A semi-active control method for magnetorheological dampers to suppress the milling vibration of thin-walled workpieces
Proceedings of the Institution of Mechanical Engineers, Part C: Journal of Mechanical Engineering Science(2022)
摘要
Thin-walled workpieces are widely used in the aerospace field, and milling is the main processing method of such components. However, thin-walled workpieces are prone to vibrate during milling because of their weak stiffness, and the vibrations significantly affect the processing quality. Therefore, it is important to develop a novel milling vibration suppression method for thin-walled parts. The present work focused on the milling vibration control of a thin-walled workpiece using a semi-active magnetorheological (MR) damper. The forward dynamic model and inverse control model of the MR damper were first established, and its actuating position on the workpiece was then determined by modal analysis. The dynamic model of the MR damper at this position was built based on the proposed dynamic parameter acquisition method and used in the following semi-active control algorithm design. The effectiveness of this algorithm was verified by MATLAB/Simulink simulations. Finally, six groups of milling experiments were carried out using the non-damper, the rigid rod, the damper applied with 1-, 2-, and 3-A currents, and the semi-active control damper to validate the practical effect of the proposed algorithm. It was found that the designed semi-active control MR damper outperformed the constant-current control dampers or the rigid rod. In comparison to the non-damper experiment, the root mean square (RMS) values of milling forces in x- and y-directions decreased by 45.12% and 48.58%, respectively, and surface roughness decreased by 40.22%.
更多查看译文
关键词
Thin-walled workpiece,milling vibration suppression,equivalent dynamic parameters,MR damper,semi-active control
AI 理解论文
溯源树
样例
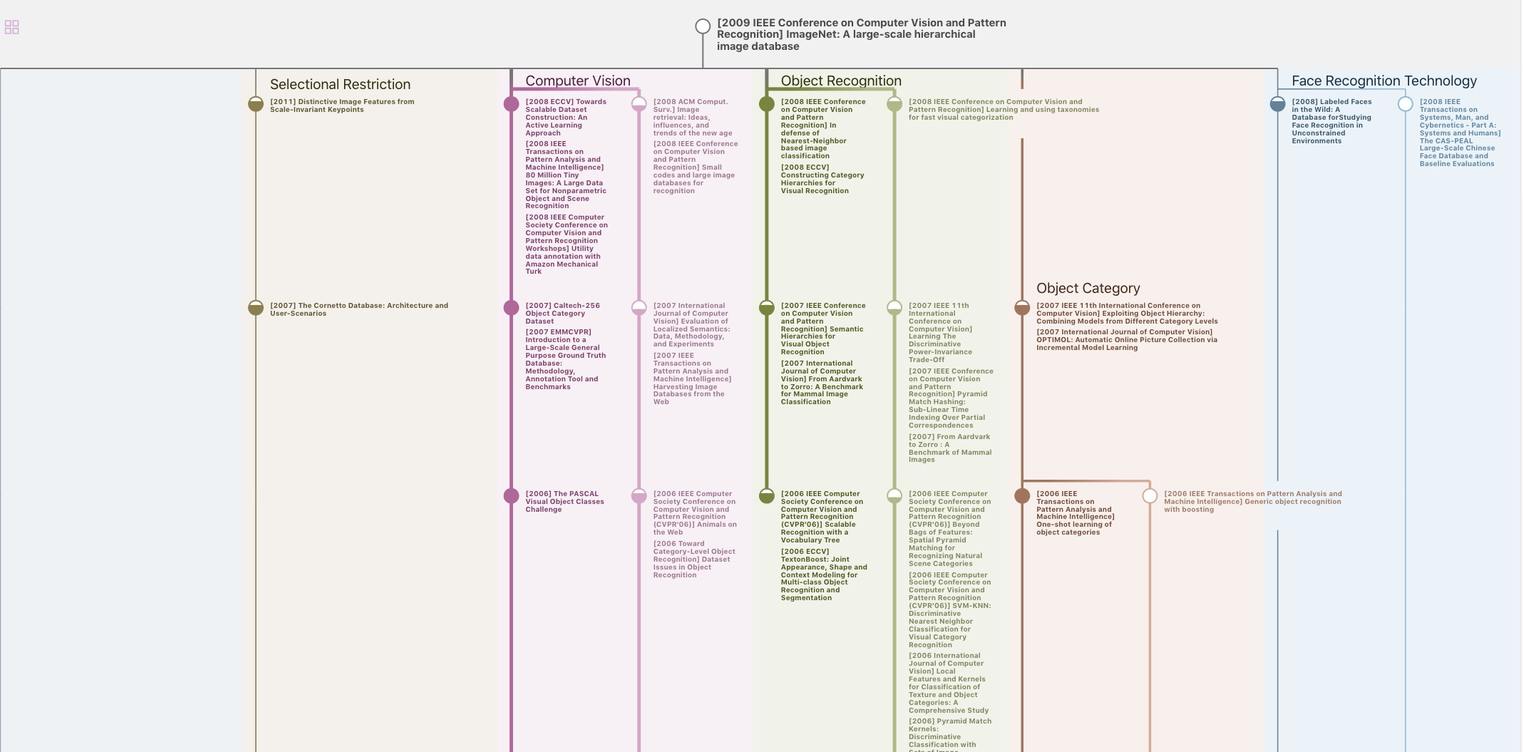
生成溯源树,研究论文发展脉络
Chat Paper
正在生成论文摘要