Experimental investigation on additive manufactured single and curved double layered microchannel heat sink with nanofluids
HEAT AND MASS TRANSFER(2023)
摘要
For the latest high density compact devices, thermal management is crucial for their effective heat dissipation and system reliability. In literature, microchannel heat sink has been established as one of the advanced heat transfer techniques to fulfill the cooling demands of high power electronic applications. However, maldistribution in microchannels causes flow induced high temperature zones (FITZ) which reduces the electrical performance owing to electrical-thermal instability of the integrated chips. One way to mitigate the FITZ is by allowing more coolant inlets in these zones. In the current study, this is achieved by redesigning double layer microchannel heat sink (DMCHS) specific to the FITZ of I-type microchannel configuration using additive manufacturing (AM). Two AM microchannels were tested, one is a single layer microchannel heat sink (MCHS) and another one is a curved double layer microchannel (C-DMCHS). The curved channels were introduced in the bottom channels of C-DMCHS to mitigate FITZ compared to conventional DMCHS. AM microchannels are compared for Nusselt number and friction factor characteristics with the conventional straight channels, and heat treated AM microchannels. From experimental observation, Ti64 3D printed microchannel with Graphene oxide (GO-0.12%) nanofluid developed 75.4% more pressure drop than the Ti64 heat treated microchannel. The results additionally show that the C-DMCHS delivered 26.5% lower FITZ temperature than MCHS.
更多查看译文
关键词
nanofluids
AI 理解论文
溯源树
样例
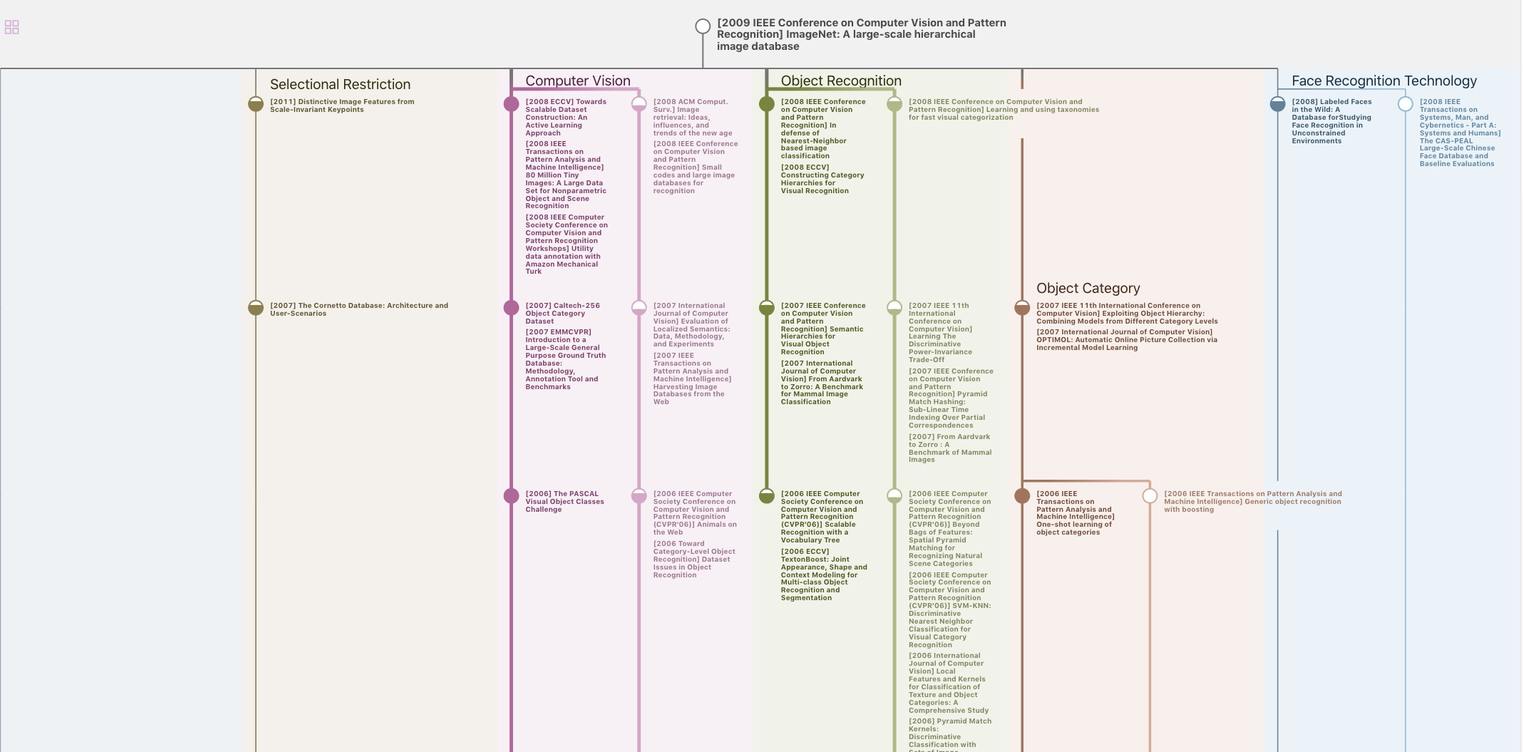
生成溯源树,研究论文发展脉络
Chat Paper
正在生成论文摘要