Implementing lean manufacturing for improvement of operational performance in a labeling and packaging plant: A case study in Bangladesh
Results in Engineering(2023)
摘要
Under the given intensified competition in real-world markets and increased customer requirements, manufacturers are subjected to adopt value-added techniques in their manufacturing management. This study aims to apply a lean manufacturing approach via value stream mapping (VSM) in a labeling and packaging company in Bangladesh for the improvement of the overall performance of the organization and generalize it for similar companies. Activities such as identifying the current state of problems, reviewing the applicability of the lean system and VSM, locating both value-added and non-value-added activities, experimentation based on new parameters, and analyzing data for improvement have been done. The key performance indicators (KPI) included are reduction of lead time and customer complaint rate (CCR), increasing units produced per labor hour (UPLH), and utilized equipment effectiveness (UEE) to analyze productivity enhancement in different processes. It shows that proper applications VSM, Kanban, setup time reduction single-minute-exchange-of-die (SMED) approach and why-why analysis can bring about significant improvement in KPIs. By using these approaches waiting time is reduced by designing a new kanban die rack, motion waste is reduced by designing a new finishing line setup, and production defects are reduced by implementing a novel color sticker technique. Therefore, it can be said that the production process assisted by lean manufacturing improves the lead-time, ICR, and CCR by 7.1%, 55%, and 83%, respectively, which indicates better production with optimum quality and lesser waste. This study makes numerous contributions to the labeling and packaging industry for productivity and quality improvement.
更多查看译文
关键词
Lean manufacturing,Value stream mapping,Key performance indicators,Customer complaint rate,Internal complaint rate,Utilized equipment efficiency,Unit produced per labor hour,Lead time
AI 理解论文
溯源树
样例
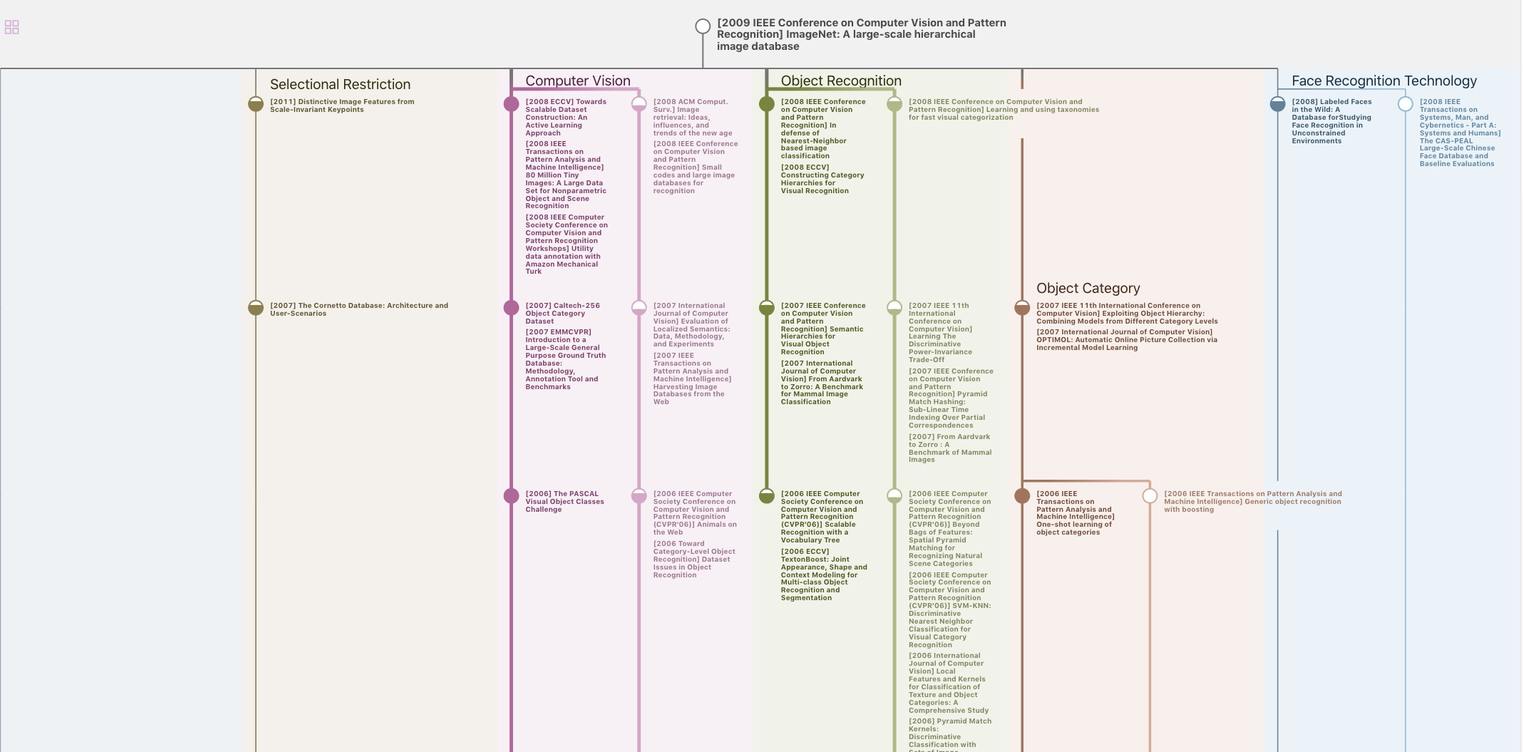
生成溯源树,研究论文发展脉络
Chat Paper
正在生成论文摘要