Correlating tool wear to intact carbon fibre contacts during drilling of continuous fibre Reinforced Polymers (CFRP)
Materials Today: Proceedings(2022)
摘要
Drilling holes to facilitate the mechanical joining of CFRP assemblies is a key operation for many high value products, especially in aerospace manufacturing. Tool wear continues to remain a significant operational problem and the extant research indicates that this wear initiates at the cutting edge due to the abrasive contact between the reinforcing fibres and the tool surface. While there have been efforts made to characterise and understand the wear process, the current literature lacks an explanation on the most logical influential parameters affecting it. Here, in this work, a novel method of calculating the idealised number of abrasive contacts between the reinforcing fibres of the workpiece and the tool is demonstrated. Sequentially, a systematic experimental study is designed to measure how tool wear is influenced by the calculated number of abrasive contacts and how wear shape varies, from an initial pristine cutting edge to a worn geometry. The experiments showed a consistent “waterfall” wear shape, the magnitude of which grew with the number of intact fibre-tool contacts. The study establishes that wear is focused on the flank face, while the junction with the rake face occurs at a repeatable radius in each experimental trial. The results also showed that the tool wear increases as a function of both drilled depth and drilling contact time, independent of drilling speed and feed, but notably, the wear magnitude does not scale proportionally with the number of idealised intact fibre-tool contacts.
更多查看译文
关键词
CFRP,Drilling,Abrasion,Tool wear,Edge rounding,Thermal Imaging
AI 理解论文
溯源树
样例
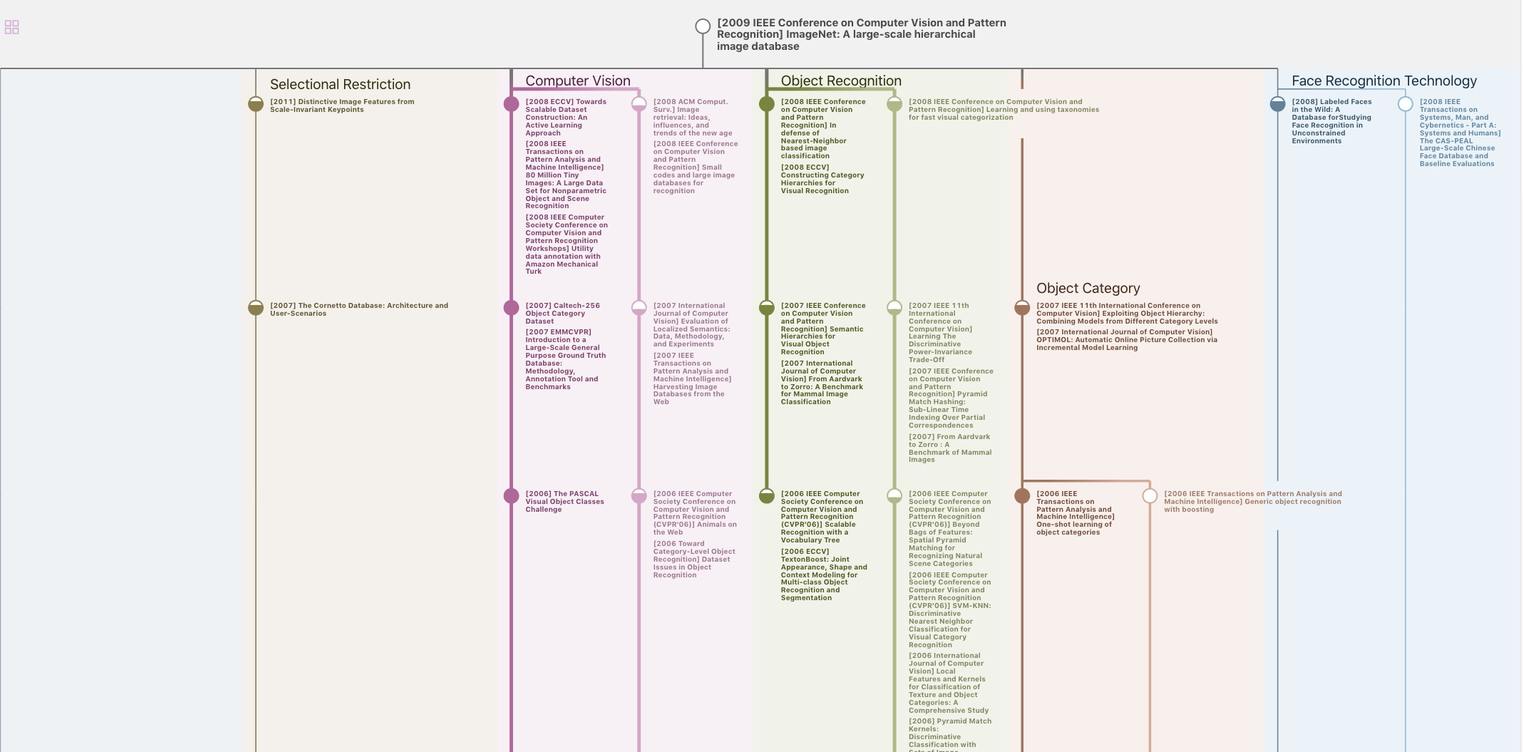
生成溯源树,研究论文发展脉络
Chat Paper
正在生成论文摘要