(Digital Presentation) Photonic Curing of Hybrid Transparent Electrodes for High-Throughput Solar Cell Manufacturing
ECS Meeting Abstracts(2022)
Abstract
Realizing high-throughput, low-cost perovskite solar cell (PSC) manufacturing is highly sought-after in photovoltaic research in recent years. PSCs can be fabricated using inexpensive and scalable solution-deposition methods, such as slot-die coating, blade coating, or spray coating, that can be performed in open air or under inert gas conditions and are compatible with high-throughput, roll-to-roll (R2R) manufacturing. To fully achieve R2R manufacturing of PSCs, it is important to also consider the flexible transparent electrode (TE). PET/ITO is a commonly used substrate for making flexible PSCs. When optimizing transparent conducting materials, there is a tradeoff between sheet resistance (Rsh) and optical transparency. PET/ITO substrates with high Rsh have high transparency and smoother ITO surfaces, compared to PET/ITO substrates with low Rsh, which have low transparency and higher surface roughness, indicating thicker ITO films. ITO is brittle and tends to crack under mechanical stress or bending, which is further exacerbated when using a thicker ITO layer. It is desired to have a thin ITO film with low Rsh, high optical transparency, and smooth surface roughness. Because commercial PET/ITO substrates are made with slow (~1 m/min) vacuum deposition processes, they tend to be expensive. Therefore, it would be advantageous to develop a high-throughput, R2R compatible, solution-deposition approach for fabricating the TE on PET substrates. To achieve this, two key processes must be developed: A solution-deposition process that enables uniform coating of the TE on PET and a post-deposition annealing process that is compatible with the low-temperature PET and high speed of R2R manufacturing. While various solution-deposition processes, such as those listed above, can achieve the desired web speed of > 30 m/min, there is still a need to improve the post-deposition annealing step. One promising post-deposition processing technique is intense-pulsed-light processing, also known as photonic curing. Photonic curing delivers short (0.01 – 100 ms) pulses of broadband (200 – 1500 nm) light from a xenon flash lamp to the samples. Any materials in the sample stack that absorb light will convert the impinging light pulse into heat within the sample, which drives changes in the sample (calcination, phase change, crystallization, etc.). Photonic curing has three main advantages over thermal annealing: 1. Faster processing speed (milliseconds or seconds). 2. Compatibility with plastic substrates. 3. Smaller physical footprint and less wasted energy. Since the light pulses are on for a short time, the intensity can be high while the total energy delivered to the sample is low. During the photonic curing process, the absorbed light causes the TE precursor film to selectively and quickly (microseconds – milliseconds) heat up, while the PET substrate underneath heats up less and slower (seconds). Because the thin film is a few orders-of-magnitude thinner than the PET substrate, the heat generated and transferred from the thin film does not cause significant substrate heating. This allows high-temperature processing in the top layers of the sample stack, while keeping the bottom plastic substrate temperature low. In this work, a hybrid TE material is fabricated on PET substrates using photonic curing. The hybrid TE material contains a layer of silver nanowires (AgNWs) and a layer of metal-oxide (ITO, IZO, etc.). The AgNWs increase the light absorbed by the film during the photonic curing process, which leads to higher processing temperatures, possibly improving the conversion of the metal-oxide layer. The AgNWs also enhance the electrical conductivity of the final TE layer after photonic curing. A AgNW and metal-oxide bilayer is formed by spin coating each solution onto the PET substrate sequentially followed by a single photonic curing process. We use average optical transmittance (Tavg) from 400 to 700 nm and average Rsh to evaluate the TE performance. The following photonic curing parameters are varied to optimize Tavg (maximize) and Rsh (minimize): Pulse voltage, pulse envelope, number of micro-pulses, duty cycle, number of pulses, and pulse repetition rate. Preliminarily, we also observe a significant impact on the TE properties by the volume of AgNW deposited during the spin coating deposition step. Using dispense volumes of 80 µL and 20 µL, we achieve samples with Tavg = 73%, Rsh = 19 Ω/sq, and roughness = 9 nm, and Tavg = 83%, Rsh = 58 Ω/sq, and roughness = 5.6 nm, respectively, after photonic curing. Fig. 1 a-d shows SEM, AFM, sample schematic, and AFM line-cuts of the photonic cured hybrid TE sample, respectively. Figure 1
MoreTranslated text
AI Read Science
Must-Reading Tree
Example
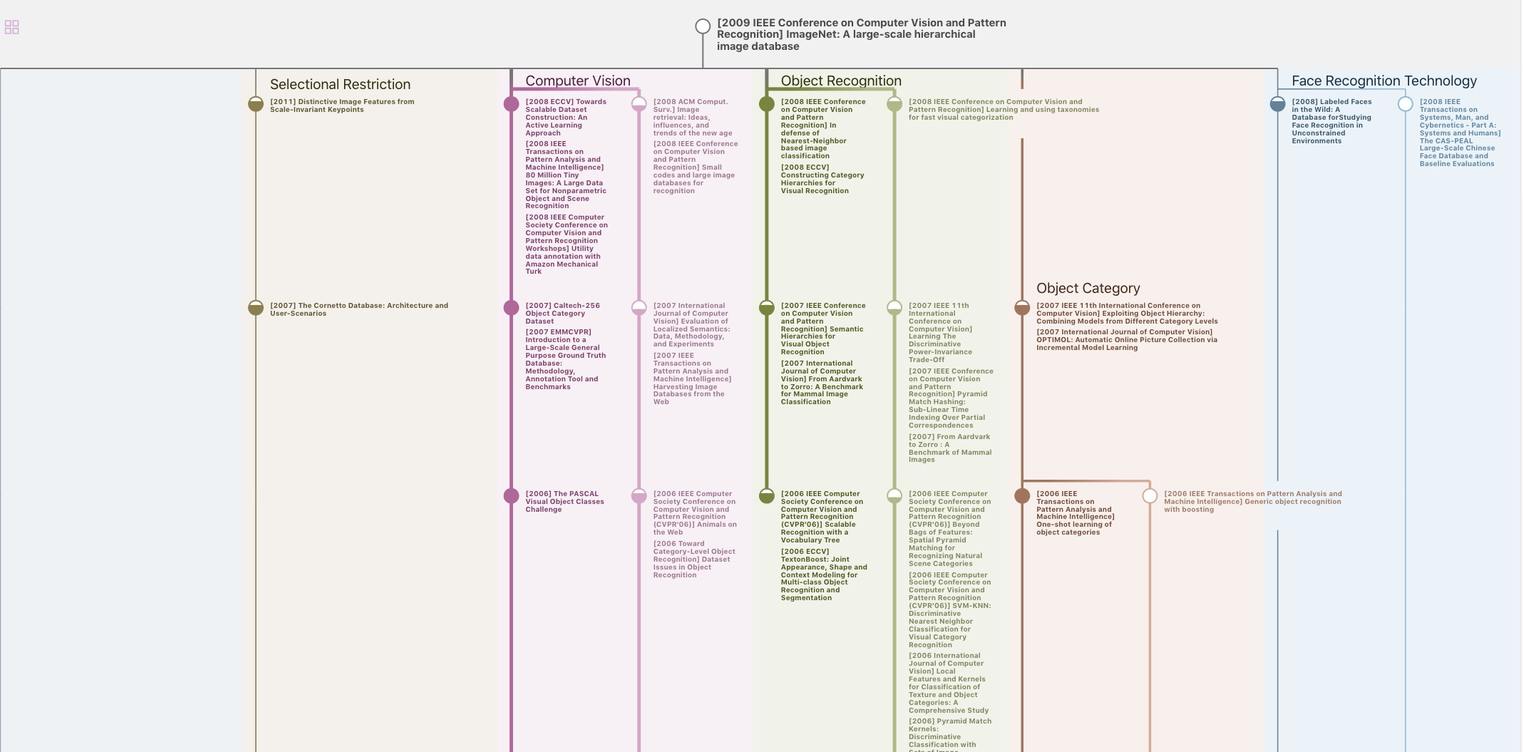
Generate MRT to find the research sequence of this paper
Chat Paper
Summary is being generated by the instructions you defined