damaged micro-mechanism of pipe wall during braking and anchoring process of pipeline intelligent plugging robot
PROCEEDINGS OF THE INSTITUTION OF MECHANICAL ENGINEERS PART E-JOURNAL OF PROCESS MECHANICAL ENGINEERING(2023)
Abstract
Pipeline intelligent plugging robot (PIPR) realizes braking and anchoring through hard contact of slip and pipeline. This process will cause bite marks on the inner wall of the pipeline, which will aggravate corrosion and shorten the service life of the pipeline. Therefore, it is necessary to comprehensively consider slip anchoring performance and degree of pipe -line damage, and optimize slip structure parameters of PIPR, to reduce the damage caused by hard contact between slip and pipeline. Based on force analysis and the hard contact mechanism of PIPR in the course of the anchoring process, the damage factors of pipe walls are analyzed, and a finite element analysis model of slip and pipeline is established. The plastic strain of the inner surface of the pipeline, the plastic strain of slip, and the von Mises stress under three parameters of slip tooth top angle, tooth inclination angle, and tooth number are comprehensively evaluated. In addition, visible indoor tests are established to verify the simulation model. The results show that the optimal tooth structure of slip is tooth top angle theta = 65 degrees, tooth inclination angle gamma = 60 degrees, and tooth number m = 18. This study will provide a reference for the optimal design of the slip of PIPR. It has important engineering significance for the successful implementation of its anchoring operations.
MoreTranslated text
Key words
Pipeline intelligent plugging robot,slip,damage of pipe wall,damage mechanism,structural parameter optimization
AI Read Science
Must-Reading Tree
Example
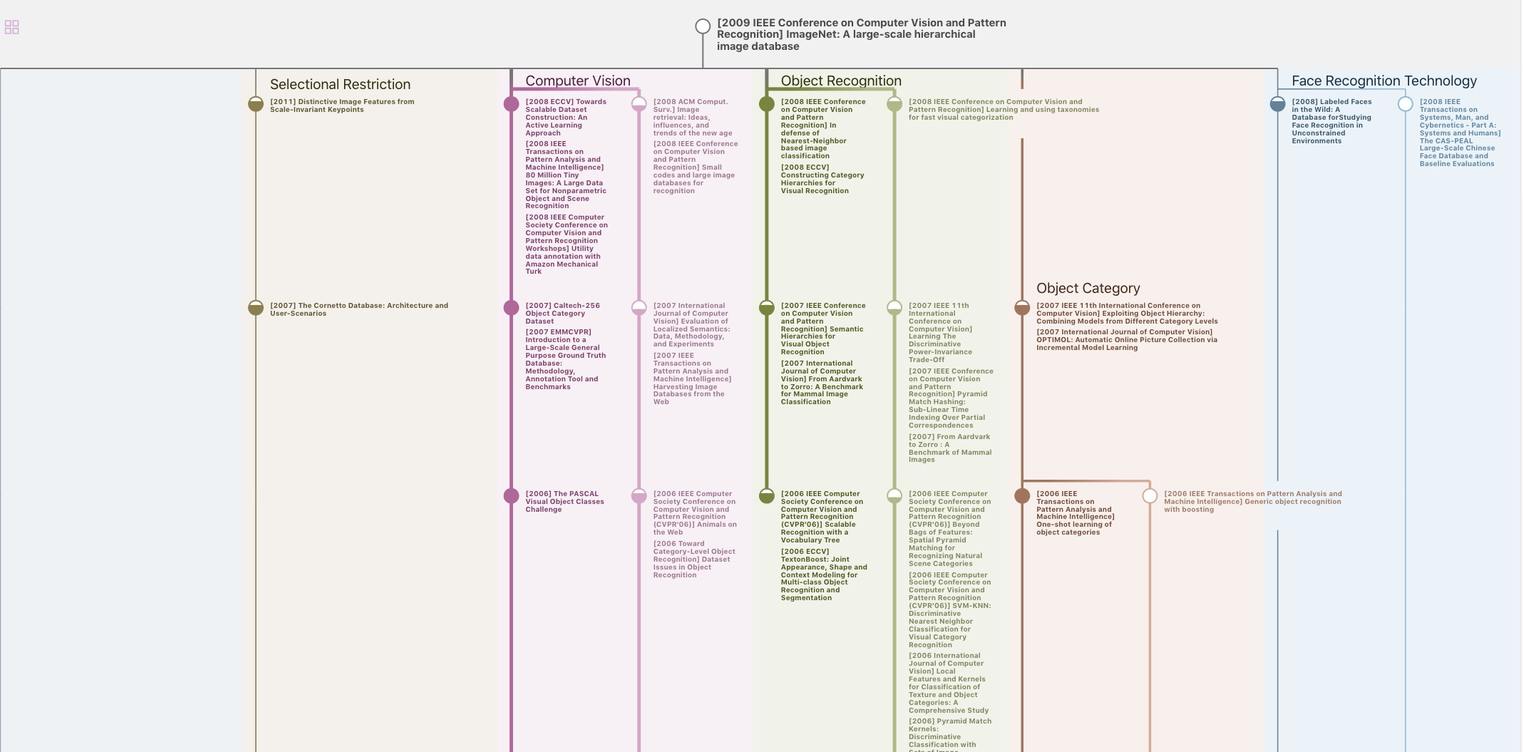
Generate MRT to find the research sequence of this paper
Chat Paper
Summary is being generated by the instructions you defined