Static numerical simulation of radial deformation of ultra-thin dicing blade
PROCEEDINGS OF THE INSTITUTION OF MECHANICAL ENGINEERS PART B-JOURNAL OF ENGINEERING MANUFACTURE(2024)
摘要
Grinding with dicing blade is an important method to cut or slot electronic and optical devices. The deformation of grinding tools will definitely affect the processing of workpiece. However, this effect has been disregarded during processing. In order to improve the machining accuracy in the precision grinding method, this deformation is worth considering. In this research, the grinding state of the ultra-thin dicing blade was simplified as a static problem. The force model of the ultra-thin dicing blade during grinding was established, which centrifugal force was adopted in the whole blade and triangular distribution grinding forces were adopted in the grinding area. The radial deformation of the ultra-thin dicing blade was determined by finite element simulation, and the influence of grinding parameters on its radial deformation was analyzed. The simulation results showed that the grinding area of the ultra-thin dicing blade occurred radial expansion deformation at high rotational speed (more than 8000 rpm), and the value could reach 1.75 mu m (rotational speed at 23,000 rpm, feed speed at 600 mm/min, and grinding depth at 0.12 mm). The deformation increased in a form of power function with the increase of rotational speed, and decreased linearly with the increase of feed speed and grinding depth. This work can provide reference data for deformation compensation, which is helpful to improve the dimensional accuracy of grinding groove.
更多查看译文
关键词
Ultra-thin dicing blade,force model,grinding parameters,deformation,finite element
AI 理解论文
溯源树
样例
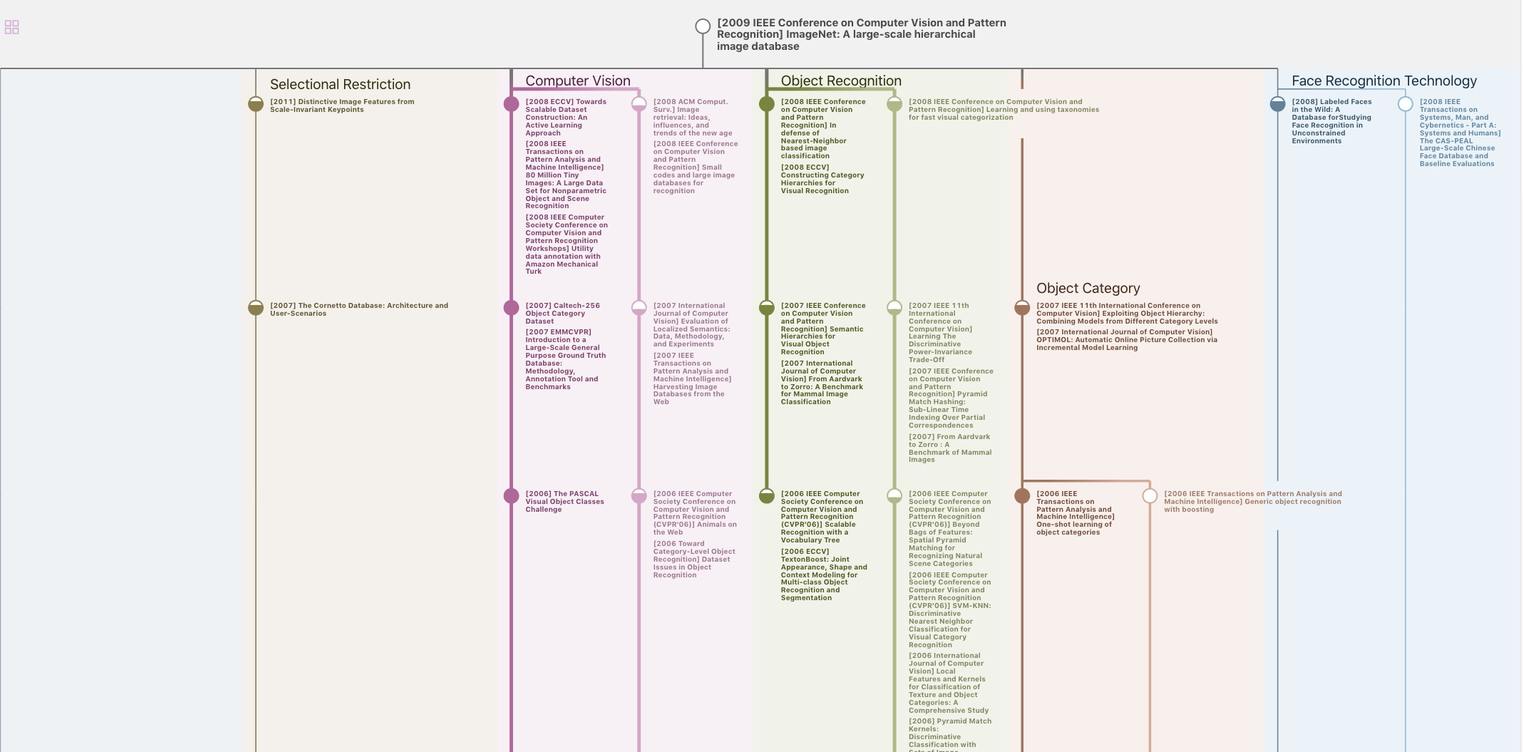
生成溯源树,研究论文发展脉络
Chat Paper
正在生成论文摘要