Double diaphragm forming simulation for net-shape component using multi-layered biaxial non-crimp fabrics
Journal of Physics: Conference Series(2022)
摘要
Compared to autoclave-cured prepreg, liquid composite moulding (LCM) is a cost-effective alternative to produce advanced composites, thanks to the less-expensive intermediate materials, lower capital investment and shorter cycle time. A separate preforming step is typically required within the process chain to convert 2D fabric blanks into complex 3D geometries before moulding. Numerical models are therefore important to ensure near net-shape preforms during the design phase, in order to minimise the material wastage related to preforming. In this study, a microscale finite element (FE) model was employed to assist in determining the ply shape of multi-ply biaxial non-crimp fabrics (NCF) to achieve net-shape preforms made by double diaphragm forming (DDF) using a spar-like geometry. The forming deformation of the NCF was predicted by simulations considering the in-plane stiffness of the NCF. The location of wrinkles was indicated by the simulation using membrane elements. By continuously removing the redundant fabric material making contact with the machine bed and tool surface, net-shape preforms were achieved for the target geometry using single and multiple NCF plies respectively. Compared with the original ply shape, the number of wrinkles was reduced for the net-shape case due to the reduction in the bridging force induced by the contact pairing between fabric-diaphragm assembly and the machine bed.
更多查看译文
AI 理解论文
溯源树
样例
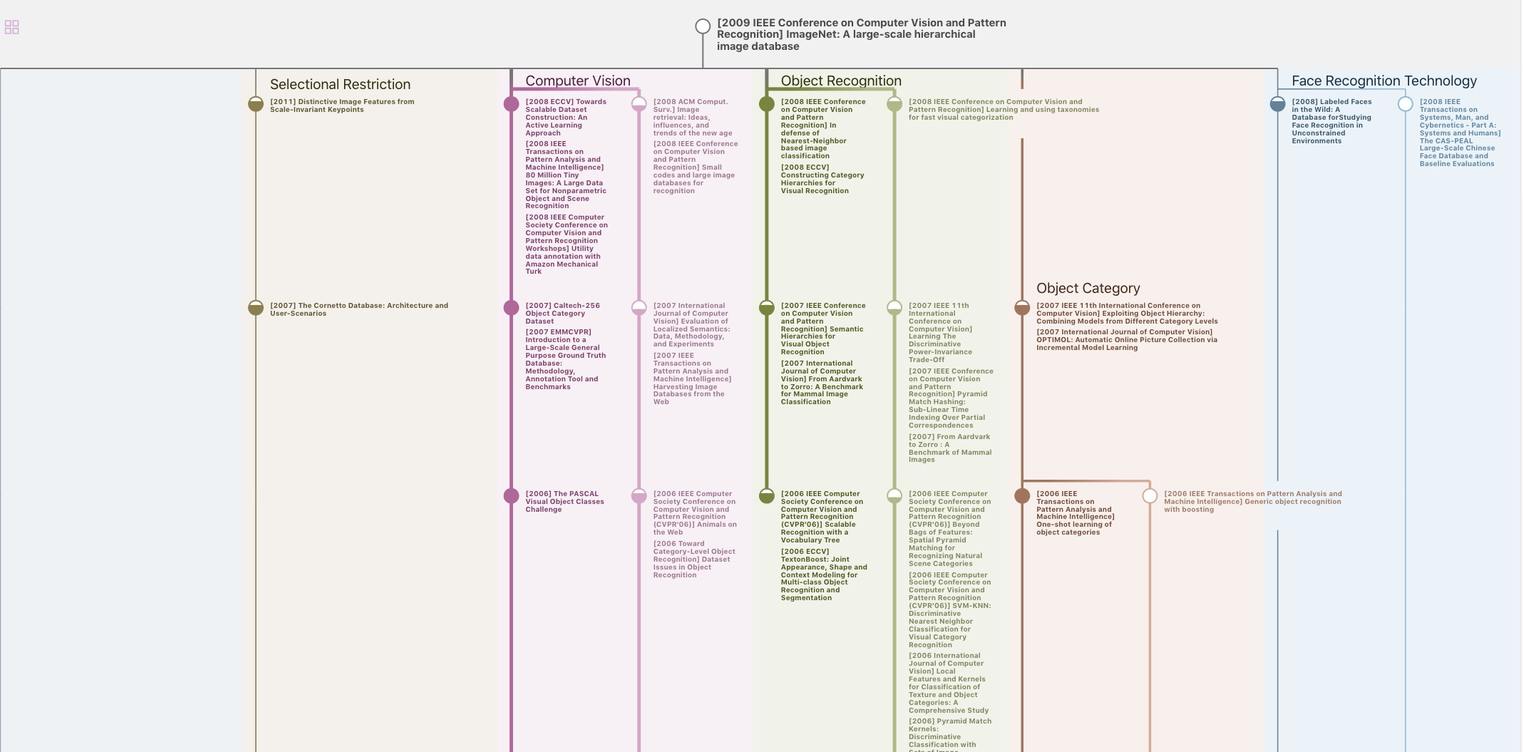
生成溯源树,研究论文发展脉络
Chat Paper
正在生成论文摘要