Numerical Simulation of the Laser Welding Process for Electrical Steel Laminations
2022 12th International Electric Drives Production Conference (EDPC)(2022)
摘要
Soft magnetic cores in electric machines conduct and enhance the magnetic flux. The magnetic properties of the single sheets are mainly influenced by the alloying elements, the microstructure and the rolling and annealing process. To reduce eddy current losses during operation, soft magnetic cores are laminated. However, all manufacturing processes and the further assembling steps, like mounting of the stator, change the magnetic properties of the stack. Laser welding is a common method for producing lamination stacks, as very thin sheets can be welded automatically with high velocities. However, the weld seams are electrically conductive connections, which lead to an increase in eddy current losses. Furthermore, the microstructure in the heat-affected zone is impaired, which leads to a higher demand for magnetization and increased hysteresis losses. A main reason for this is the magneto-mechanical effect, as mechanical stresses influence the magnetic properties. For improvement, the process parameters must be adapted to the specific material system and the requirements. In this paper, a numerical simulation model for visualizing and optimizing the heat distribution in welded electrical steel laminations is presented. The main objective is the analysis of the weld dimension for different welding parameters. For this purpose, a transient thermal analysis is carried out with Ansys Workbench. The welding process is mapped in a simplified way with a moving heat source for different conditions. To validate the results, a comparison to experimental tests is applied. In this way, the simulation results are verified and potential sources of errors are identified.
更多查看译文
关键词
Electrical steel,Finite element analysis,Joining processes,Magnetic losses,Soft magnetic materials
AI 理解论文
溯源树
样例
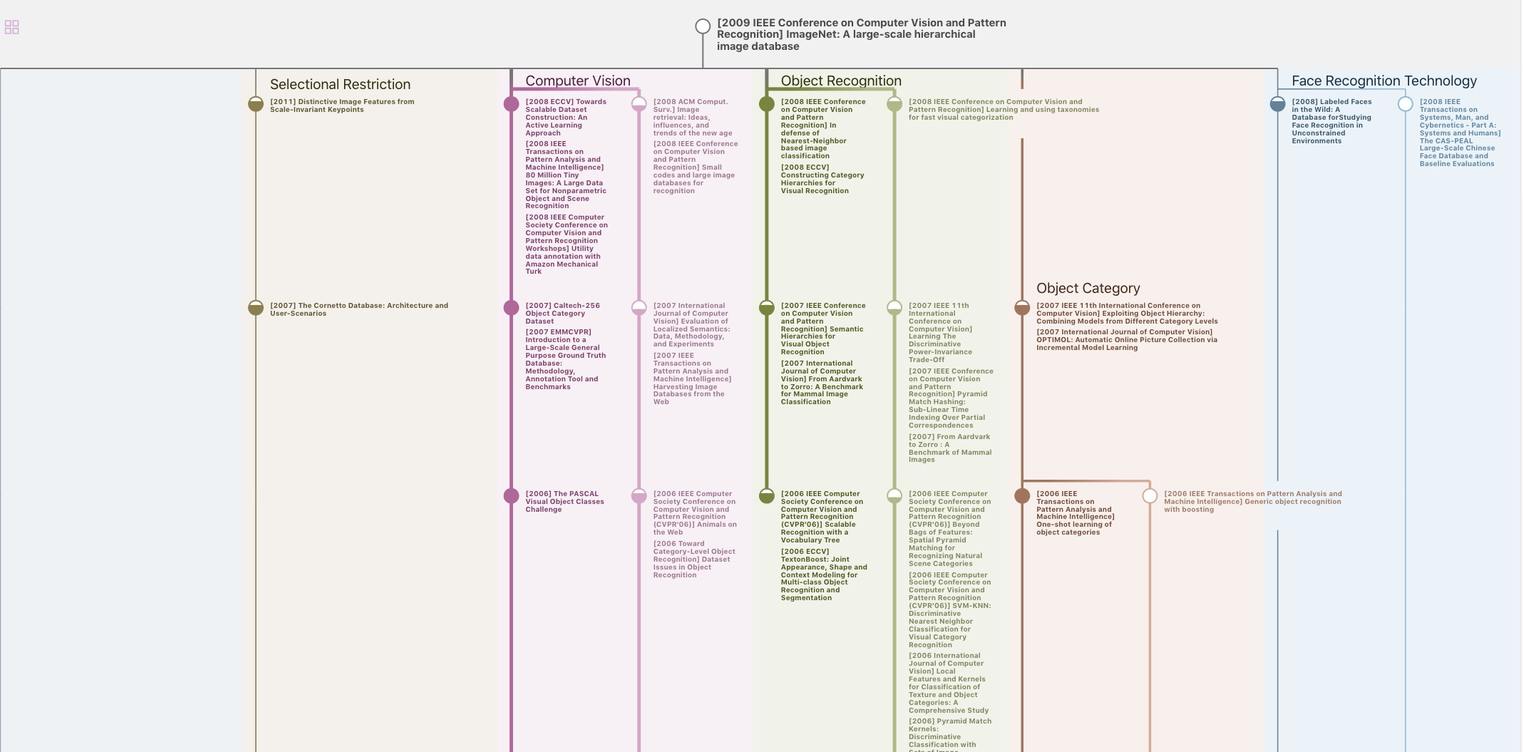
生成溯源树,研究论文发展脉络
Chat Paper
正在生成论文摘要