Initial Experimental and Analytical Efforts to Predict Sustained Load Crack Growth During a Hydrotest and Subsequent Fatigue Crack Growth During Pressure Cycling
Volume 2: Pipeline and Facilities Integrity(2022)
Abstract
Abstract Significant efforts were undertaken to develop experimental data to assess the effect of sustained load crack growth during a simulated hydrotest and the effect on fatigue crack growth during subsequent pressure cycling service operation. The pipe used was a 1960ERW 16-inch diameter by 0.250-inch thick X46 pipe. There were a variety of laboratory specimen tests including: standard and isochronous tensile tests at various rates, Charpy transition curves, C(T) J-R curve tests, and SENT J-R curve tests. There were axially surface-cracked pipe tests with monotonically increasing pressure to failure, as well as step-hold pressure tests. Cracks were put in the base metal as well as the ERW seam weld. Some key results to be shown are: 1. The fracture toughness of the base metal and ERW HAZ varies with a/t of the flaw in the SENT testing. Larger a/t specimens have lower toughness. It is believed that this behavior is a key aspect in leak-before-break behavior under pressure loading. 2. Slow strain rate tensile test showed that the yield point decreases with slower loading rates, but the strain-hardening exponent remained relatively constant. The drop in the stress-strain curve causes an increase in the crack-driving force, which is why crack growth can occur with sustained loading. 3. Step-hold pressurized pipe tests with axial surface cracks were conducted with a great amount of data and refined crack growth measurements. In one pipe test, there were four identical flaws. One flaw failed by leakage during a long hold-time. It could be patched, and the other three “identical” flaws all had some small (but different) amounts of ductile tearing. On subsequent pressure cycling, the crack growth rate was incredibly lower than standard fatigue crack growth rates. This was due to the crack retardation effect from the small ductile tear and crack-tip plasticity, with the reverse crack-tip compressive plasticity from unloading after the simulated hydrotest. The fatigue crack growth rates were about 2 to 3 orders of magnitude slower. The crack retardation benefit easily overcame the small loss in the ligament from ductile tearing. Instead of failure being about 11,300 cycles it took 267,400 cycles. This is a huge benefit for liquid lines. A subsequent follow-on program to this is being undertaken by DOT/PHMSA to better characterize the crack retardation effect and also develop a methodology to predict the “Rupture Free Operational Time” after hydrotest.
MoreTranslated text
AI Read Science
Must-Reading Tree
Example
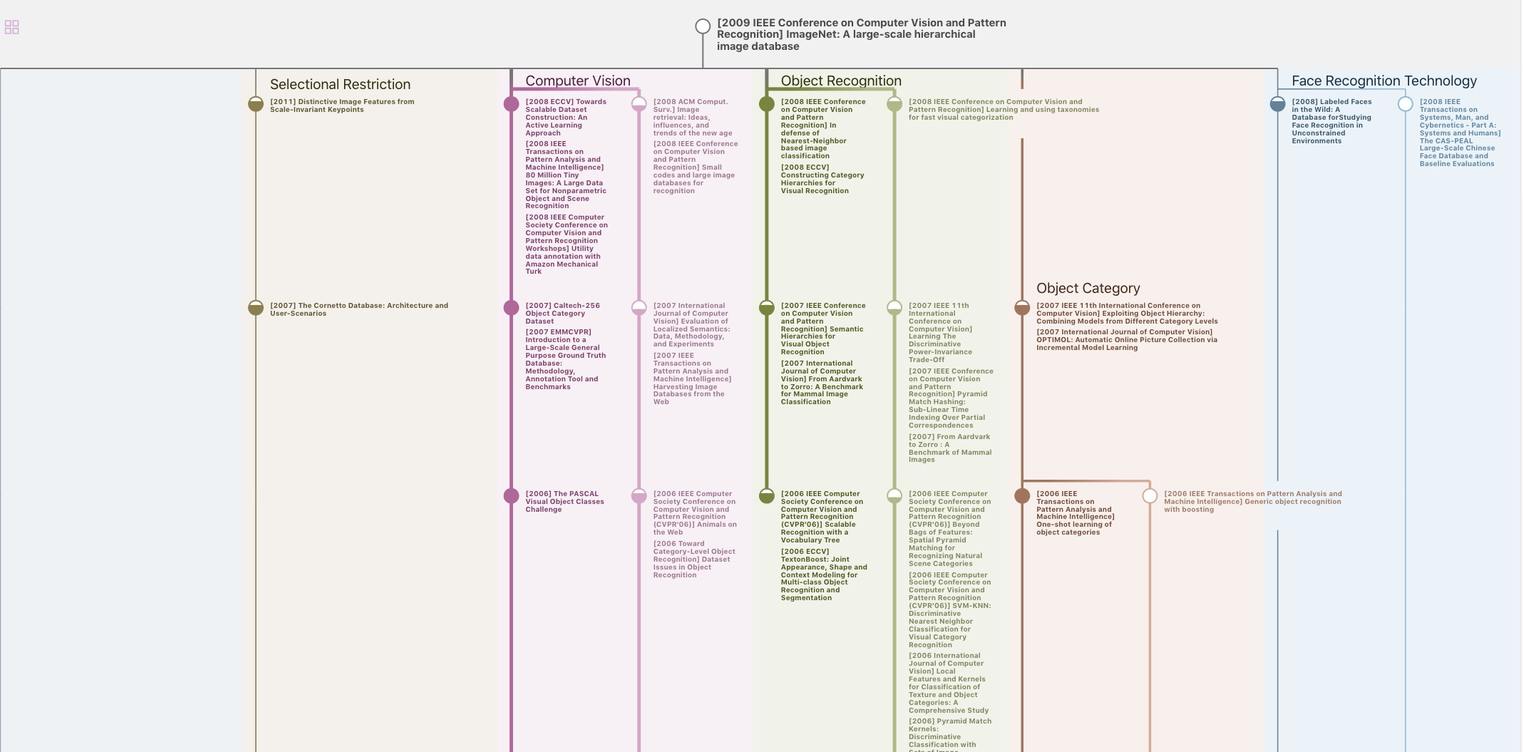
Generate MRT to find the research sequence of this paper
Chat Paper
Summary is being generated by the instructions you defined