Modeling machining of aluminum honeycomb structure
The International Journal of Advanced Manufacturing Technology(2022)
摘要
Aluminum honeycomb structures have been frequently used in many industrial applications, especially in aerospace and aeronautics, due to their high strength and stiffness to weight ratio. The machining quality of aluminum honeycomb structures is generally related to plastic deformation of the walls forming the honeycomb structure and burrs. Consequently, the use of this type of structure requires specific machining operations and special tools. In order to carry out in-depth studies on the milling of aluminum honeycombs, a 3D finite element model was developed with the help of Abaqus/Explicit software. The model thus developed is validated with several experimental tests and for different machining conditions. Based on the developed model, the relationship between the cutting forces and the friction coefficient between the cutting tool and the honeycomb during the cutting process is studied. The main objective of this work is to highlight the effect of physical and geometrical parameters during the milling of aluminum honeycomb structures on cutting forces, surface quality generated, chip size, and material accumulation in front of the cutting tool. The comparison between the simulated results and the experimental results indicates that the developed numerical model is in good agreement with the experimental reality.
更多查看译文
关键词
Finite element modeling,Aluminum honeycomb,Cutting tool geometry,Machined surface quality,Chip size
AI 理解论文
溯源树
样例
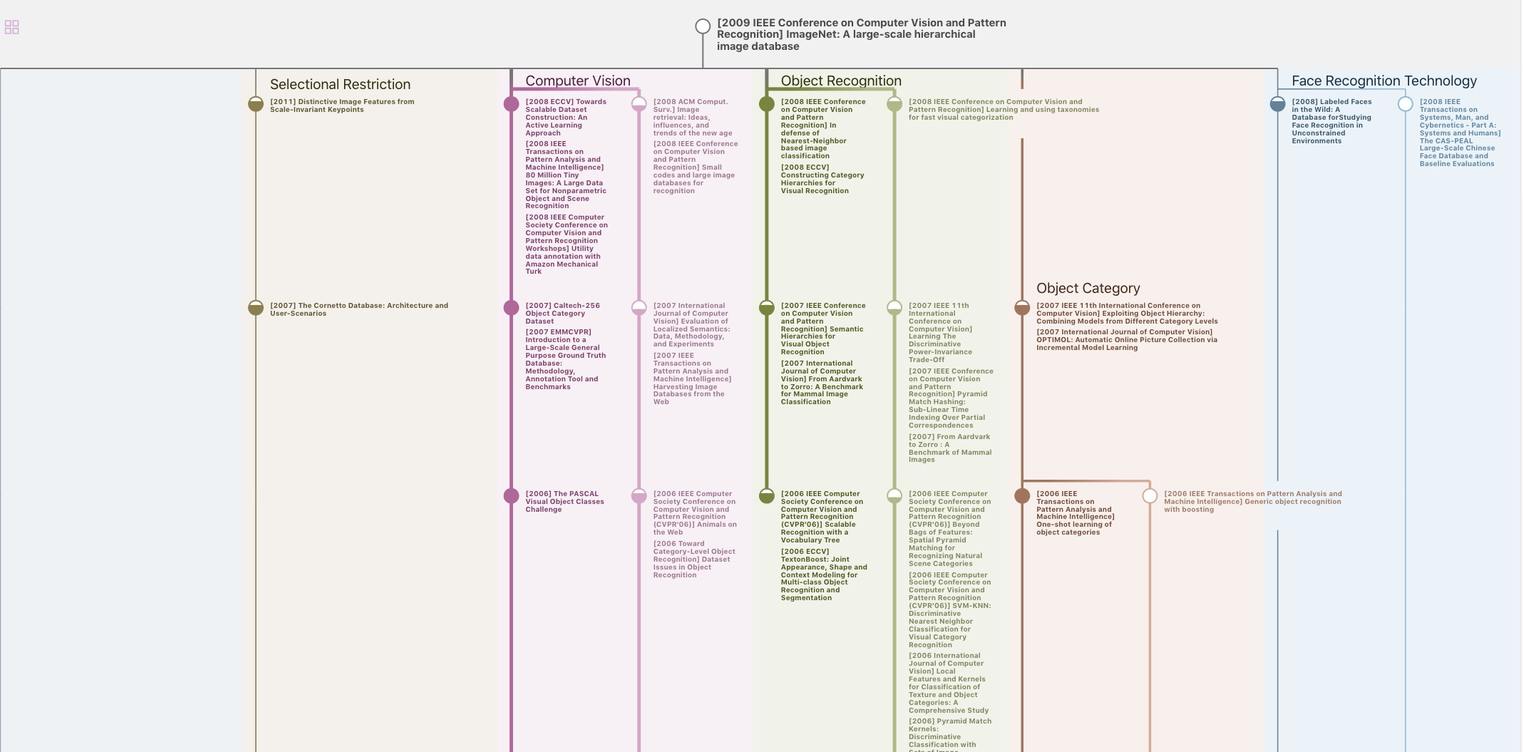
生成溯源树,研究论文发展脉络
Chat Paper
正在生成论文摘要