Analysis of the wear characteristics of multi-directional die forging and forming dies for a railway wagon bogie adapter
The International Journal of Advanced Manufacturing Technology(2022)
Abstract
This paper evaluates the influence of the combined die motion scheme and forging process parameters on the evolution of the wear pattern of forging dies for the railway wagon bogie adapter based on an improved Archard model. The simulation results show that the distribution of die wear parts during the hot forging process of the railway wagon bogie adapter is uneven but symmetrical, and the maximum wear parts are mainly distributed in the ring belt part of the top die and the shoulder part of the bottom die, and the maximum wear amount of the top die is about 1.4 times that of the bottom die. In addition, the influence of the initial forging temperature ( T w ) and the preheating temperature ( T d ) on the wear behaviour of the die during the forging and forming of the adapter was investigated, and a combination of high T w and low T d was found to be more beneficial in reducing the wear of the die. In order to obtain the optimal process parameters, a response surface model of die wear was established and combined with a genetic algorithm-back propagation (GA-BP) to optimise the forging process parameters and proposed an optimal strategy to reduce die wear.
MoreTranslated text
Key words
A railway wagon bogie adapter,Multi-directional die forging,Die wear,Die combination movement,GA-BP neural network
AI Read Science
Must-Reading Tree
Example
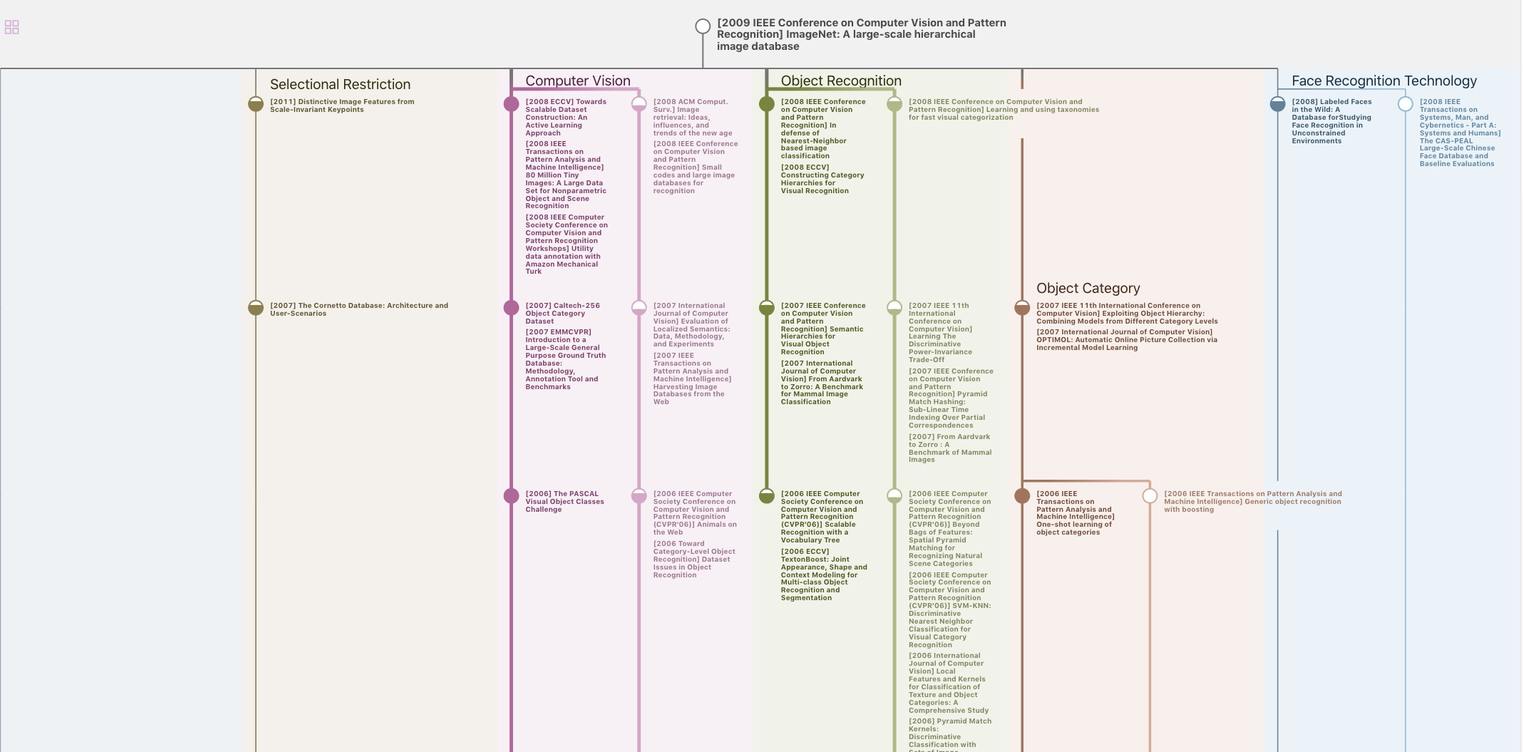
Generate MRT to find the research sequence of this paper
Chat Paper
Summary is being generated by the instructions you defined