Residual Heat Effect on the Melt Pool Geometry during the Laser Powder Bed Fusion Process
JOURNAL OF MANUFACTURING AND MATERIALS PROCESSING(2022)
摘要
The continuous back-and-forth melting of the powder bed during the laser powder bed fusion (LPBF) process leads to the development of residual heat, which affects the melt pool geometry as the laser scan progresses. The magnitude of the residual heat depends on the scan length, hatch spacing, location on the track, etc. In this regard, back-and-forth raster scanning was performed to investigate the effect of the scan length and hatch spacing on the melt pool size at different locations along the laser travel direction. Multi-track specimens with different scan lengths (0.5 mm, 1 mm, and 1.5 mm) were fabricated using 195 W laser power, three scan speeds (375 mm/s, 750 mm/s, and 1500 mm/s), and two hatch spacings (80 mu m and 120 mu m). A white light interferometer was used to analyze the surface morphologies of the fabricated samples, and metallography was performed to observe the melt pool boundary. The melt pool boundary obtained at different locations revealed that the effect of the residual heat was maximal in the laser-turn region. In addition, a powder scale numerical model was developed to investigate the effect of temperature distribution on the melt pool geometry. The numerical results show that the laser-turn region was most affected by the residual heat, as the melt pool from the two tracks merged. The depth of the melt pool increased with increasing track numbers, while the track height decreased. The addition of a second layer of powder showed that the inherent surface variation in the first layer leads to the difference in the actual layer thickness of the second layer.
更多查看译文
关键词
additive manufacturing, laser powder bed fusion, porosity, numerical modelling, melt pool
AI 理解论文
溯源树
样例
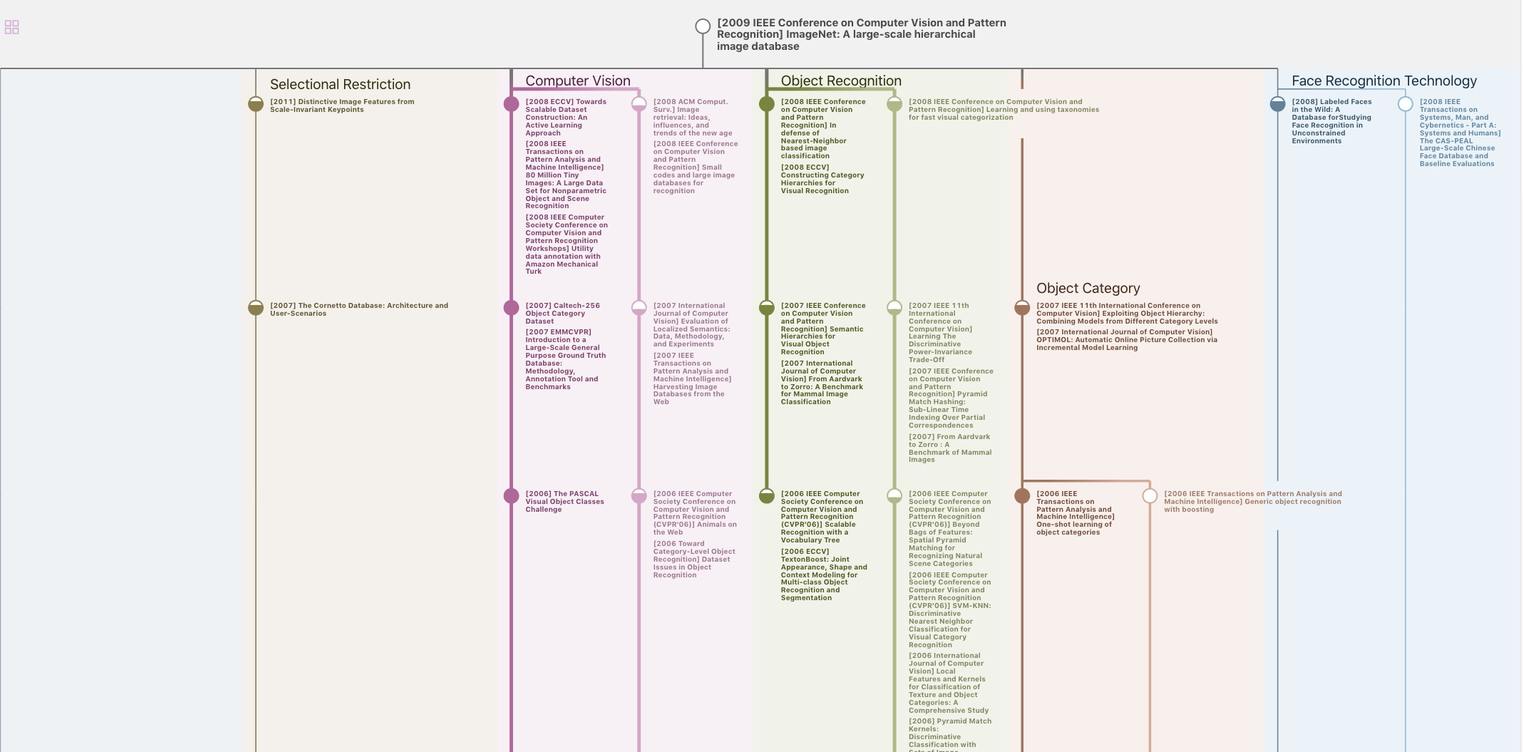
生成溯源树,研究论文发展脉络
Chat Paper
正在生成论文摘要