Investigation on Ultrasonic Vibration Effects on the Plastic Flow Behavior of Ti2AlNb Alloy: Johnson–Cook Model
Journal of Materials Engineering and Performance(2022)
Abstract
Ultrasonic vibration (UV)-assisted technology has been widely investigated in metal forming in the past decade. However, the research on ultrasonic-assisted forming of Ti2AlNb alloy has not been reported. To study the flow behavior of Ti2AlNb alloy during ultrasonic-assisted forming and set up the constitutive model that can accurately describe its flow behavior, the room temperature compression test of Ti2AlNb alloy with ultrasonic amplitude range of 0-31 µm and strain rate of 0.001-0.125 s −1 were carried out. Considering the influence of yield strength, strain hardening and strain rate hardening effect, a modified Johnson–Cook (J–C) constitutive model is proposed, which can accurately describe the flow behavior of Ti2AlNb alloy during ultrasonic-assisted compression. The results show that under the studied deformation conditions, the yield strength and strain hardening coefficient of Ti2AlNb alloy decrease with the increase of ultrasonic the amplitude. When the amplitude increases to 31 µm. the yield strength decreases by 42%. The ultrasound provides larger dislocation motion energy, increases dislocation activity, and alleviates dislocation stacking, thus reduce the yield strength. The strain hardening exponent and strain rate hardening coefficient increase with the increase of amplitude. The results, obtained from the quantitative analysis of the optimized J–C model, show that the prediction results are in good agreement with the experimental data.
MoreTranslated text
Key words
acoustic softening,constitutive model,Ti2AlNb alloy,ultrasonic vibration
AI Read Science
Must-Reading Tree
Example
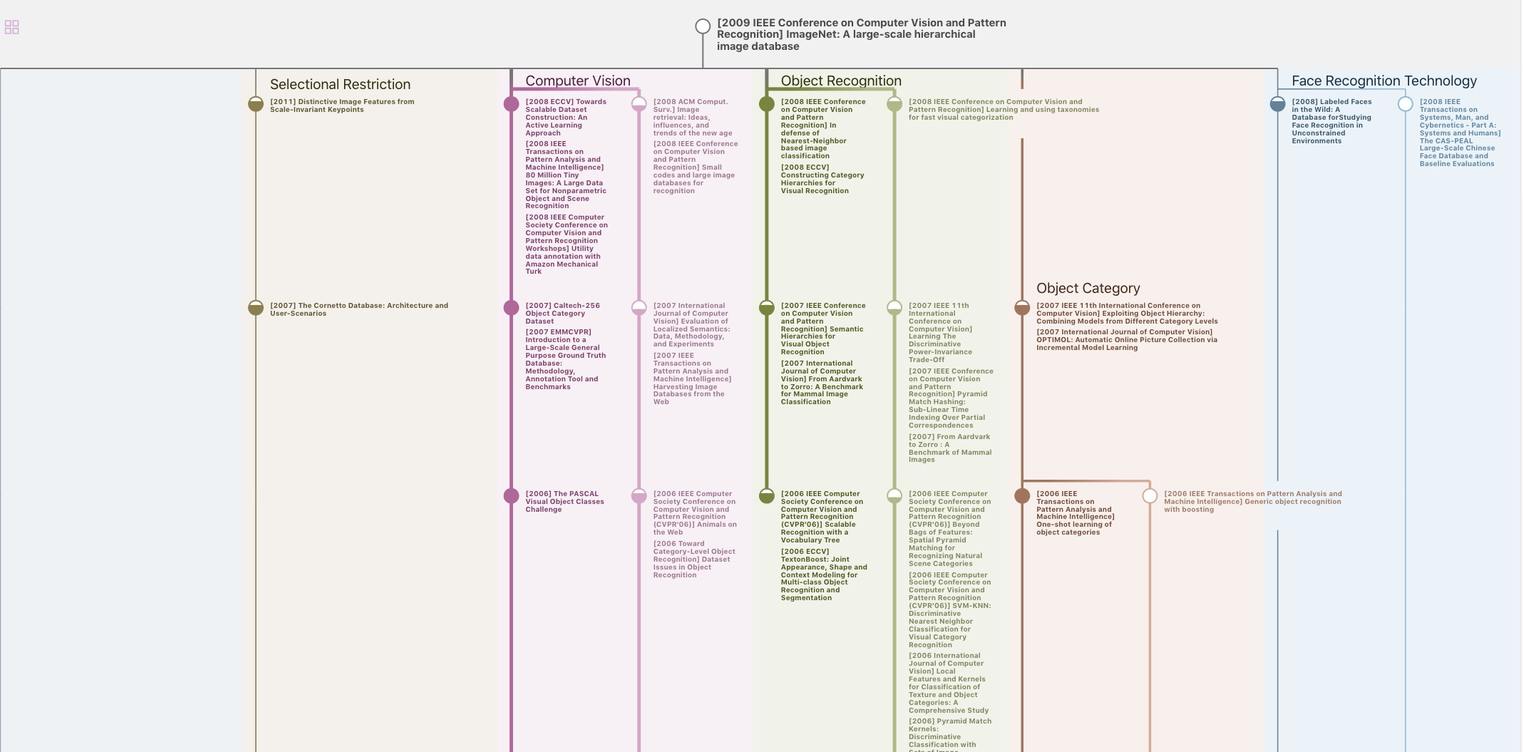
Generate MRT to find the research sequence of this paper
Chat Paper
Summary is being generated by the instructions you defined