Numerical simulation through Fluent of a cold, confined and swirling airflow in a combustion chamber
EUROPEAN JOURNAL OF MECHANICS B-FLUIDS(2022)
Abstract
The study focuses on modelling a cold, confined and swirling airflow in a magnesium burner. Direct observations of the magnesium combustion in the combustion chamber proved the existence of a significant recirculation zone in the burner. Before modelling the high flame temperature and the turbulent mixture of solid fuel and products in this burner, the correct simulation of a high swirl cold flow and the creation of a recirculation zone is a crucial first step. Experimental measurements were made placing a hot-wire anemometry at different positions in a PMMA replica of the burner, to validate the simulation results returned by the Fluent software. In a low swirl case (S=0.13), simulations performed using different eddy viscosity models were compared and the standard k-epsilon model was proved to more accurately predict the velocity profiles and the central recirculation zone. In a high swirl case (S=2.94), the turbulence and its anisotropy were too strong and the RSM model was proved to more accurately predict the position, size and shape of the central toroidal recirculation zone. Important errors were still observed for the velocity values. Higher discretization orders (second-or higher-order) could not be used in this case, due to induced numerical instabilities. (C) 2022 Elsevier Masson SAS. All rights reserved.
MoreTranslated text
Key words
Swirling airflow, CFD simulation, Fluent software, Magnesium burner, Recirculation zone
AI Read Science
Must-Reading Tree
Example
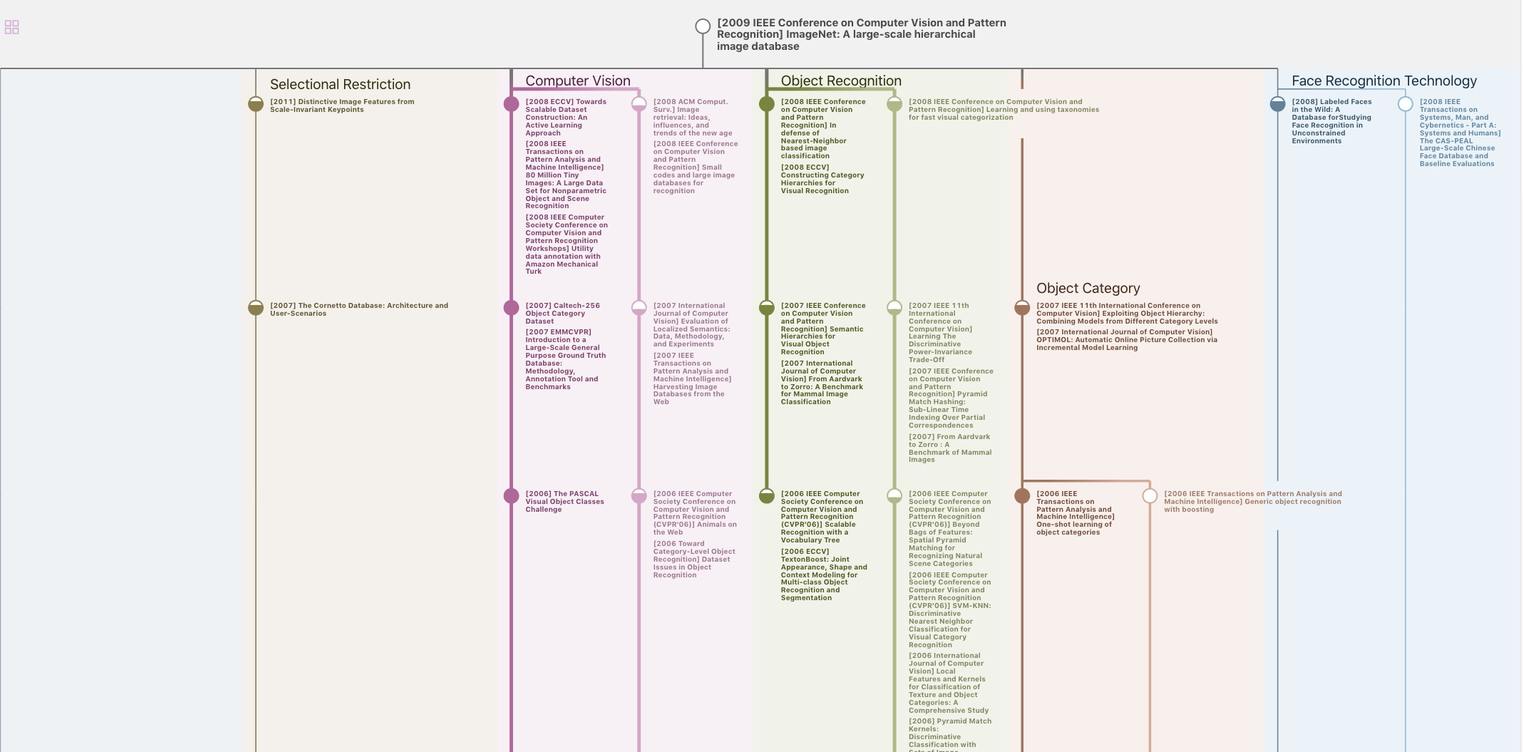
Generate MRT to find the research sequence of this paper
Chat Paper
Summary is being generated by the instructions you defined