Machining error prediction scheme aided smart fixture development in machining of a Ti6Al4V slender part
PROCEEDINGS OF THE INSTITUTION OF MECHANICAL ENGINEERS PART B-JOURNAL OF ENGINEERING MANUFACTURE(2023)
摘要
Machining of slender (low rigidity) parts is associated with tool/workpiece deflections due to induced cutting forces resulting in machining error (dimensional inaccuracy of the machined surface). The development of smart fixtures is seen as an enabler for reduction of machining error. To reduce lead times, the smart fixtures need to be designed in an efficient way by using more virtual simulations and less physical iterations. This paper presents the development of a novel methodology for machining error prediction in milling of a fixture-workpiece system. The methodology integrates a cutting force model, a finite element based fixture-workpiece system and a multi-step error predictive approach. The methodology was first validated on a flexible thin-wall Ti6Al4V slender part where less than 6% difference was achieved between predicted and measured machining error. The difference between predicted and measured cutting forces was approximately 6%. After the gained confidence, the methodology was applied to the flexible thin-wall Ti6Al4V slender part encompassed by a fixture with three actuators acting as supports. The predicted machining error was reduced from the range of 0.2-0.33 mm (no actuators) to the range of 0.12-0.14 mm (with three actuators). This demonstrated the capability of the developed methodology to aid the design of future smart fixtures with the potential to reduce lead times during their development.
更多查看译文
关键词
Machining,fixture-workpiece system,error prediction,modelling and simulation
AI 理解论文
溯源树
样例
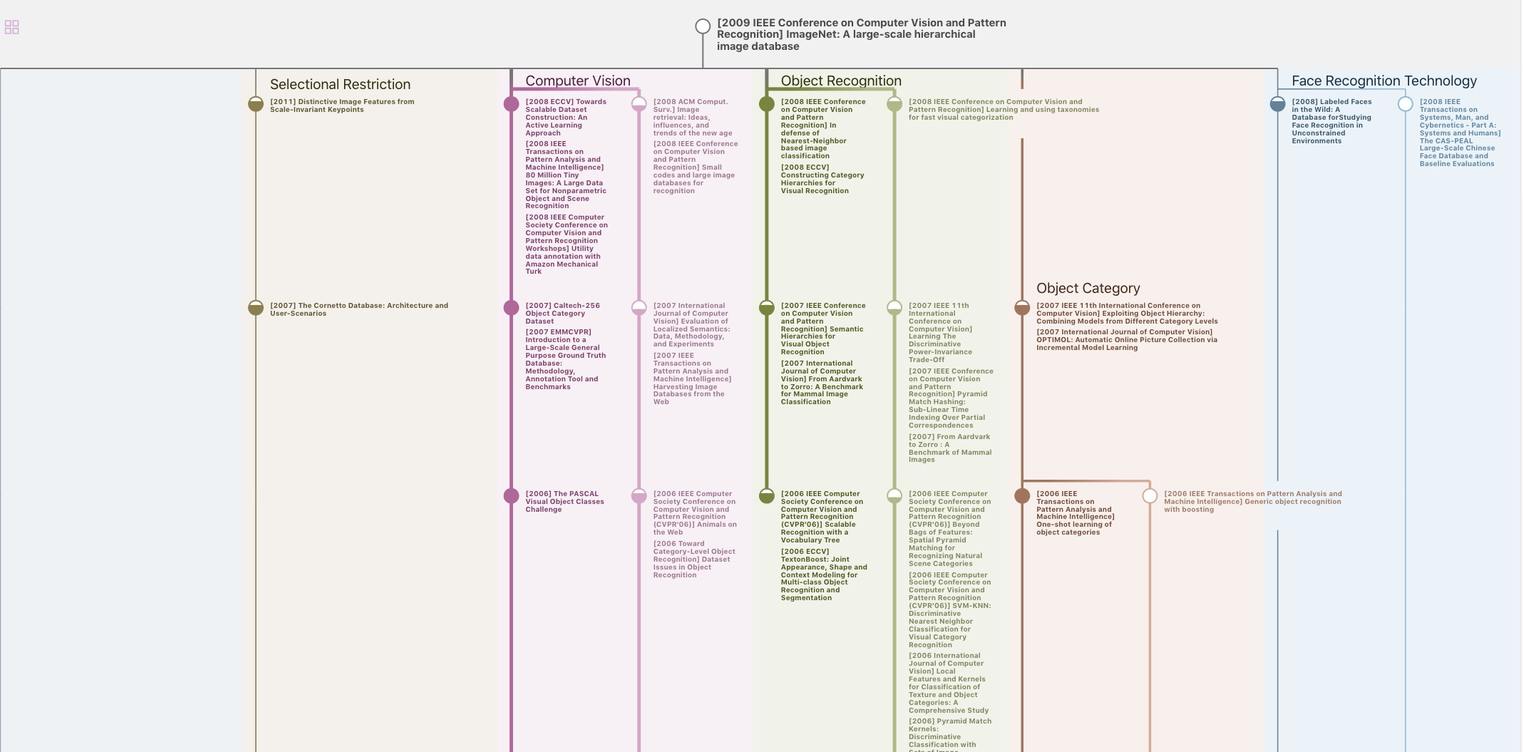
生成溯源树,研究论文发展脉络
Chat Paper
正在生成论文摘要